Sustainable desalination showcasing the submerged UF membranes pre-treatment at the Adelaide Desalination Plant
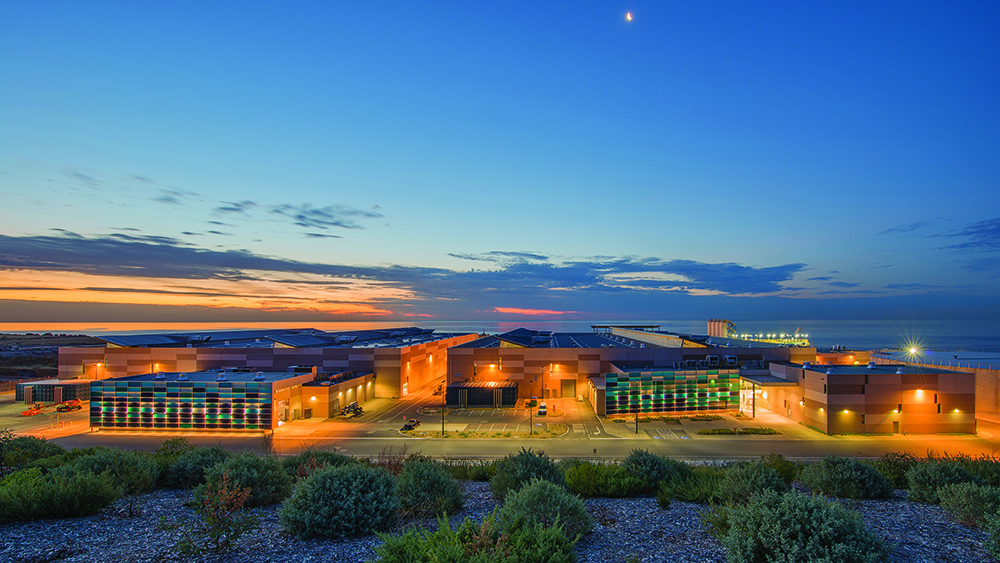
DOWNLOAD THE PAPER
Abstract
SA Water’s 300 ML/d Adelaide Desalination Plant (ADP) has been operating since 2011, and it is interesting to compare the design of its pre-treatment to recent SWRO projects that include Dissolved Air Flotation (DAF) within the process train. The ADP uses disc filter fine screens together with submerged membranes for the pre-treatment. This process/ pre-treatment train is not commonplace.
However, the ADP demonstrates/achieves strong advantages versus a two-stage treatment process such as Dissolved Air Flotation (DAF) plus pressurised membrane filtration.
This paper demonstrates that submerged membranes as pre-treatment are very relevant and are a sustainable pre-treatment solution for desalination plants built today. When compared to a process train that uses Dissolved Air Flotation (DAF) in the pre-treatment process, they can offer outstanding advantages in:
- installation costs
- simplicity of operation
- plant footprint
- energy use.
It should be noted that DAF can still be a great pre-treatment for projects when the seawater characteristics so require.
This paper also presents:
- key sustainable/environmental design and operating benefits of the current submerged membrane system for desalination
- a review of the original specification requirements for the ADP
- a comparison of aspects of the pre-treatment at the ADP to typical recent desalination projects in the region
- including plant footprint, chemical use and energy operating costs for similar projects
- reduced control complexity and reduced risk of water hammer when submerged membrane systems are directly coupled to the RO system
Since 2011, the supplier has significantly improved the features of submerged membranes by:
- reducing the plant footprint by 50%
- reducing aeration energy use by 36%
- reducing membrane capital and replacement costs by at least 35%
- increasing solids handling capability of the system
Introduction
The Millennium Drought in South Australia prompted critical water infrastructure investment and development of innovative, sustainable water management strategies. Along with the North South Interconnection System project, the Adelaide Desalination Plant (ADP) was built to provide a climate-independent source of drinking water for Adelaide. SA Water awarded the project to AdelaideAqua (consisting of ACCIONA, Abigroup – now ACCIONA and McConnell Dowell) for design and construct, and ACCIONA and TRILITY for operation and maintenance, in February 2009. The plant was built at Lonsdale, around 30 kilometres south-west of Adelaide (see Figure 1).
Figure 1: Adelaide Desalination Plant Location
The features and challenges of the local area are included in Table 1. (Lazaredes, 2011)
Some of the requirements for the ultrafiltration (UF) pre-treatment for this project were:
- achieve treated water quality with inlet silt density index (SDI) ≤ three at 95 percentile
- ability to treat feed water turbidity spikes up to 10 nephelometric turbidity unit (NTU) & organic feed water spikes up to three milligrams/litre (mg/L) total organic carbon (TOC) event
- ability to tolerate powdered activated carbon (PAC) in the feed water to treat a hydrocarbon event.
ACCIONA’s pre-treatment solution for the ADP included submerged membranes instead of a process train that included DAF.
Salient features of the pre-treatment process included:
- Submerged UF membranes with fine screens as this approach would:
- achieve the SDI requirement
- provide the lowest plant footprint
- achieve the highest feedwater recovery
- allow for a low energy system. - Ultrafiltration pre-treatment was directly coupled to the reverse osmosis (RO) system providing
- no filtered water storage tank
- submerged membrane filtrate pumps to double as the RO low pressure feed pumps. - Powdered activated carbon (PAC) added to the pre-treatment in the event of hydrocarbons
Results
The submerged pre-treatment at the ADP achieved:
- A feed water recovery of greater than 98.5 per cent
- Excellent treated water SDIs, with 98.1 per cent of results < three
- A successful control philosophy through direct coupling the filtrate pumps to the RO system, operating without difficulty and managing flows and pressures within tolerances as UF cells go in and out of backwash. Note also there is no water hammer risk to the UF, as the membranes are on the suction side of the RO low pressure feed pumps
Figure 2 below shows the TMP profile of the membranes operating at full design flow, even though the submerged membranes had been operating since 2011 (i.e. 9 year old membranes).
The energy use for pre-treatment at the ADP is extremely low. With submerged membranes, minimal energy is wasted, compared to pressurised membrane systems. So here the average TMP is only 35 kilopascals (kPa), and as the submerged membrane system is directly coupled to the RO system, there is further energy savings (i.e. no losses at any intermediate tank). Arguably the energy use on this
pre-treatment is lower energy than any conventional pre-treatment system that uses cartridge filters.
Notably the chemical use is also extremely low. Approximately once per month, a dual acid and hypochlorite maintenance wash is used for an hour each. There are no other clean-in-place (CIP)
or chemical backwashes etc. Also, no coagulation chemicals are used.
Figure 2: Hydraulic Performance of 9 year old Submerged Membranes @ Design Flow
Discussion
Adelaide Capital & Operating Costs Efficiency Benchmark vs Other Desalination Projects in Australia
Milind Kumar presented “Energy Recovery, from concept to Reality” to Engineers Australia in 2016 (Kumar, 2016). Relevant information from the presentation is contained in Table 2 below, which considers normalising both the capital cost, and operating cost of different large scale desalination projects around Australia.
As can be seen both the capital and operating cost efficiency of the Adelaide Desalination Plant compare favourably to the other projects listed.
Table 2: Australian Desalination Projects
Developments to the submerged membrane technology used at the ADP mean that a system built today will have an even lower capital and lower operating costs than what is presented above.
Submerged Membranes vs DAF Plus Pressure Membranes
Pressurised UF membranes are increasingly being used as the pre-treatment to seawater RO projects. However, many pressurised UF projects have pre-treatment such as:
- clarifier
- DAF
- media filtration.
A DAF project with a capacity of 300 ML/d can add in the order of 30 Million AUD to the total CAPEX of a desalination project. The table below compares parameters for a DAF & Pressurised membranes versus a Submerged Ultrafiltration only pre-treatment.
Table 3: Pre-treatment for Typical 136mL/d SWRO Project
Also, many recent seawater RO projects that use pressurised UF are not directly coupling the UF process to the RO. We understand this is because of factors such as:
- increased control complexity
- risk of water hammer (i.e. intermittently exceeding pressure rating of the membrane housing) or
- risk of damage to the pressurised membranes themselves from water hammer
Water hammer is a very destructive force that can exist in any pumping installation where the rate of flow changes abruptly for various reasons. This is particularly relevant for a pre-treatment for desalination as the process operates at high operating pressures, and there are frequent flow changes due to units starting and stopping to conduct backwashes. In fact, much time and expense have been spent repairing pipelines and pumps damaged by water hammer. The ADP demonstrates that direct coupling with submerged UF is a low risk, and in fact there is no water hammer to the UF process, as it’s on the suction (low pressure) side of the RO low pressure feed pump.
Algae Cell Breakage
Manheim & Jian found using probabilistic Materials Flow Analyses (pMFA) that Submerged membranes result in lower Algal Cell Breakage than Pressurised membranes (15-35% breakage in Submerged versus 75 to 100% breakage in Pressurised membranes).
They also found that coagulation plus MF/UF resulted in higher algal removal efficiencies for intracellular and dissolved toxins. (Manheim & Jiang, 2017)
The breakage of algae cells releases algae toxins and intracellular organic matter (IOM), into the feed stream, which could then pass through the pre-treatment process. This additional organic load could lead to increased biofouling on the downstream cartridge filters or RO membranes.
Table 4: Algae Cell Breakage using pMFA for different process trains
Conclusions
The pre-treatment at the ADP is a shining example of sustainable seawater desalination.
It achieved:
- Small footprint – lower land usage
- Low energy use – lower CO2 emissions
- No coagulant use – No sludge waste disposal & no land
fill requirements - Long membrane life – Lower disposal costs, lower
wastage
The decision not to install DAF pre-treatment has netted huge savings in capital and operating costs for the ADP, and produced a smaller plant footprint. The footprint reduction was also advantageous for the submerged membranes to achieve further savings in capital cost, as the land at Lonsdale presented civil challenges.
Submerged membranes reduce the risk of direct coupling the UF to the downstream RO process with no risk of water hammer. The advantages of direct coupling are well known, however this process has not been regularly chosen for recent large scale SWRO projects that are using MF/UF, potentially because of the perceived risks associated with water hammer.
Submerged membranes result in lower algal cell breakage than Pressurised membranes, and when combined with coagulation can achieve higher removals of Algal cells, and algal toxins than a DAF process. Submerged membranes are a suitable, cost-effective and competitive pre-treatment solution for many seawater projects.
The Authors
Huw Lazaredes
Huw is the Applications Development Manager and technical lead for the Memcor® brand of Pressurised, Submerged & MemPulse MBR product lines of DuPont Water Solutions in the Asia Pacific. He has over 27 years’ experience with MF/UF membranes, and during this time has been inventor and/or co-inventor of six patents.
Javier Artal
Javier is the Plant Manager at the Adelaide Desalination Plant. He joined ACCIONA in 2005 to work on seawater desalination projects. Javier has been involved in several international projects during different stages (bidding, contract negotiation, process design, handover and operation) from Spain to USA, Algeria and Australia.
Rimon Gergawy
Rimon is the Process Manager at the Adelaide Desalination Plant. He joined ACCIONA in 2010 to work at the Adelaide Desalination Plant as a commissioning Engineer. He then joined the operation team. Rimon has been involved in several interstate and international projects at various stages - mainly commissioning and operation.
References
Lazaredes, HA, (2011) Pre-treatment for Australia’s BIG 6 Desalination Plant, IDA World Congress
Kumar, M, (2016) Energy Recovery from Concept to Reality, Engineers Australia
Manheim D C, Jiang S C, (2017), Investigation of Algal Biotoxin Removal during SWRO Desalination through a Materials Flow Analysis, Water MDPI