Using Digital Twin technology to improve inspection methods of high risk assets
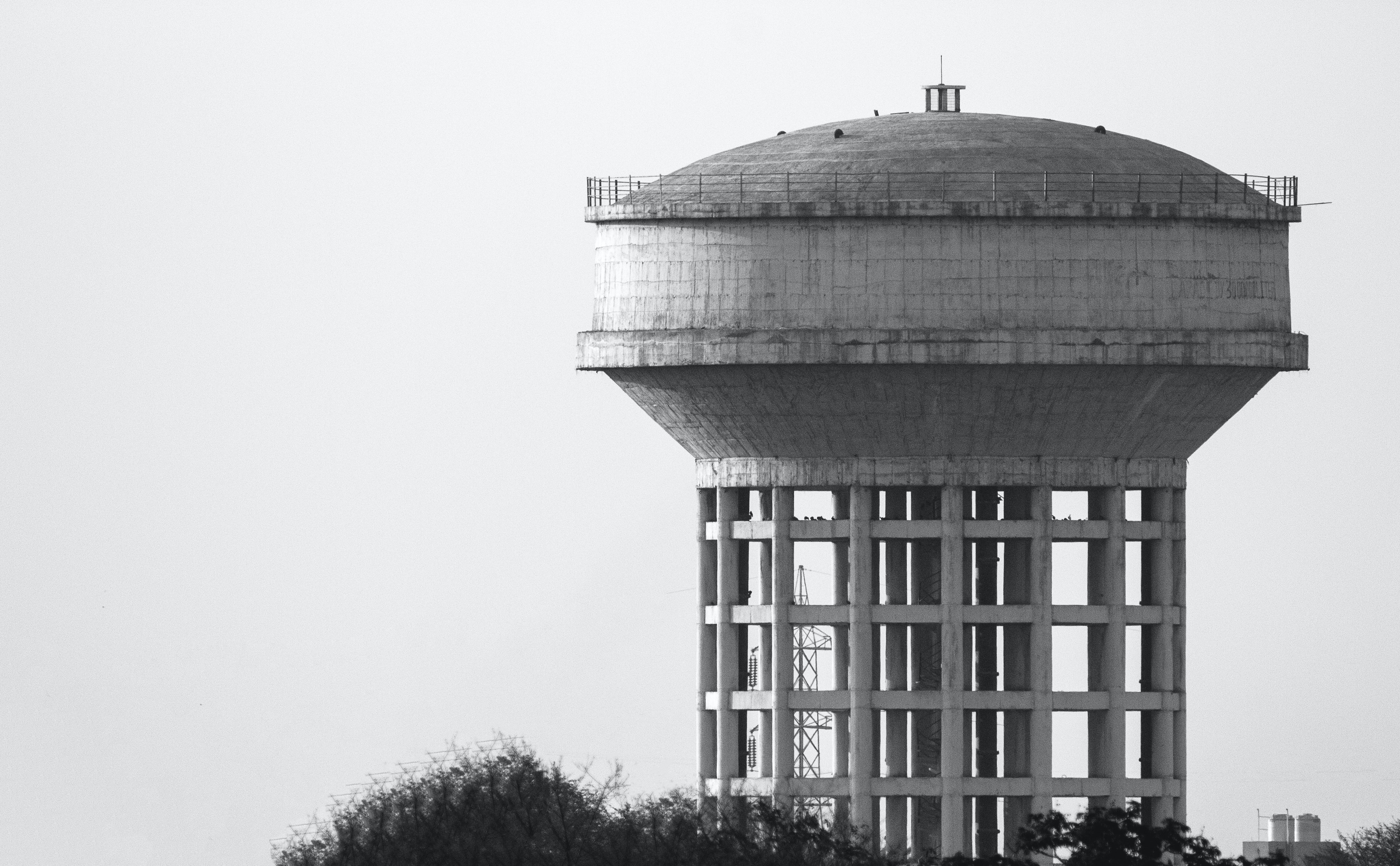
First published in Water e-Journal Vol 6 No 4 2021.
Digital Twin technology has increased the safety of personnel, improved data quality and drastically decreased the time and money spent inspecting each asset.
DOWNLOAD THE PAPER
Abstract
Digital Twin (DT) technology has changed the way critical in-service assets such as elevated potable water tanks are inspected and condition assessed. With the advent of remote inspection practices, only minimal operational intervention is required to assess the asset deterioration. This facilitates timely asset inspections that can be achieved with a high degree of accuracy in the Operational Asset Management (OAM) process. The in-service assets team at Water Corporation has confirmed the use of remote inspection techniques to produce asset DT improves safety and reduction in inspection cost when compared with conventional inspection approaches. One of the advantages of using DT is that the defects on the assets are located with a higher degree of accuracy. The defects are geo-tagged and labelled which can be used for timely intervention and renewals decisions.
Introduction
Water Corporation owns and operates water, wastewater and drainage infrastructure in Western Australia. There are ground level and elevated concrete tanks with varying capacity and configurations, and these types of assets are ageing. With the lack of quality inspection and condition assessment data, the detailed asset health is still unknown and hence the likelihood of failure is deemed to be high.
Historically, the use of Remote Visual Inspection (RVI) was limited to the internal inspection of pipelines. Improvement in Drone and battery technology however, has paved the way to use RVI for other asset classes. The COVID-19 pandemic expedited the increased use of RVI’s in the water industry.
In some instances, RVI has eradicated the traditional methods of inspection that involved sending inspectors into high-risk locations. For Water Corporation, the benefits of using Digital Twin technology include personnel safety, reduction in the number of inspectors and cut down travel time to sites, thereby saving time and money.
Above all, the inspection data quality enables the end user to visualise and assess the condition of the asset from the comfort of their office.
The term Digital Twin is a digital representation of the asset in the real world. A DT will enable the end user to visualise the asset, track changes, and perform analysis to better understand and optimise asset performance. CSIRO (Data 61) defines the DT technology as, “an open platform that can visualise 3D and 4D data over time such as buildings, strata plans, terrain, property boundaries, utilities, including power, water storage tanks and pipelines”. DT’s can be continuously updated with data from a number of sources, which is what separates them from traditional 3D models. Users at all stages of the asset’s lifecycle can make more informed decisions for better outcomes [1].
DT also provides the opportunity to utilise predictive, rather than reactive, maintenance programs of the in-service assets. The combination of virtual and physical worlds [Figure 1] allows accurate asset condition data analysis and monitoring of entire systems to prevent problems before they occur [Figure 2]. This means the prevention of asset operational downtime, and also develops asset designs using simulations. Water Corporation has trialled DT technology for elevated concrete tanks, and successfully embedded the application in their condition assessment process.
Figure 1: Physical and Virtual worlds interaction in the Digital Twin creation
Figure 2: Digital Twin (concrete ground level tank - 2021)
The Digital Twin Technology
Water Corporation collects vast amounts of data across a range of asset types each year. Harnessing large amounts of data and using technology to visualise and interact with assets has become a key focus. The development of DT technology allows organisations to deal with their historical data, but more importantly, provides a visualisation platform where complex post inspection analysis can be made, and real time data can be viewed.
The DT resides in a cloud-based platform and is maintained throughout the asset lifecycle; available across the organisation at all times. It becomes the single source of asset information and location of other services that interact with the asset (e. g. pipework, valves, pumps, electrical cables etc.).
A DT for water assets is created by using the latest advancements in remote inspection technologies, including RGB sensors, laser scanners, LiDAR, and drones. The data collection process itself has significant advantages over traditional data collection methods. The time required on site is almost halved, and exposure to high risk activities such as working at heights and confined space entry is almost eliminated.
Once the data is captured, it’s processed by reality modelling software packages. The output provides a real-world digital model of the asset in the form of a 3D reality mesh. The mesh is geo-referenced to provide precise real-world digital context. The 3D reality mesh is created from overlapping photos captured from drones and ground-based cameras, together with accurate point clouds from laser scanners positioned at key static positions around the asset. This combination provides the user with high levels of geometric accuracy, enabling precise calculations from the DT.
Once created, the DT is exported to a 3D visualisation platform for immersive viewing throughout the lifecycle of the asset. Data can be updated and applied to the DT over time, including real-time sensor information if available.
Digital twin technology removes the subjective nature of traditional inspections, whereby an inspector often uses basic measurement and data capture tools, and transfers the information captured to a basic paper-based notepad. This type of traditional inspection is subject to human error, and the initial measurements and data captured cannot be accurately reviewed or audited. Digital twin technology allows multiple users to not only review the inspectors' comments on the condition of the asset, but also an exceedingly high detail realistic view of the asset itself.
Year Case Study was Implemented - 2017 to 2020
Case Study Summary
In 2018, Water Corporation engaged external contractors to inspect and assess the condition of Mt Tarcoola’s elevated concrete tank in the Mid-West region using 3D Laser technique. Even though the inspections were conducted remotely with improved safety, certain limitations in the inspection techniques, modelling and data tagging restricted the Asset Condition Assessment (ACA) findings. However, the learnings from the Mt Tarcoola tank provided a strong base for the DT approach.
Water Corporation carried out a Level 1 visual inspection using traditional methods on the elevated concrete tank in Joondanna. The asset availability constraints for a longer duration had limited Level 2 detailed inspection, and also scoping for repair works. In late 2019, in-service assets trialled inspecting an elevated concrete tank in City Beach using basic DT, where the end user could control the 3D rotation of the asset. Once base line information was obtained, and with continued efforts in 2020, the Halls Head elevated concrete tank [Figure 3] DT was completed [Figure 4].
Figure 3 - Physical Asset
Figure 4 - Virtual Asset created using Digital Twin
Case Study Details
Two elevated concrete tanks of different configurations in the suburbs of Joondanna and Halls Head in Perth Metro were identified for DT technology inspection. Water Corporation Asset Condition Assessment (ACA) panel contractors were engaged to undertake inspections. With additional remote sensing techniques, condition assessments of Water Corporation assets were carried out without the need for traditional support equipment like elevated work platform, scaffolding and cranes. In one tank, conventional hammer tapping was performed to confirm the inspection results obtained through the technology.
On the second tank, conventional hammer tapping was not used at all. These inspection improvements resulted in less time on site, reduced working at risky heights and provided better insights into the asset condition.
The Halls Head tank enabled contractors to further enhance the DT inspection process, including the collection of data from the tank internals. The processed laser scan data and RGB imagery was upload to the 3D viewing platform Pointerra® [2]. Thermal imagery and 4K videos from the caged drone were added as tags.
Detailed Methodology
There are several sensors used to collect the DT data. External aerial imagery is captured using the DJI Matrice® 300 RTK drone [Figure 5] which includes two camera payloads: a full frame ultra-high-resolution camera (Zenmuse P1) and a hybrid wide angle, zoom and radiometric thermal camera (Zenmuse® H20T) [Figure 6]. Larger megapixel cameras (61MP) can be used for the location of hairline cracks. For LiDAR data, the Emesent® Hovermap scanner is mounted to the drone to capture full resolution, 30mm accurate point clouds using its 360 by 360-degree angular field of view LiDAR sensor.
Terrestrial data is captured using a combination of the FARO® Focus laser scanner [Figure 7] and the Emesent® Hovermap scanner (in handheld mode). To support this, a Sony® Alpha A7R IV full frame camera is used to capture multiple 360-degree panoramas inside an asset as well as the entire exterior of the asset using still photography.
Internal drone imagery is captured using the Flyability Elios 2® [Figure 8] caged drone, which records 4K close-up video supported by its 10,000-lumen lighting system and thermal video simultaneously. This combination is especially useful for low-light situations, where previously non-inspectable assets can be inspected completely and with clarity.
The data from these multiple aerial and terrestrial systems are collated and processed using the leading 3D reality modelling software to produce ultra-detailed DT’s. This software utilises machine learning auto-alignment and object recognition technologies to ensure the DT’s produced are as spatially accurate as possible. Furthermore, the final DT’s are geo-referenced in the Pointerra® viewing platform, allowing the end user to see exactly where the asset is in respect to its local and greater environment.
Figure 5 - RPA (drone)
Figure 6 – Thermal Camera
Figure 7 - 3D-Laser Scanner
Figure 8 - Caged drone
Issues Identified
Operating many potable water tanks requires timely inspection and maintenance to preserve the integrity of the water services. Traditionally, condition assessment has involved a site visit to inspect and take photos of specific interest areas. The challenges associated with this approach typically relate to safety of inspectors, the time taken, the cost associated with complex site visits and correlating the captured information to the specific location on the asset. This approach is always subjective, and the end users may not agree with the inspection that was presented to them. At times, this leads to the delay in the capital investment plan for the asset replacement.
Outcomes and Solutions
Recent DT technology trials achieved the following outcomes. They are:
- Eliminated work at height for delamination identification.
- Resolved access limitation to elevated tank.
- 3D digital image provided acceptable visible inspection details for condition assessment.
- Condition rating and defect annotation incorporated into the DT model allowed future reference and maintenance repair planning.
- Allowed new image layer for future inspections to identify changes through visible asset condition inspections.
- Reduced site travel time.
- The DT trial proved a potential cost saving of nearly 45% over the traditional inspection approach. With the availability of cost effective remote inspection equipment and associated software, it is expected the DT inspection cost could still come down further as the technology continues to evolve.
It also reduces the time pressure on the inspector to complete the inspection while on site and while subjected to unfavourable environmental conditions (heat, wind, rain). This time pressure and induced human error can also lead to inaccuracies in the final reporting on the condition of the asset. One of the key planned trials is on-line continual monitoring of the asset condition that can be achieved through the application of Internet of Things (IoT’s) sensors and Artificial Intelligence (AI) to recognise the defect types and map out on the DT.
Lessons Learned and Closure
Currently, physical inspection is removed to a significant extent by using DT technology because it does manual defect annotations and dimension measurement. In future, AI defect detection and mark-up can be used which will save time.
Use of thermal imagery overlay on the DT model had replaced the traditional hammer tapping [Figures 9 and 10]. Also, AI can be used for thermal imagery analysis to improve accuracy and consistency for the interpretation. Paper based defects mark-up plan and photographs are a thing of the past now. This was replaced by the defect list extracted from the DT model [Figures 11 to 13]. This can be integrated into the work management process.
Figure 9 - Thermal Imagery to detect defects and leaks
Figure 10 - Typical Drone thermal images
Figure 11 - Defect identification on the internal of the tank
Figure 12 - Defect location and type on the internals of the tank
Figure 13 - Typical defects marked on the concrete
Acknowledgement
The authors would like to thank and acknowledge the contribution from the following personnel during the project: P. Woods, Snr Prin. Engineer Emerging Technology, Engineering Branch, E. Soon, Senior Project Engineer Perth Region Fields Services, Water Corporation, J. Au, Senior Materials Engineer, GHD Pty Ltd and G. Johnson, Senior 3D Point Cloud Specialist, 4D Delta Pty Ltd, Perth, WA, Australia.
References
[1] Digital twins at CSIRO’s Data 61, From objects and systems to precincts and cities, https://data61.csiro.au/en/Our-Research/Our-Work/Future-Cities/NSW-Digital-Twin/NSW-Digital-Twin].
[2] 3D Data Solved. Actionable 3D information powering digital asset management solutions, https://www.pointerra.com/.
Author Biographies
Venkat Coimbatore | Venkat Coimbatore is a Senior Materials and Corrosion Specialist at Water Corporation, Western Australia. Venkat has more than 27 years of corrosion control and condition assessment experience and worked in Oil and Gas, Mining and Utility. He has B.E. in Metallurgy and M.E. degrees in Corrosion Engineering, is a Chartered Professional Engineer at the Institute of Engineers, Australia. A 26-year member of NACE (now AMPP – The Association for Materials Protection and Performance) and is certified Senior Corrosion Technologist.
Ed Boxall | Ed Boxall is a Remote Inspection Project Manager and Managing Director at Sensorem Pty Ltd. Ed has 25 year’s experience in the aviation industry and holds an Airline and Drone pilots licence, with 14,000 hours of flight operations experience. Since 2012, Ed has managed some of the largest and most complex remote (drone) inspection projects in Australia, including over 1500 Digital Twin asset inspections for Australia’s leading telco provider.