Thermal treatment of South East Water biosolids to solve disposal challenges
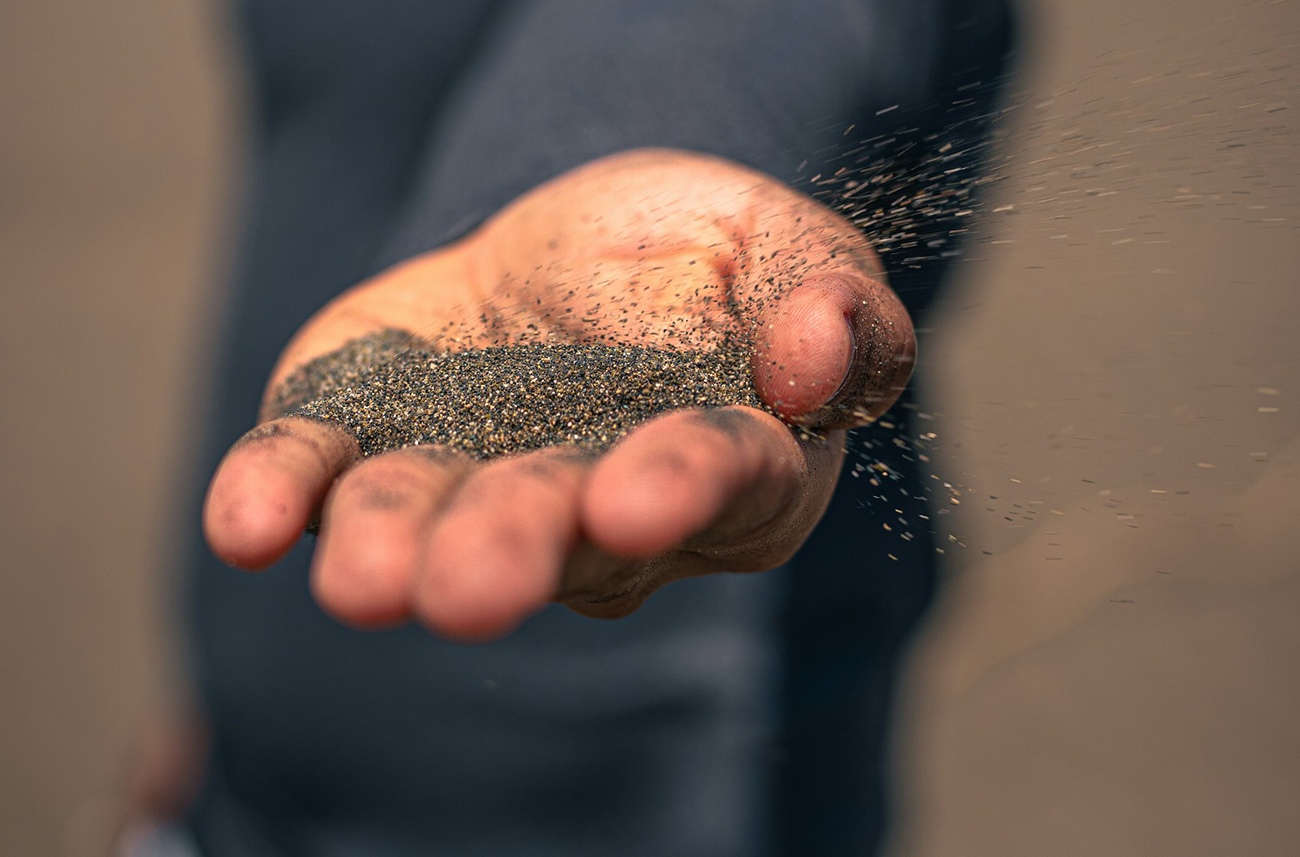
Key points
- PYROCO is proving to be a cost-effective and environmentally friendly thermal treatment approach to managing biosolids through a unique heat recovery fluidised bed pyrolysis technology, which destroys PFAS and produces high quality biochar.
- With expected limited down time for maintenance, low energy input and costs and extended plant life delivering high quality biochar, PYROCO offers an effective biosolids management solution for water authorities to manage their biosolids needs of the near future.
- In partnership with RMIT, and collaboration with Greater Western Water and Intelligent Water Networks, South East Water has been developing PYROCO for over eight years. PYROCO is a product of foresight and careful development, tested and proven over time. While delivering a solution to tightening regulation, its creation has been in development long before legislative changes were being considered.
Abstract
The tightening of regulation around per- and polyfluoroalkyl substances (PFAS) limits has created barriers to the common practice of biosolids stockpiling and spreading on land. This is impacting South East Water’s biosolids management strategy. A broader approach is therefore required which considers all management options including land application, permanent stockpiles, external processing services and on-site thermal treatment. South East Water is assessing how contaminant destruction, carbon neutrality and beneficial reuse of nutrient content can also feature in the solution. The utility is looking at an advanced fluidised bed pyrolysis process, named PYROCO, developed by RMIT University in collaboration with South East Water, as the answer.
With a number of trials already complete, the thermal treatment of biosolids is proving to be a viable approach for cost effective PFAS destruction and the creation of a beneficial end product in biochar.
With expected limited down time for maintenance, low energy input and costs, and a 25-year plant life, PYROCO offers an effective biosolids management solution for water authorities to manage their biosolids needs of the near future.
Introduction
Changing PFAS requirements
The tightening of regulation around PFAS limits in biosolids and receiving soils in Australia has introduced barriers to the common practice of biosolids stockpiling followed by spreading on land, impacting South East Water’s biosolids management strategy.
Prior to the release of the Draft PFAS National Environmental Management Plan 3.0 (NEMP 3.0, 2022), the Victorian EPA adopted the Queensland End of Waste Code Biosolids for PFAS trigger values in soil after biosolids land application in 2021. These soil PFAS trigger values are summarised in Table 1.
Table 1: Queensland End of Waste Code Biosolids soil PFAS trigger values
Prior to the Queensland End of Waste Code Biosolids, the application rate of biosolids to agricultural land was based on Nitrogen Limiting Application Rate (NLAR), which is the maximum rate at which biosolids can be applied without exceeding agronomic requirements. Since the nitrogen requirement is higher for pastures (250 kg/ha), South East Water biosolids application rates were reasonably high and therefore receiving soils after biosolids application were expected to exceed soil PFAS trigger values in Table 1. Recently the revised PFAS NEMP 3.0 (Version 2) also provided soil PFAS trigger values as allowable MASCC (maximum soil contaminant concentrations) as well as criteria for biosolids PFAS (PFOS+PFHxS and PFOA) based on three margins of safety (refer Table 2).
Table 2: Criteria for PFOS+PFHxS and PFOA in biosolids and maximum allowable maximum soil contaminant concentrations (MASSC) based on 1,2 and 5-fold margin of safety (NEMP 3.0 Version 2)
Note: a. The default MOS is 1. b. The PFOA criteria are based on the interim soil ecological indirect exposure guideline value for PFOA. c. The unrestricted use threshold may not be applicable in all jurisdictions. Where it is applicable, it should be applied to the final biosolids product for land application.
Compliance with the Queensland End of Waste Code Biosolids (2021) and NEMP 3.0 Version 2 (2024) will result in reduced application rates and therefore reduced nitrogen being provided to South East Water biosolids customers. Also, based on the levels of PFOS+PFHxS and particularly PFOA within the bulk of South East Water’s biosolids, biosolids land application under NEMP 3.0 Version 2 will not be feasible. South East Water has therefore recently suspended the biosolids land application program due to the release of the draft per- and poly-fluoroalkyl substances National Environmental Management Plan (PFAS NEMP) version 3.0 for public consultation by The Heads of Environmental Protection Authorities of Australia and New Zealand. Generally, biosolids land application is becoming less favourable across developed countries due to PFAS.
A broader biosolids strategy is therefore required which considers all management options including land application, permanent stockpiles, external processing services and on-site thermal treatment. Biosolids heat treatment is now rapidly emerging as a water industry technology to solve challenges of product value, contaminants of emerging concern (e.g. PFAS) and for carbon sequestration.
Method
South East Water PYROCO Journey
South East Water is fortunate to have started a process to consider a plan B approach to biosolids management from 2015. In consultation with RMIT, a review of gasification and pyrolysis solutions for the conversion of biosolids to biochar was undertaken in 2016/17 and a research-based desk top study into the potential for a fluidised bed heat recovery process began. Based on the review, and in the absence of a mature, efficient and cost-effective gasification or pyrolysis market offering, a decision was made to fund a pilot plant based on the successful preceding desk and small-scale trials with RMIT. The pilot plant known as Mark 1 was built and operated for approximately one month in 2021. Located at Greater Western Water’s Melton Treatment Plant, the Mark 1 pilot plant successfully converted South East Water biosolids and Greater Western Water’s biosolids to biochar at a rate of 20kg/hr dried biosolids at 85% total solids. (Drying was undertaken off site in an oven to facilitate trials) Based on the success of this pilot, South East Water approved a business case for $5.64M to develop a demonstration production plant with a capacity of 3,000 tonnes per year dewatered biosolids at 50% total solids equivalent.
The business case for the scale up design phase of the pyrolysis reactor (PYROCO) was approved in 2022, and detailed design phase began soon after. The unique PYROCO fluidised bed heat recovery design includes an inner pyrolysis zone with syngas discharged to an outer zone for partial combustion, and combusted gas passed through inner tubes as an additional heat source to the pyrolysis zone. The addition of heat from the combustion zone and the inner tubes provides the high heat transfer coefficient and means the reactor can scale significantly without loss of efficiency. Large, fluidised bed reactors exist in other industries. On this basis it is anticipated that the PYROCO technology will be able to scale up significantly providing a great opportunity for cost effective biosolids management at scale. The PYROCO reactor indicative design is included in Figure 1 below.
Figure 1: PYROCO reactor design
In early 2023 an opportunity arose with Department of Energy Environment and Climate Action (DEECA) funding for a co-pyrolysis trial with a Mark 2 pilot plant utilising the learnings from the Mark 1 pilot plant. The Mark 2 project was a collaboration between South East Water, RMIT, Intelligent Water Networks, Greater Western Water, Barwon Water, East Gippsland Water and Westernport Water. This Mark 2 DEECA project facilitated the introduction of a wet gas phase treatment design including novel vertical thermal oxidiser and full gas phase emissions testing to establish the faith of PFAS and other contaminants. The process flow design for the PYROCO Mark 2 pilot plant is detailed in Figure 2.
Figure 2: Process flow design for PYROCO Mark 2 pilot plant
The Mark 2 plant included a fluidised bed gas producer which generates all the near oxygen free fluidising gas for pyrolysis within the PYROCO reactor. Therefore, no expensive imported oxygen free fluidising gas is required. The PYROCO reactor receives approximately 90% of the biosolids feed with the remainder going to the gas producer. This feed ratio flexibility allows biosolids with varying calorific value to be processed.
The design includes modest chemical dosing for nitrogen oxides and sulfur oxides removal in addition to thermal oxidiser at 850 to 900 Celsius for two seconds for PFAS destruction. Liquid petroleum gas is used at start up and for the pilot light only, during normal operation with the calorific value of biosolids generally providing all thermal energy requirements. The Mark 2 plant also included additional process automation and biochar continuous removal and cooling.
The Mark 2 plant was fabricated off site in early 2023 and a trial of approximately two weeks completed in November that year, which converted four biosolids, one Food Organic and Garden Organic (FOGO) and one biosolid plus canola straw mix in pellet form to biochar. The reactor achieved 25 kg/hr dried pellet feed rate and facilitated detailed gas emissions compliance testing. The Mark 2 plant in situ at Melton is shown in Figure 3.
Figure 3: PYROCO Mark 2 plant at Melton
The Mark 2 plant is made up largely of stainless steel tubes with no moving parts within the thermal reactors. The relatively consistent and low temperature of pyrolysis at 550 to 600 Celsius allows more cost effective, less exotic stainless steel products to be utilised. The use of tubes within tubes for the reactor reduces the build cost. Maintenance costs are minimised with ease of access and no moving parts in the thermal zone and should result in less downtime and longer plant life than alternative processes with moving parts in the thermal zone, such as augers and rotating hearths.
Uniform pyrolysis at 550 to 600 Celsius in PYROCO provides consistent quality biochar specific characteristics. The characteristics that make a particular biochar valuable include surface area, functional groups, cation exchange capacity, ability to be functionalised and moisture holding ability. The nature of the thermal process influences these characteristics. Low temperature pyrolysis at 550 Celsius as with PYROCO improves functional groups, cation exchange capacity, ability to be functionalised and moisture holding. We therefore anticipate the future biosolids derived biochar from the PYROCO reactor will benefit industry trials with maximised value.
The footprint of the pilot plant inclusive of gas phase treatment is only 3 x 4 m which is a consequence of the high heat transfer coefficient and vertical design. As the capacity of the reactors will increase with the area of the tubes, doubling of diameter will be a square of the capacity. The footprint for scale up designs will therefore be relatively small.
This Mark 2 pilot operation proved to be a critical step in overall technology maturity with a key project outcome to undertake testing to determine PFAS destruction.
Results
PFAS study
Six feedstocks were tested with the Mark 2 plant namely four biosolids, one FOGO and one biosolid combined with canola straw. PFAS was analysed at the following sampling points.
i. Feedstocks before thermal treatment (x6 solid samples)
ii. Biochars from PYROCO reactor and gas producer (x11 solid samples)
iii. Scrubber water during plant operation (x3 liquid samples)
iv. PYROCO exit during plant operation (x1 gas sample)
v. Thermal oxidiser outlet during plant operation (x1 gas sample)
vi. Scrubber outlet before chimney stack during plant operation (x1 gas sample)
All feedstocks except FOGO contained PFAS prior to treatment, ranging from 4.5-114.3 ug/kg. In majority cases, Perfluorooctanesulfonic acid or PFOS is the predominant PFAS compound. Post treatment none of the 28 PFAS components in biochar samples exceeded the limit of reporting. Similarly, none of the 36 PFAS components in scrubber water samples were detectable. Gas phase analysis revealed non-detectable PFAS concentrations at the thermal oxidiser and scrubber exits. At the PYROCO exit, the sum of enHealth PFAS concentration was 6.8 ng/Nm3. From these results the PFAS destruction percentage within the PYROCO reactor itself before thermal oxidiser was calculated at 96.5%. The sampling at PYROCO exit may have underestimated the PFAS concentrations as it only captured gaseous PFAS and lacked inline filtration for fines. This will be addressed by incorporating an inline gas filter in future trials. As we understand PFAS destruction to be related to temperature, duration at temperature and turbulence, the combustion zone in the PYROCO reactor creates a high temperature rapid mixing zone, so PFAS destruction rate is expected to be high, thereby reducing thermal oxidiser scale requirement.
South East Water business case deep dive
Following the successful operation of the Mark 1 pilot plant in 2021, South East Water approved a business case in early 2022 for the development of a PYROCO demonstration plant at a scale of 3,000 tonnes dewatered biosolids at 50% total solids. This scale equivalent to a reactor feed rate of 230 kg/hr represents approximately 50% of South East Water total current annual biosolids production. The business case considered three business objective pillars. These three pillars were considered separately under the following headings:
- Net Zero Contribution
- Risk Mitigation – PFAS
- Net Present Value over 25 years
The Net Zero Contribution calculation compared the current emissions reporting under the National Greenhouse and Energy Reporting Scheme (NGERS) for biosolids management and the energy consumption and carbon sequestration potential of converting biosolids to biochar using the PYROCO technology. The NGERS scheme requires annual emissions reporting of carbon dioxide equivalent (CO2e) for water utilities. The biosolids management element of this reporting makes estimates of the carbon dioxide (CO2), methane (CH4) and nitrous oxide (N2O) emissions associated with stockpiling of biosolids, transferring to farm sites and application to land including incorporation into the top 75 mm of the soil profile. We tested the biochar from the Mark 1 pilot trial to determine the carbon content of the biochar. We also estimated the efficiency of the process with regard to LPG and electricity use. With the high heat transfer efficiency of the PYROCO process we anticipate a thermal energy neutral process, with small external thermal energy input at start up. We also now have access to 100% renewable energy at our facilities. On this basis we calculated 17% reduction in scope 1 emissions comparing the current stockpiling and land application with conversion to biochar using PYROCO. This is due to a combination of carbon sequestration in biochar, scope 1 emissions avoidance with removal of stockpiles and reduced volume of material for transport. This equates to an estimate of 345 tonnes of CO2e sequestered and 520 tonnes of CO2e avoided for our proposed demonstration plant.
The PFAS risk has been mitigated through the Mark 2 trials with PFAS removed from biochar and not detectable in the gas emissions and scrubber water.
The Net Present Value compared the 25-year capital and operating cost estimates for PYROCO to land application. It was recognised that land application may no longer be a valid comparison with land application option closing. An assessment of offsite treatment and disposal options was considered more applicable. The indicative cost of offsite treatment and disposal is $250 to $400 per tonne, which exceeds recent land disposal costs of around $200 per tonne. In comparison the production of biochar at this modest scale was estimated between $350 - $400 per tonne dewatered biosolids at 50% total solids. This cost was deemed similar to alternative external treatment approaches, which benefit from larger scale. The PYROCO heat recovery fluidised bed has the benefit of scalability without compromising the performance by increasing the number of internal heat transfer tubes. With scale up at 10 times or 50 times the Mark 2 scale achievable, the unit cost per tonne will be significantly reduced and very competitive with anticipated benefits of efficiency, scale, less downtime and long plant life with PYROCO. It is also anticipated to be more competitive to alternative gasification or pyrolysis process offerings at similar scale due to the efficiency and small footprint.
Following the detailed design phase of the PYROCO reactor under the business case and the evidence from the parallel process from Mark 2, a strategic decision was made to invest in a Mark 3 plant to deliver an interim scale up to 100 kg/hr with a focus on integration of a dryer and full automation with six months continual operation to fully develop integration and operation understanding before developing the full commercial scale plant. The business case funding has therefore been transferred to this revised scope. This Mark 3 plant development is currently underway with detailed assessment of a commercial dryer offering.
The selection process for a suitable commercial dryer including a market scan, technical workshop shortlist and site visits to Europe, has led to a select tender for preferred commercially proven biosolids dryers from overseas markets. This process is now underway with expected procurement in early 2025. The Mark 3 outcome will include automated feed from the commercial dryer to the PYROCO reactor and integration of the thermal heat energy from the thermal oxidiser to the dryer. Subject to incoming biosolids calorific value of approximately 16 MJ/kg and biosolid with total solids above approximately 27%, we anticipate a thermally neutral process with the caloric value of the biosolids providing all the thermal heat energy to both dry biosolids to minimum 85% for feed to the PYROCO reactor and all energy for pyrolysis and post pyrolysis thermal oxidation. The Mark 3 plant which we program will be in operation in 2025/26 will determine the validity of this thermal energy neutral process expectation based on pilot data.
Discussion
What next?
The Mark 3 PYROCO plant with integrated front-end dryer is currently in development for continual operation in 2025/26 as a key step in the technology’s market readiness. Subject to successful operation including achievement of target capital and operating costs, the upscale plant is planned to be made available to other utilities via delivery consortia in late 2026.
The pathway for PYROCO includes the completion of Mark 3 plant in 2025/26 to achieve Technology Readiness Level 8 and the learnings and confidence to provide a commercial offer in 2026.
From a utility strategic planning perspective, the critical path issue for South East Water was biosolids seasonal data to understand the biosolids characteristics for feed to a thermal process, which includes range of moisture contents and calorific values. Potential contamination pathways for stones or clay also become a consideration for thermal treatment. Since these considerations were less relevant for stockpiling and land application, the relevant data was not historically collected. The other consideration regarding future thermal treatment process for biosolids is the nature of other parallel biosolids processes such as anaerobic digestion, combined heat and power, solar dryers, drying pans and stockpiles, and where the right fit might be for the future. The renewal or replacement of existing components in the near term should be reviewed in the context of the future biosolids process stream options.
Conclusion
Based on the Mark 1 and Mark 2 pilot plant performance it is anticipated the overall PYROCO target outcomes as follows are on track:
- 25-year plant life based largely on no moving parts in reactor and uniform temperatures and correct material selection. This is based on fluidised bed reactors in other industrial processes achieving similar life spans.
- Continual operation with three to six months between maintenance. Again, based on no moving parts in reactor and uniform temperature control. With particle size range managed within the dryer it is anticipated this is readily achievable and will be targeted in Mark 3 trials.
- High heat transfer coefficient for low external energy input and associated cost. The ideal of thermal heat energy neutrality will be based on biosolids calorific value and total solids content for a given process efficiency. The high efficiency of fluidised bed heat recovery compared to alternative technologies will result in lower energy augmentation and realistic thermal heat energy neutrality.
- Reduced capital and maintenance cost due to high heat transfer coefficient and high availability. This will be determined from the Mark 3 development and subsequent larger commercial scale development. Based on the simple tube structure, non-exotic materials and ease of access to components, relative cost competitiveness is anticipated.
- Biosolids derived biochar from the PYROCO reactor will benefit industry trials with maximised value due to multiple characteristics for beneficial use.
Thermal treatment of biosolids is a viable approach for cost effective PFAS destruction and the creation of a beneficial end product in biochar. With the lack of moving parts in the thermal zone, tube construction and fluidised bed heat recovery, PYROCO offers the potential for low relative energy consumption, capital and operating costs and long plant life. PYROCO fluidised bed heat recovery is one viable option that should be considered with availability estimated for 2026. To note: Biosolids data to inform thermal process design including seasonal moisture content and calorific value should be undertaken well ahead of considering any procurement process planning.
Acknowledgements
Prof Kalpit Shah, RMIT
The Authors
Eamon Casey
Technical Director at Iota Services
Eamon qualified with first class Honors in civil engineering from University College Dublin, has post graduate qualifications in environmental engineering and 29 years’ experience in water & wastewater. Eamon held the role of Design Manager for South East Water and is now Technical Director of Iota Services - the commercial arm of South East Water. Eamon is supporting the PYROCO biosolids to biochar initiative.
Aravind Surapaneni
Principal Scientist, Biosolids at South East Water
Aravind has an Agricultural Science background and a PhD in soil science, worked as Senior Research Scientist at the Department of Primary Industries and in the pharmaceutical industry (U.S.). He played a key role in establishing the Biosolids Training Centre and initiated the biosolids to biochar research and development that is now leading to the construction of PYROCO - Australia’s first fluidised bed pyrolysis plant.
References
Department of Climate Change, Energy, the Environment and Water, 2020. PFAS National Environmental Management Plan 2.0 (Version 2.0), www.dcceew.gov.au
Department of Climate Change, Energy, the Environment and Water, 2022. Consultation Draft PFAS National Environmental Management Plan Version 3.0 https://consult.dcceew.gov.au/nemp-pfas
Queensland Government, End of Waste Code, Biosolids (ENEW07359617) Queensland
www.des.qld.gov.au
Queensland Government.