Digital tool for driving circular economy outcomes in the Australian red meat industry
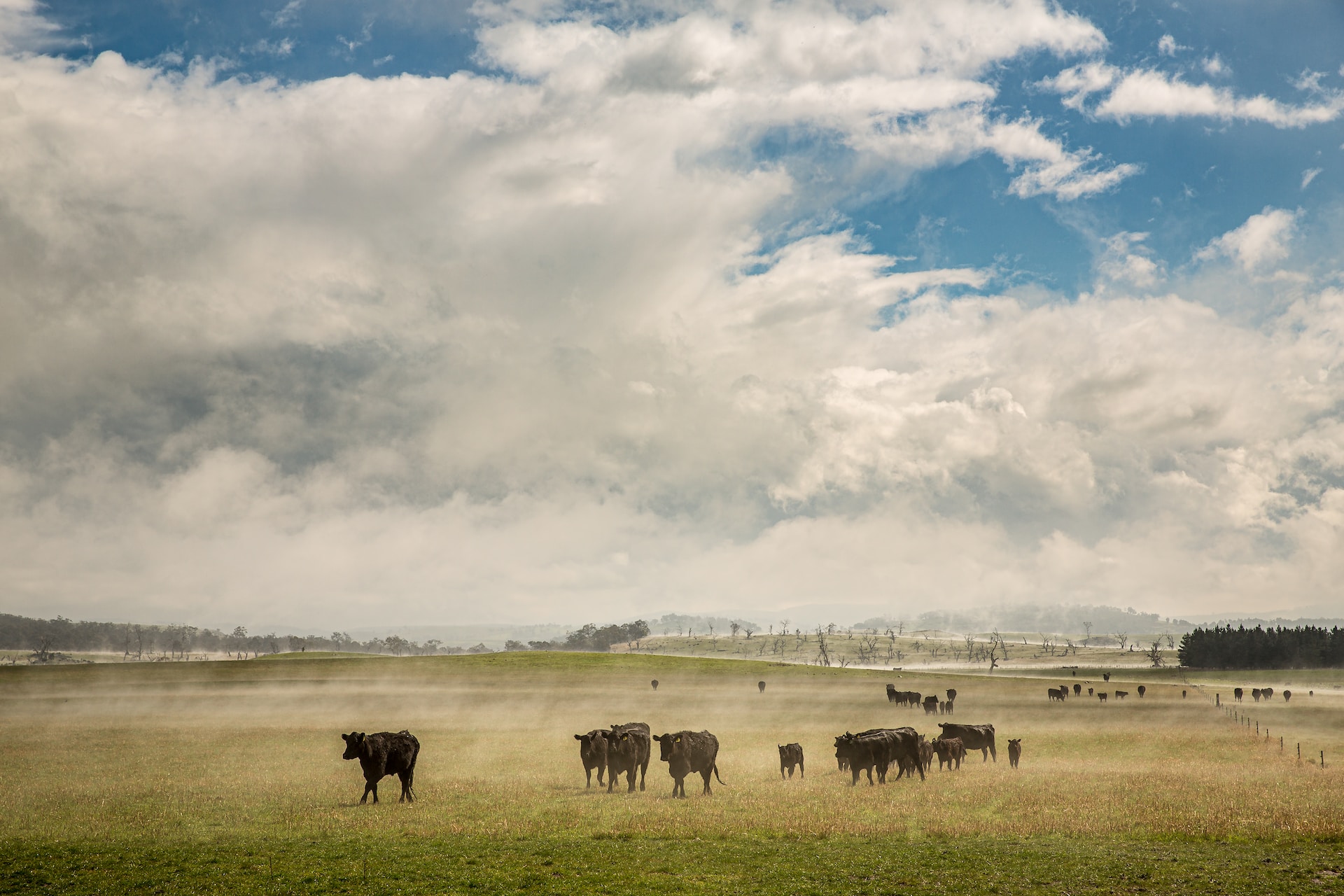
DOWNLOAD THE PAPER
Abstract
This study presents the development of a novel digital tool aimed at facilitating the preliminary sizing and economical evaluation of integrated resource management facilities for wastewater treatment in red meat processing plants. The tool is designed to transform conventional wastewater treatment facilities in these plants into resource recovery plants, with a strong emphasis on enhancing environmental compliance and reducing the overall carbon footprint. Key objectives include the reduction of nutrient emissions, wastewater recycling, waste minimisation, and biogas energy production. The framework for developing this digital tool incorporates considerations of scale, the urgency of wastewater issues outlined by the Environmental Protection Authority (EPA) for Australian red meat processors, and adaptability for plants of varying sizes. By providing decision support for wastewater treatment and waste management, this model aims to assist the red meat processing industry in aligning with net-zero goals through resource recovery and the adoption of a circular economy.
Introduction
The red meat processing sector plays a vital role in Australia’s economy, contributing $17.6 billion to the Gross Domestic Product (GDP) in 2018-19 (MLA, 2022). However, it is also responsible for 11.8% of the country’s greenhouse gas (GHG) emissions. To address this environmental impact and align with global sustainability goals, the industry has set a target to become Carbon Neutral by 2030 (CN30; AMPC, 2021).
Simultaneously, stricter water usage, wastewater treatment, and waste management regulations have been introduced by environmental regulators across Australia. Red meat processors face the challenge of achieving robust environmental compliance while drastically reducing carbon emissions within a short timeframe. Many existing wastewater infrastructure systems are outdated, inefficient, and do not align with the concept of “resource recovery” (Tessele et al., 2020). To overcome these limitations, there is an urgent need for a nationwide tool that can illustrate targeted refurbishment options for wastewater and waste management systems. This paradigm shift would involve replacing pond systems with more efficient, engineered processes that not only improve environmental performance, but also generate income and significantly reduce the carbon footprint (Vellacott, 2016; McCabe, 2012). Although this approach is new in Australia, it has been successfully implemented in Europe and other developed countries.
However, the red meat processing sector lacks expertise in designing, building and operating these advanced systems. The pace of change required to meet compliance and net-zero goals is demanding. Therefore, there is a pressing need for a fast and efficient decision-making process for red meat processing plants (RMPs). By adopting a digital tool specifically tailored to their needs, RMPs can benefit from streamlined initial assessments, enabling faster decision-making. This tool also facilitates the development of concept designs for different scales, ensuring inclusive participation and providing smaller operators with lower investment requirements and potential additional revenue streams.
The development and adoption of a digital tool for the red meat processing sector would not only assist in achieving environmental compliance and net-zero goals, but also enhance the sector’s overall sustainability and economic viability.
Figure 1 shows a 3D representation of the integrated modular bio-resource recovery facility conceived in this model, adaptable for different scales of processing plants.
Figure 1: 3D model showing the integrated bio-resource recovery facility. Modular integrated wastewater, biogas and biofertiliser plants.
This integrated approach can generate impacts beyond the processing facility, being integrated with the community as a training centre, events venue, and part of the local attractions for visitors. This will contribute to the development of higher awareness of the value of what was previously considered waste and normalise the recovery of valuable resources.
By implementing the proposed integrated bio-resource recovery concept developed for the digital tool, the average Australian abattoir can become financially attractive. Non-financial outcomes include:
- Development of a digital tool that informs small, medium, and large-scale abattoirs on their decision-making process on managing waste/wastewater streams from a different lens.
- Increased environmental compliance via reduction of the adverse effects of nutrient emissions to the environment.
- Reduction of wastewater discharged to the environment and of waste diverted to landfills
- Reduction of overall carbon footprint via bio-energy production using organic waste streams.
- Provide a tool for decision-makers to identify and select the most appropriate technical pathway according to the scale of their operations.
- Contribute towards a change in paradigm on how waste streams are managed in Australia.
Figure 2 shows the schematic diagram of the integrated bio-resource recovery facility, the blueprint for the digital tool development. The diagram shows the anaerobic digestion process as a central pillar for achieving bio-resource recovery via adopting a circular economy approach, as described by Tessele and van Lier, 2020.
Figure 2: Schematic diagram of the integrated system, or bio-resource recovery facility used as a basis for the digital tool development, based on Circular Economy principles.
Methodology
The digital tool was developed based on data collected from seven anonymous real-case studies of red meat processing plants (RMPs) across Australia (Table 1) and validated with literature data (AMPC, 2021; Ware and Power, 2016).
Table 1: Facilities assessed by the digital tool
The data provided by the selected participants included:
- Water consumption and type of uses,
- Raw wastewater characteristics and production as well as current issues,
- Energy consumption by source,
- Solid wastes production; and
- Expansion plans.
The technology selection was driven by (i) maximising recovery of high-quality treated water (in compliance with environmental discharge targets); (ii) recovering energy from carbon-rich organic streams; and (iii) production of commercial bio-based fertiliser.
The concept design was developed using excel spreadsheets and Biological Nutrient Removal (BNR) process calculations (Metcalf & Eddy, 2013) for equipment sizing and ancillary calculations. Envirosim’s BioWin 6.2 was used to validate process design and perform sensitivity analysis (evaluation of the plant performance, varying effluent flow rates vs loads.
Concept level cost estimates were developed for each case. The economic analysis, using the Net Present Value method, considered the +/-30% capital expenditure (CAPEX) and operating costs (OPEX). The incomes considered in the analysis included recycled water, energy (from biogas), biofertiliser (biochar, from processed digestate), savings on waste disposal, and carbon credits offset (Figure 3).
Figure 3: Inputs and outputs of the bio-resource recovery facility, red meat industry.
Individualised plant assessments, using the digital tool and supported by wastewater characterisation and plant situational conditions (i.e., species, throughput, climatic), were performed for each of the seven participants. These assessments aimed to demonstrate how the tool can be used to support an accelerated design outcome.
There is an option built into the digital model allowing for calculating the outputs either based on the default wastewater characteristics established for the industry (organic and nutrient loadings), volume flows and situational data or allowing the user to enter their values. The default wastewater quality was based on average values for the case studies and Australian industry averages (AMPC, 2021), divided into three different strengths: Low, Moderate, and High.
The outputs of the modelling served as inputs for creating an online digital tool, that will be made available online for members of the Australian Meat Processing Corporation (AMPC).
Results
The assessed processing facilities were classified into “Small, Medium and Large” based on their production capacity and wastewater production; and their wastewater strength into “Low, Moderate and High” strength, as summarised in Table 2.
Table 2: Processing plants classification according to size (S, M, L) and strength (L, M, H).
Based on the selected case studies, the volume of wastewater produced by the processing facilities varied from 143 to 2,000 kL/ day, as shown in Table 3.
Table 3: Average Waste Water Treatment Plant (WWTP) flows resulting from the assessment of the case
The collected data allowed the classification of the facilities in terms of flow (Small, Medium and Large), and its distribution is presented in Table 4:
Table 4: Classification of scale based on wastewater production ranges
The current average wastewater production intensity (k/tHSCW) is superior compared to the average from the industry (AMPC 2021), staying above the national average with 7.5 vs 6.5 kL/t HSCW; and is consistent with the average consumption reported by the National Greenhouse Emissions Reporting (Australia, 2021), with 7.5 vs 7.8 kL/t HSCW as represented in Figure 4.
Figure 4: Wastewater production per tonne of hot standard carcase weight (kL/tHSCW), compared to the industry. NGER (2021); AMPC (2021).
Although the average obtained for all cases is inside the national water consumption range if considering the individual scenarios, the perspective is different. Most of the individual results of water consumption intensity (shown in Table 3) have a relatively elevated water consumption intensity compared to recent national averages. Consequently, there are opportunities to further reduce water consumption (NRMMC, 2006), and therefore the design has included modular flexibility to adapt to future wastewater production. In case future expansion of the facility is made necessary, the increase of the treatment capacity of the plant and easy integration with the system in operation becomes feasible. Additionally, having parallel treatment trains also allows operational and maintenance flexibility.
Wastewater quality
Wastewater originating from abattoir facilities is typically a rich source of energy, carbon, and nutrients (Jensen and Batstone, 2012). The results showed that small facilities producing sheep/lamb tend to produce more concentrated wastewater streams compared to medium and large facilities with combined cattle and sheep/lamb production. A possible cause for this result is the efficiency of oil and grease separation at the source and lower water used during the process, resulting in less dilution of the abattoir effluent. Table 5 presents the average results of wastewater concentrations identified in the seven case studies.
Table 5: Wastewater quality at the assessed red meat processing plants (all results in mg/L).
Based on the collected data, the resulting classification (Low, Moderate, High) in terms of loads are distributed as presented in Table 6:
Table 6: Wastewater quality at the assessed red meat processing plants (all results in mg/L).
Concept design
The choice of the integrated process design for this project is justified by its alignment with the core concepts aimed at achieving high efficiency, low energy consumption, and maximum resource recovery. These concepts are as follows:
High-efficiency pre-treatment: The design focuses on efficient pre-treatment to recover carbon-rich organic material for processing in the biodigester. This approach not only offloads the wastewater treatment process but also reduces the energy required for aeration. By utilising carbon-rich organic material, the design optimises resource utilisation and minimises energy consumption.
Modular biological nutrient removal (BNR): The integrated process design incorporates a modular BNR system specifically designed for high-efficiency and low-energy nitrogen removal. This targeted approach ensures effective nutrient removal while minimising energy requirements, making it suitable for the project’s objectives.
No biogas recovery from wastewater streams: The decision not to recover biogas from wastewater streams is intentional in this design. By preserving the carbon for the denitrification step and eliminating the need for additional carbon sources, the process maximises the utilisation of carbon within the system, resulting in improved efficiency and reduced energy demand.
Chemical phosphorous precipitation: The inclusion of chemical phosphorous precipitation enables the achievement of very low total phosphorus concentrations in the treated water. This approach not only enhances the quality of the treated water, but also allows for the recovery of phosphorus, a valuable resource.
Ceramic ultrafiltration membranes: The use of ceramic ultrafiltration membranes as a post-treatment after the BNR system ensures the production of high-quality clarified water. This step adds an additional level of treatment to meet the desired water quality standards, promoting the reuse of water for non-potable purposes.
Multi-barrier disinfection system: The integrated process design incorporates a multi-barrier disinfection system to achieve log removals compatible with Class A water standards for non-potable reuse. This ensures the treated water meets stringent quality requirements, allowing for safe and reliable water reuse.
Management of biodegradable solid streams using Co-Digestion Anaerobic Digestion (AD) Plant: The design incorporates the management of all biodegradable solid streams, including sludge from save all/primary dissolved air flotation (DAF), manure, paunch, and waste sludge from the BNR process. These streams are efficiently processed in a Co-Digestion AD Plant, optimising resource recovery and minimising waste.
It is important to note that external waste streams were not considered in this specific integrated process design. However, further studies can assess the site-specific economic viability of Anaerobic Digestion and explore the benefits of adding external wastes to the system. This ensures that the design can be adapted and optimised based on the specific needs and conditions of the project site.
BioWin sensitivity analysis
A total of 15 BioWin simulations were performed for the medium and large-scale systems (five cases), aiming to test the robustness of the designed system when facing loading changes. The sizing was performed based on the “Moderate” strength, with subsequent validation of the system via BioWin modelling. Then, for each case, two additional scenarios changing the effluent to Low and High strengths, were tested on the BioWin, while keeping the initial wastewater treatment plant sizing.
The steps adopted in the simulations were:
- Design flow rates, based on wastewater currently produced in the facility.
- Preliminary sizing, design of the system using Excel spreadsheet and moderate effluent strength.
- The input of preliminary sizing to the BioWin for validation of the WWTP design.
- Additional validation of the model for low and high effluent strength.
The highest water quality (high risk) was considered as the target parameter for the model evaluation. After simulation, the model was validated for all cases using current flow rates and testing different flow strengths. To validate the designed wastewater treatment plant, the result was compared to target parameters. All the simulations have presented results inside the targeted treated effluent parameters. The outputs of the BioWin modelled treated water results for the various scenarios are shown in Table 7.
Table 7: Sensitivity analysis: Treated effluent quality scenario outputs from BioWin simulation. Low (L), moderate (M), and high (H) effluent strengths, for five medium and large facilities.
Economic analysis
The economic assessment is based on several assumptions and considerations, which are as follows:
Net positive outcomes over 25 years: The economic analysis indicates that the project is expected to generate positive financial returns over its entire 25-year lifespan. This suggests that the investment in the integrated resource management facility is financially viable and has the potential for long-term profitability.
Payback time and annual return on investment (ROI): The estimated payback time for the project ranges from 5 to 10 years. This means that the initial investment is projected to be recovered within this timeframe. The annual ROI is estimated to be between 2% and 5%, depending on the scale and location of the facility. These figures provide insights into the profitability and financial performance of the project.
Cost estimate calibration: The cost estimate curves used in the economic assessment are calibrated using literature data from relevant studies (Guo et al., 2014; Jalab et al., 2019). This calibration ensures that the cost estimates are realistic and representative of the industry standards and prevailing market conditions.
Regular updates of financial inputs: The model used for the economic assessment will be regularly updated with current financial inputs. This ensures that the analysis remains up-to-date and reflects any changes in costs, market conditions, or financial parameters that may impact the project’s financial performance.
Efficiency with scale increase: The analysis shows that as the production scale increases, the present value of total expenditure (TOTEX), which includes capital expenditure (CAPEX) and operational expenditure (OPEX), becomes more efficient. This suggests that larger-scale operations are more cost-effective, leading to improved financial performance.
Net present value of TOTEX intensity: Figure 5 presents the curve of the net present value of the TOTEX intensity over 25 years of operation, expressed in dollars spent per tonne of hot carcase weight processed per annum ($/t HSCW). This metric provides insights into the cost efficiency of the facility over its operational lifespan.
It is important to note that the cost estimate curves and financial inputs used in the analysis are based on a combination of five points of cost estimates from 2021, adjusted using modelling based on literature data. This approach ensures that the analysis captures a range of cost scenarios and is grounded in realistic and relevant industry data.
The economic assessment provides a comprehensive evaluation of the financial viability and potential returns associated with the integrated resource management facility, as summarised in Figure 5.
Figure 5: TOTEX intensity, expressed in $ spent per tonnes of hot carcase weight processed per annum ($/t HSCW), over a 25 year project lifetime.
Digital tool
The digital tool, developed initially in Excel and later coded in JavaScript, is designed to be accessible through the AMPC webpage for the organisation’s membership base. It features a user-friendly interface that allows for easy data input and convenient access to simulation outputs. The tool aims to provide a seamless experience for users seeking to evaluate and analyse their facility’s resource management potential.
To begin using the tool, the user will be prompted to enter basic details about their facility, as depicted in Figure 6. This step ensures that the simulation considers the specific characteristics and requirements of the user’s operation. Following this, the user will input information regarding production capacity and effluent quality data, which are essential for accurate analysis.
Once the necessary data has been entered, the simulation will be performed, and the user will be directed to the results page. The tool will generate relevant outputs based on the provided inputs and calculations performed. These outputs can include metrics related to resource recovery potential, environmental compliance, carbon footprint reduction, and economic feasibility, depending on the specific objectives of the tool.
Figures 6 to 9 showcase some typical interfaces between the user and the webpage of the digital calculator, providing a visual representation of the user’s interaction with the tool. The user-friendly interface, combined with the seamless data input process and easy access to simulation results, ensures that users can navigate the tool effectively and derive meaningful insights from the analysis.
![]()
|
![]()
|
|
Figure 6: Screenshot of the input user details, which is followed by the detailed plant inputs. | Figure 7: Screenshot of the process results and system classification. |
![]()
|
![]()
|
|
Figure 8: Screenshot of the process outputs and Recycling opportunities. | Figure 9: Screenshot of the economic analysis outputs. |
The digital tool serves as a powerful resource for red meat processing plants, enabling them to assess their resource management potential and make informed decisions to optimise their operations.
Three main results pages are presented: (i) System Classification (Figure 7), which will classify the size of their facility, the recommended type of system, average wastewater production and footprint required to install the recommended system; (ii) Recycling (Figure 8) will present the major physical outputs of the facility (energy in form of heat and electricity, recycled water and biofertiliser produced; and (iii) Financials (Figure 9) which will provide an estimate of the CAPEX, OPEX, payback period and ROI, all based on the initial inputs and simulated results.
In addition to the results presented on the webpage, the digital calculator has been equipped with an option for generating a report including all the data assessed and the outcomes produced. The purpose of this report is that after the simulation exercise, results can be shared with the user’s team, and decision-makers in their respective facilities, to decide whether this type of system can be further developed and ultimately implemented after a detailed assessment and design.
Next steps
The adoption of the digital tool is going live in the second half of 2023. In parallel to that, the first full-scale model of a bio-resource recovery centre is currently going through engineering stages and will help to feed back more accurate information to the model, once operational. The implementation will include a rigorous peer-review process and detailed market analysis for the side-products offtake and revenue (water, biochar, energy).
Conclusions
In conclusion, the development of the digital tool for integrated resource management in the Australian red meat industry represents a significant step towards embracing circular economy principles and realising the benefits associated with resource recovery. This project was the result of a collaborative effort between processing plants, the AMPC and consultants, driven by a deep understanding of the industry’s unmet needs.
The integration of wastewater treatment with a biogas plant presents a unique opportunity to address multiple challenges simultaneously. By processing red meat wastewater and organic solid wastes, the facility can produce high-quality water suitable for recycling purposes. Additionally, the on-site processing of organic solid waste generates biogas, which can be converted into valuable forms of energy such as electricity or heat. Moreover, the resulting digestate can be used as a fertiliser, closing the loop on resource utilisation.
The developed digital tool enables easy assessment and evaluation of different scenarios for integrated resource management across various scales of abattoirs. It incorporates best practices and waste management strategies tailored to the specific operational requirements of each facility. The tool provides insights into costs, complexity levels, returns on investment, and carbon offsetting opportunities, allowing decision-makers to make informed choices.
Validation of the digital model was performed using real case studies from operating abattoirs, ensuring its applicability and relevance to the Australian context, including climate and regulatory considerations.
Overall, the digital tool fills a crucial gap in the red meat industry’s journey towards achieving net-zero carbon emissions and robust environmental compliance. By embracing a bio-resource recovery approach, underpinned by circular economy principles, the tool facilitates the transition towards a more sustainable and resource-efficient industry. It empowers stakeholders to make informed decisions, optimise resource utilisation, and contribute to a more environmentally conscious and economically viable future for the red meat sector.
Acknowledgements
This work is being funded as a “Core Project” by the Australian Meat Processor Corporation (AMPC). Special thanks to Matthew Deegan (AMPC) for their continuous support and commitment to a low-carbon future. We are also grateful to the participant processing facilities who assisted our team with opening their facilities for site visits and providing the necessary information as input for this work.
The Authors
Fabiana Tessele
Fabiana, a dedicated water and wastewater treatment expert, has spent the past two decades spearheading projects worldwide. With a strong commitment to water, resource recovery, and environmental protection, she believes that inclusive, collaborative, and well-planned water management is crucial for long-term water security. Based in Perth, Fabiana is the owner of Tessele Consultants, specialising in integrated water and energy systems, resource recovery, and Circular Economy Advisory, with clients ranging from water utilities to the red meat industry, fertilisers, and mining. She brings a wealth of experience as a former board director of the Australian Water Association and as a member of the International Water Association’s management committee for the specialist group on anaerobic digestion.
References
AMPC 2021. Environmental Performance Review (EPR) for the Red Meat Processing (RMP) Industry. V.MFS.0448. All-Energy Pty Ltd.
Australia 2021. National Climate Resilience and Adaptation Strategy 2021 – 2025. Positioning Australia to better anticipate, manage and adapt to our changing climate.
DAFF 2008. AQIS Meat Notice, 2008/06. Efficient Use of Water in Export Meat Establishments. Department of Agriculture, Fisheries and Forestry. Australian Quarantine Inspection Services.
DoH 2011. Guidelines for non-potable uses of recycled water in Western Australia. Government of Western Australia, Department of Health.
Guo, T., Englehardt, J., and Wu, T. 2014. Review of cost versus scale: Water and wastewater treatment and reuse processes. Water Science and Technology, 692), 223-234.
Jalab, R., Awad, A., Nasser, M., Miner-Matar, J., Adham, S., and Judd, S. 2019. An empirical determination of the whole-life cost of FO-based open-loop wastewater reclamation technologies. Water Research 163, 114879.
Jensen, P. Batstone, D. 2012. Energy and Nutrient analysis on Individual streams. Meat & Livestock Australia.
McCabe, B. 2012. Using Covered Anaerobic Ponds to Treat Abattoir Wastewater, Reduce Greenhouse Gases and Generate Bioenergy. Meat & Livestock Australia.
MLA 2022. Meat and Livestock Australia. The red meat industry. Download www.mla.com.au.
Metcalf & Eddy 2013. Wastewater Engineering: Treatment and Resource Recovery 5th Edition.
NGER Australia 2021. National Greenhouse and Energy Reporting Determination.
NRMMC, 2006. Australian Recycled Water Guidelines. National Resource Management Ministerial Council, Environmental Protection Heritage Council, Australian Health Ministers Conference.
Ware, A. and Power, N. 2016 Biogas from cattle slaughterhouse waste: Energy recovery towards an energy self-sufficient industry in Ireland Renewable Energy 97 2016) 541e549
Tessele, F. Tedesco, G, Bertizzolo E. 2020. Sustainable Management of Waste and Wastewater Streams at V&V Walsh. Pip 2020-1030. Australian Meat Processor Company.
Tessele, F. and van Lier, J.B., 2020. Anaerobic digestion and the circular economy. A Systemic Approach to the Circulation of Resources. Water e-Journal Vol 5 No 3 2020.
AMPC, 2017. The Ecoefficiency Group Pty Ltd, Johns Environmental Pty Ltd. Guideline for Water Recycling and Reuse in Red Meat Processing. Australian Meat Processor Company.
Vellacott, A. and Sharland, D. 2016. Advances in wastewater treatment – reducing energy use while improving effluent quality.
Warnecke, M. Farrugia, T. Ferguson, C. 2008 Review of abattoir water usage reduction, recycling, and reuse. Meat & Livestock Australia.