Structural assessment of sewer pump stations using a novel photonics-based sensor system
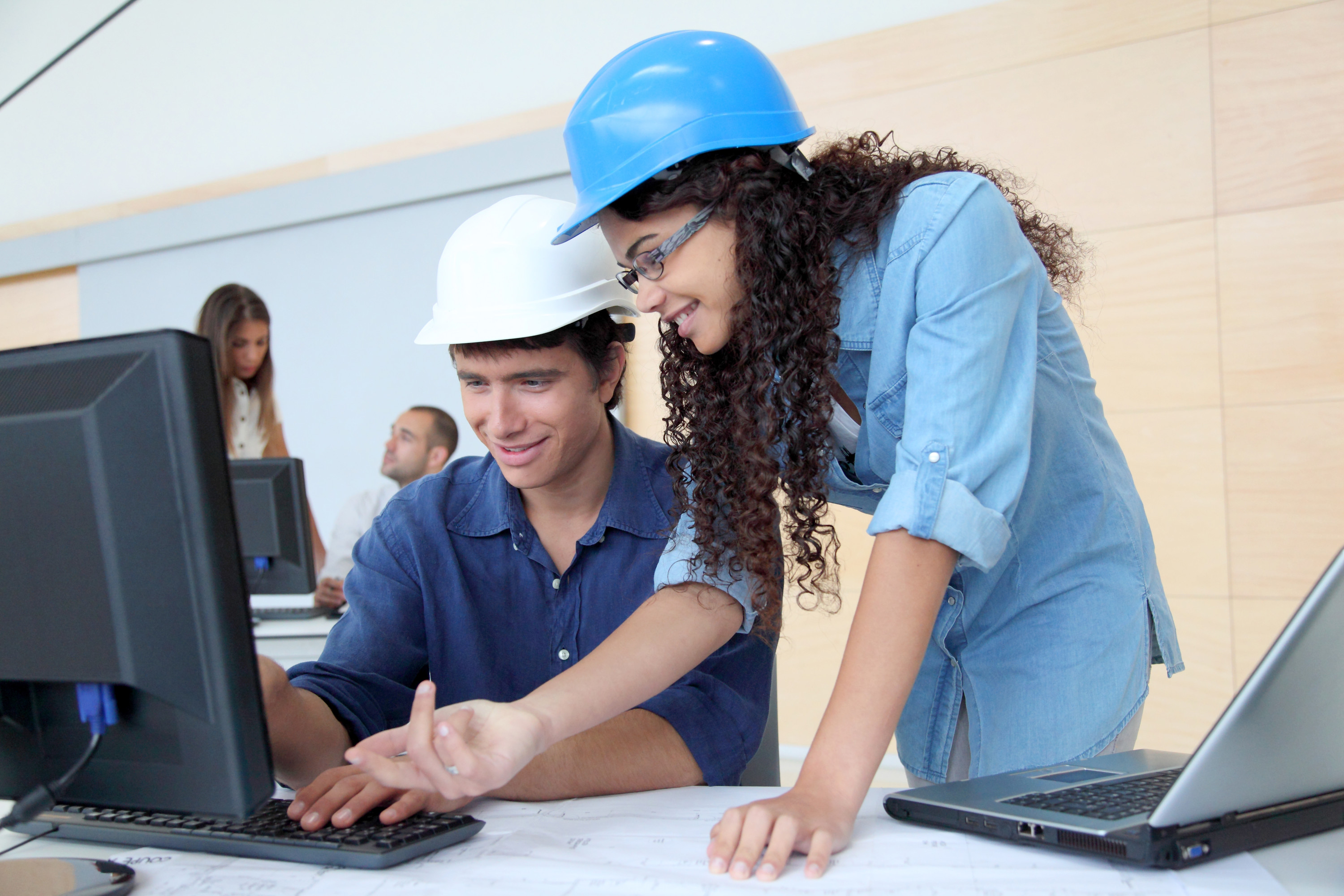
DOWNLOAD THE PAPER
Abstract
This paper reports the outcome of the research jointly developed and implemented by Sydney Water and City, University of London (City) to create innovative sensing solutions to long term monitoring of wastewater pump stations (PS) which form part of a network owned and operated by Sydney Water (SW). This has been achieved through recognising the potential of photonic devices for use in this environment and thus designing, fabricating and installing innovative optical fibre sensors, (achieving a strain resolution as low as ~1 microstrain), in two representative pump stations chosen by SW (and designated PS072 and PS001). This innovative sensor system has been complemented by conventional cover meter inspection for reinforcement identification. Being sensitive to the structural differences between the two sites chosen, the scientific rationale behind the sensor design, including the sensor positioning, the number of sensors installed, and the types of sensors required has been justified in detail in this paper. This contextualises the sensor data analysis and the key information extracted from the sensor systems designed and installed, thereby allowing better diagnosis of their respective structural operational conditions. Through this type of synergy of sensor data and structural integrity assessment, the key achievements of the work have been to create not just a continuous data-stream but allow accurate assessment of strain and vibration conditions of the structure in both time and position, through real time in situ monitoring and thus to warn of the potential for structural failure and collapse – the prime objective of the work.
Introduction and context
Sydney Water (SW) operates and maintains 690 wastewater pump stations across its network. Such sewage pumping stations are provided to lift the sewage from areas below and beyond the natural catchment boundaries to the higher-level sewer mains. They are also used to raise sewage from carriers to sewage treatment plants and often to avoid excessive depth of sewer lines in flat areas of land.
The context of the installation is that Sydney is a city which grew rapidly in the latter part of the 19th century and into the 20th, and thus pump stations were needed from that time to deal with the population growth. This study has included the oldest heritage-listed pump station in the SW network, designated PS001, which although constructed in 1899, remains in use in the network today. Since that time, several different types of pump station design have been constructed across the network, which include both dry well and wet well stations, wet well stations with grinder pumps, and wet weather storage type stations, for example.
The essential business driver of the work carried out has been to maximise the value derived from its significant annual investment in repair and replacement, and thus to maintain these pump stations as ‘fit for purpose’ is the important benefit, in spite of their age. The rationale for this project was that through the use of an innovative network of optical fibre-based sensors, pump stations could be monitored in real time and continuously and thus used effectively in the network. However, a further driver for the work was the problematic collapse of pump station PS103 (located in Northmead, Sydney), in 2018 (a pump station of a similar design to PS072) which caused a major environmental spillage and resulted in a fine to SW by the New South Wales Environment Protection Authority [1].
The problem is that current, conventional methods of structural monitoring are not well suited to the problem of achieving the real time, continuous monitoring that can give confidence in the structural integrity of concrete structures such as Pump Stations and thus their use in the network. While finite element analysis (FEA) of such structures is widely used in an attempt to assess their structural integrity, the Sleipner failure [2] (reported some 30 years ago) was attributed to inadequacies in the FEA carried out where an over reliance on modelling data was blamed for the failure to identify zones of high stress, compounded by an over dependance on computerised reinforcement detailing. Together, these weaknesses led to a catastrophic shear failure which the modelling did not predict. In the ensuing investigations, doubts were cast on the reliability of the design codes used when assessing the stress combination of axial load and shear. A reassessment of the recommendations in the then current UK code (BS8110) was undertaken by reanalysing data from tests on beam-column connections, which exhibited a similar stress combination. As a consequence of this failure, enhanced design equations were formulated and the UK code revised accordingly. In light of this SW were naturally reticent to rely on FEA for the pump stations in their network.
Conventional electrical strain gauges have traditionally been used for real time monitoring of structures, making strain measurement in situations such as those under study. However, care needs to be taken when using them in ‘real world’ situations as problems can arise due to important issues such as:
- Long-term stability of the calibration of the strain gauges and
- Their durability in the inevitably damp environment of such Pump Stations as ingress of moisture will cause failure of these electrical sensors. Expanding on this, a damp/humid environment is particularly problematic as it means that long term stability is very difficult to achieve. It can cause corrosion of the unprotected wires resulting in currents flowing between the wires and the substrate to which the strain gauge is attached and create a conductive path with much less electrical resistance than the intended path. For these reasons, strain gauges and their wiring must be fully protected – if that is possible when exposed to humid or damp environments. Further such sensors are not intrinsically safe in hazardous environments or where explosive or corrosive gases can build up.
A damaged strain gauge (a problem which often cannot be detected visually) will give readings which either fluctuate wildly, or are inconsistent with other gauges in the locality, or go straight to open circuit. Such gauges are irreparable, the only solution being to replace them. In addition to possible problems of access in a field environment, there may be difficulties ‘zeroing’ the calibration of the gauges to the same baseline as the others in the installation.
In addressing the problems of monitoring PS072 and PS001, it was recognised that a new approach was needed and the available technology for such applications has moved on considerably and other solutions which show the same sensitivity and avoid some of the above problems (through the use of all-optical fibre strain sensors) are now available. These were assessed by the team involved in the work as offering a potential new solution to the real-time, high-resolution monitoring needed to address the requirements of the enforceable undertaking served on Sydney Water as a result of the Northmead incident.
Concrete and its use in the construction of the pump
Concrete is strong in compression but weak in tension. The pump stations under assessment in this work were designed with concrete walls, which experience compressive strains which, normally, will be within the acceptable design limits. However, should tensile strains occur then cracks will likely form at around 100μE, and their propagation could lead to brittle failure.
Another consideration in this case is shrinkage, which will induce tension in the concrete although, in view of the age of the pump stations (PS072 constructed in 1927 and PS001 in 1899) this may likely have been largely dissipated by creep. It is also possible that shrinkage strains may not be immediately apparent since they may merely be reducing the compressive strains caused by self-weight loading.
Investigation of tensile strains
Added to the above is an ongoing concern regarding the presence/absence of reinforcement in many of the walls of the pump stations (an issue which was not evident from the plans available from Sydney Water’s records and indeed may not have been recorded correctly, given the age of the structures). It is, however, well known that reinforcement detailing in early concrete structures could be quite different from what is practised today. There is always the risk that tension cracks may link up with shrinkage cracks or voids in the concrete which would exacerbate the potential for brittle failure which would be a particular worry if the walls are unreinforced.
For the above reasons it was seen as important by Sydney Water that any signs of tensile strains being developed in the concrete should be carefully investigated. Even slight incursions into the tensile range during normal pumping operations would be a matter of concern and require careful assessment of their effect on both the short-term and long-term integrity of the structure. Continuous long-term monitoring of pump station performance will be particularly valuable when making these assessments and this is a key feature of the capabilities of the monitoring systems developed, and this is discussed in this paper. The use of fibre Bragg gratings (FBGs), as the basis of the what is often seen as the optical fibre ‘equivalent’ to regular electrical strain gauges (but which in many instances offer superior performance, e.g. in corrosive or damp atmospheres), represent an ideal approach, due to their long-term stability, resistance to humidity and ability to measure both strain and vibration. In order to allow the widest interpretation of the data generated, all pump station walls were treated as being unreinforced (unless the original reinforcement layout drawings were available and show otherwise).
Methodology of the investigation
Pump station PS072 and sensor layout planned and implemented
Figure 1 (left) shows the annulus structure of PS072 which is strengthened by 9 radially positioned buttresses. The two well types more commonly being referred to as wet (where wastewater is stored) and dry wells (where machinery is positioned) respectively. Two aspects for particular attention in this work were the strains on the wet well wall caused by changes in water level, and vibrations in the pipes and walls caused by the pumps starting and stopping. As the outlet riser was hard against a buttress as shown in Figure 1 (left), this indicated that the vibration from the outlet riser was largely absorbed by the buttress. To verify this, an appropriate sensor layout was devised and this is illustrated in Figure 1 (right).
As shown in Figure 1 (right), in total 12 strain rosettes (12S) and 8 temperature sensors (8T) were installed at 3 locations with ‘A’ series sensors 6S (SA1-SA6) and 6T (TA1-TA6) being distributed vertically along the wall in a location where scaffolding could be easily erected; ‘B’ series 4S (SB1-SB4) + 1T (TB1) around the outlet riser and ‘C’ series 2S (SC1-SC2) + 1T (TC1, not shown) directly on the riser. Added to the above were two electronic sensors, measuring respectively the water level in both wells and the pressure in the outlet risers, for comparison purposes. As marked in Figure 1 (right), the ‘A’ series sensors are located at least 2000 mm from the edge of the buttress.
Figure 1: (left) Simplified drawing of PS072 to show the essential features of the pump station – top view; (right) Mapping of sensors on the wall and pipes – side view.
Pump station PS001 and sensor layout
PS001 is of exceptional historical significance. It was designed in the Federation Free Style [3] – an architectural style allowing domestic styles to be applied to larger buildings at turn of the 19th century. The substructure walls were constructed in concrete, but the original drawings do not indicate if they were reinforced. In addition, even if reinforcement is present, reinforcement detailing at the time of construction was in its infancy and would not conform to modern practice. Thus, the only safe approach (and that taken in this work) was to assume that the walls were unreinforced.
Concrete mix design was also in its infancy at the time of construction and analyses of cores taken from the walls showed that the mix design would not meet modern standards. However, PS001 was constructed over thirty years before the first design code was published and it is impressive that PS001 is still a working pump station, 120+ years after its construction.
The substructure consists of two sewage wells adjacent to a machinery chamber, as shown in Figure 2. Wastewater collects in the wet wells and, upon reaching a prescribed level, pumps in the dry well then pump it up through an outlet riser to ground level and into the SW distribution system. There is a non-return valve in the outlet riser which is situated in a valve chamber adjacent to the dry well, just below ground level.
The suction inlet pipes through the bottom of the wall dividing the wet and dry wells are of 600 mm in diameter. Each pipe feeds into a pump with outlets from the pumps combining into a single outlet riser. Two aspects for particular attention for the structural integrity of the station were the strains on the well wall dividing the wet and dry well compartments, caused by changes in water level, and vibrations in the pipes and walls caused by the pumps starting and stopping. Closure of the non-return valve in the valve chamber might also create vibrations due to ‘water hammer’. Consequently, the following layout for the sensors to monitor the station (grouped in clusters) was devised and is illustrated in Figure 2:
Cluster 1: Two strain rosettes on the suction inlet of well 1 (90° apart) and another two around the opening in the wet well wall (on the dry well face).
Cluster 2: Same layout as Cluster 1 but installed on suction inlet and wall of wet well 2.
Cluster 3: Two strain rosettes on each outlet riser (90° apart).
Cluster 4: Four strain rosettes on the wall around the opening where the combined outlet riser penetrates the wall into the valve chamber.
Cluster 5: Two strain rosettes (90° apart) on the pipes either side of the non-return valve.
Cluster 6: Six strain rosettes mapped along a vertical column up the centre line of wet well 1 (on the dry well face).
Cluster 7: Same layout as Cluster 6 but installed on wall of wet well 2.
Each sensor cluster has an additional dedicated temperature sensor (not shown in Figure 2) to allow compensate for the temperature effects on the strain sensors to be made in the usual way (as discussed in Section 3.3).
Figure 2: Substructure of the pump station and sensor mapping. The sensors are grouped into clusters which are distributed across the key points of interest of the Pump Station, i.e., the suction inlets (1,2), the outlet risers (3), the wall around the outlet riser opening (4), the external valve chamber (5), and the well walls (6,7).
Optical fibre sensors and the sensor system installed
Figure 3 (left) illustrates a conventional electrical strain gauge-based rosette (and which is routinely used to capture strain changes along 3 different orientations). The optical strain gauge design uses the same rosette approach, with the electrical sensor element replaced by an optical element, based around FBGs and as shown in Figure 3 (right). In this way structural engineers can have confidence in the data generated by the sensor system.
Figure 3: (left) Schematic of an (electrical) strain gauge rosette; (right) photograph of an optical strain rosette and a temperature sensor designed for this work (with schematic overlay of the sensor rosette structure).
FBGs are used as the key elements of the sensor system, allowing simultaneous temperature and strain measurement. Fuller details of the operation of FBGs is given elsewhere (e.g. [4]) but in summary a FBG is a structure with the fibre core being periodically modulated and reflects the light at a wavelength, termed the Bragg wavelength (λB), that satisfies the Bragg condition, given in equation (1).
where ͷeff is the effective refractive index of the fibre core and Λ is the grating period, where both are affected by strain and/or temperature variations, a feature that is reflected in the sensor design.
The underpinning sensing mechanism of a FBG is that its Bragg wavelength (λB) shift is determined by the change in surrounding temperature and/or strain applied as described in equation (2) [5].
where Pe is the photoelastic constant of the fibre, ε is the strain induced on the fibre, α is the fibre thermal expansion coefficient and ζ is the fibre thermal-optic coefficient.
Equation 2 also indicates clearly the cross-sensitivity of a FBG to strain and to temperature, therefore when a measurement of strain alone is required using a FBG-based device, correction for any temperature effect is required, with compensation achieved through optimising the sensor design and sensor packaging and including a separate (FBG-based) temperature sensor element. This is the reason why the strain rosettes installed in pump stations are paired with temperature sensors, as shown in Figure 3 (right), to allow for full thermal compensation as the temperature within the pump station will vary.
Optical sensor interrogation and calibration
One of the key features that FBG-based optical sensors have demonstrated is their capabilities to be multiplexed along a single narrow optical fibre. Figure 4 shows a typical FBG-based sensor layout based on wavelength-division-multiplexing (WDM) [6] with each grating being encoded at a specific wavelength (and thus allowing it to be identified along the optical network by that wavelength). This characteristic is of particular importance for monitoring large-scale and/or critical structures, like pump stations, which require densely distributed sensors, for simultaneous multi-point measurement. In this project, for convenience the connections between the sensors (e.g. 44 FBGs in PS072 or 127 FBGs in PS001) were grouped into four channels which fed into the data logging hardware (Micron Optics, type si155, Hyperion).
Figure 4: Schematic layout of a quasi-distributed FBG sensor system used in this work
Surface preparation prior to sensor installation
Before the sensors were installed in the various locations on the walls and pipes, extensive surface preparation was required and undertaken (this important process spanning several days). Figure 5 illustrates three examples of surface conditions across SP001, i.e., painted walls and pipes as well as tiles on the concrete walls with an additional layer of paint, all of which potentially were inhibiting reliable strain transfer from the walls/pipes to the sensor patches prior to their removal.
Figure 5: Surface preparation for optimum adhesion enabling reliable strain transfer from the
walls/pipes to the sensor patches. Three different locations are shown (from left to right):
outlet riser; painted concrete and tiles on a concrete wall.
Once the surfaces were prepared and cleaned (with IPA and lint-free wipes), the sensors were bonded to the pipes and walls with concrete-based epoxy resin commonly used to repair cracks in concrete walls (and therefore considered appropriate for this application). The sensor patches were then held in place with aluminium foil tape for a period of three days to allow sufficient time for the epoxy resin to fully set and allow for good strain transfer. Figure 6 shows three exemplary photographs of sensors installed in SP001.
Figure 6: Photographs showing examples of sensors installed at various locations throughout PS001 (from left to right): outlet riser; dry well wall and valve chamber
To complete the installation process, the sensors were connected in series across four parallel instrument channels.
Figure 7 shows a typical signal captured from one SP001 channel with 34 FBGs (ten strain rosettes (i.e. 30 strain-measuring FBGs with four temperature sensors), with each peak showing the signal received from any one of the FBGs used. The individual peaks could then be ‘tracked’ through software and the wavelength shift monitored then converted into strain/temperature data, using Equation 2. Tracking the peak wavelength (which was seen to be highly stable over time) as opposed to the peak amplitude (which can be affected by a number of features, such as degradation of the optical sources used) offers excellent long-term stability of the monitoring system (as signal amplitude data are important).
Figure 7: Signals captured from one channel showing the response of the 34 FBG-based sensors used across the wavelength range from 1490 nm to 1590 nm (34 peaks)
The selection of adequate sensing locations in terms of both accessibility and usefulness for the station’s condition assessment took several months to complete. The key challenges faced in making those choices are summarised below:
- Structural information: Extensive research into original structural drawings and multiple site visits were necessary. Some aspects remained inconclusive, e.g. the presence of reinforcement in the concrete walls as well as the composition of the actual concrete used to build the two stations at the turn of the 19th century and in the early 20th century due to the lack of standards.
- Extensive surface preparation: The paint in many locations had started to peel off so it had to be removed. Due to the age of the paint, it had to be tested for potential lead content. In addition, in some areas of interest tiles were uncovered under the paint and had to be removed. Grease, rust, and/or paint had to be removed from the pipe surfaces.
- Dust: The required level of surface preparation generated considerable amounts of dust in the confined space of the station’s machinery chamber so personnel had to take appropriate precautionary measures (personal protective equipment etc.).
- Fibre routing: To avoid the fibres being damaged by other work going on in the pump station, safe routes from the sensing instrument (sat in a locked cabinet above ground) to the sensing locations had to be established. This was also addressed through multiple site visits.
- Remote access: It was essential for the monitoring system to be accessible remotely as pump stations are generally not manned so 5G connectivity was a key requirement.
Results of the investigation carried out
PS072 unusual operation: pumps off
An unusual operation had been arranged (on 29 November 2021) by SW to test the performance of the sensor system. Before 7am that day, both pumps operated in alternating manner and after 7am both pumps were switched off, allowing for the increase of the water level in both wells. When the well levels reached 70%, both pumps were switched on again which is signaled by the increase of the pump pressure and the decrease of water level in both wells monitored by electrical sensors installed.
Figure 8 shows the signals captured by B and C series sensors when the pump is off, indicating the liquid oscillation inside the pipe as reflected clearly in SC2 sensor. The vibration is transferred to the wall, as reflected in SB1-4 sensors, showing maximum strain transfer into SB4 and minimum into SB2. However, SA sensors did not pick up any oscillation because A series sensors are located about 200 mm from the edge of the buttress as shown in Figure 1. This adjacent location makes it difficult to capture any dynamic signals.
Figure 8: Signals illustrating liquid oscillation inside pipe captured by B and C series sensors in PS072 when the pump is off for SB1 – 4 and SC2 (positioned as seen on inset diagram)
PS072 Long term operation
Figure 9 shows sensor data from SA1-6, collected remotely in London over a period of nearly one year (January to October). As expected, high precipitation, e.g. heavy rain fall, results in higher wet well level which subsequently causes compressive strain in the well wall and the signal of which is picked up by the SA sensors installed on the dry well side. It is noticeable that after each precipitation event, the strain in the well wall slowly recovers. There is no sign of tensile strain experienced by the pump station wall during the monitoring period, signalling its healthy operation conditions.
Figure 9: Sensor data collected from pump station PS072 over a period of nearly one year (January – October)
A cover meter inspection was undertaken to try to establish what reinforcement, if any, was present in the dry well wall. (A cover meter is a portable, handheld, battery-operated device which uses the electromagnetic principle to determine the location of reinforcement in concrete). The inspection identified the presence of a mat of reinforcement (i.e. horizontal and vertical bars) on the near face of the wall. However, it was concluded that this reinforcement was unlikely to influence the serviceability (working load) performance of the structure although it would likely enhance behaviour under ultimate (e.g. collapse) conditions.
Monitoring vibration in PS001
A key monitoring aspect – within the scope of this report – was vibration present in the outlet risers (sensor Cluster 3) and how this is transferred into the wall where the combined outlet riser penetrates it (sensor Cluster 4). Figure 10 highlights the sensors of interest.
Figure 10: (left) Schematic highlighting the sensors installed for vibration monitoring, i.e., sensor Clusters 3 and 4 on the outlet risers and around the opening where the outlet riser penetrates the wall, respectively; (right) Photos of sensors SD1 and SE (left) which were installed in PS001.
The sensor data captured are plotted in Figure 11 where the top diagram shows the signals obtained from outlet risers and the bottom diagram those from the wall around the opening. There was no controlled starting or stopping of the pumps in PS001, meaning that both operations propagated sudden impulses into the pipework, as indicated by the spikes in the sensor responses shown in Figure 11, in this instance caused by a pump stop. Subsequent to this stop, water continued to oscillate in the pipework, slowly decaying until the next pump start-up. The oscillation frequency of approximately 0.15Hz was not related to that of the pumps which operated at about 400rpm, i.e., 6.7Hz. Oscillations in the pipes were transmitted into the wall where this was penetrated by the outlet riser, as shown in Figure 11. Interestingly, above the outlet riser the wall was in tension whilst below the pipe it was in compression. The observed strain magnitudes of <15μE, however, are no cause for concern (from a structural point of view) but it will be interesting to monitor these vibration ‘signatures’ over time.
Figure 11: Dynamic signals captured by the vibration sensors illustrating the propagation of sudden impulses into the pipework, as indicated by the spikes in the sensor responses shown (and caused by a pump stop). The graphs show that water then continued to oscillate in the pipework, slowly decaying until the next pump start-up.
Discussion and analysis
The major capability of the optical fibre sensor-based approach shown by this work has been the ability to capture the weak damping signal released from the liquid oscillation after the pump is off in both pump stations, as shown in Figures 8 and 11, and this confirms the high sensitivity of the sensors deployed in this environment. The work done has been pioneering, designed to overcome the lack of suitable commercial sensors with an appropriate sensitivity for this purpose. The sensor system here was designed to meet the requirements set by Sydney Water and to allow monitoring systems to be installed in these historic structures, transmitting data on performance and giving warning of potential structural risks.
However, the data collected show that when the pump in PS072 is on, there is no signals at 20-40Hz (from the pumps) being captured by sensors. This is likely because the vibrational signal from the pump has been absorbed by the buttress where the outlet riser is positioned hard against as illustrated in Figure 1 (left).
The key lessons for the installation of sensors at PS001 from the years’ data taken from PS072 show that in spite of some sensors being near to a buttress they are still able to measure quite appreciable levels of strain in an area which is very stiff. This is an important finding for future installations that may help minimise the number of sensors that need to be installed in any future pump station monitoring work and still to get the maximum information from the long-term sensing undertaken.
The sophisticated and all-optical sensor layout designed, installed, and used in PS001 has permitted some interesting comparisons to be made with regards to how vibrations from the pump operations are transmitted around the pump station. As discussed above, vibrations in the outlet risers are transmitted into the walls but, by contrast there were no signs of vibrations in either the suction inlet pipes or in the wet wall where this was penetrated by these pipes. This suggests that both wall thickness (i.e. wall stiffness) and geometry of the pipe layout (more complex in the case of the suction inlets) are important parameters in determining how the system will behave and there will likely be considerable variations in these parameters within any one pump station.
Conclusions and next steps
The work carried out has shown the advantage of the innovative approach taken, integrating both sensing science and engineering and structural engineering, to fully investigate and thus understand the concrete structure. The research project has clearly indicated the need to fully engage with and have access to the end user’s know how and detailed knowledge of historical structure such as were investigated, as well as the operation of the pumping stations. This has enabled the creation of new solutions to an important set of monitoring problems. The optical fibre sensors have been successfully installed, exemplified in that they provided reliable data for both static (increased rainfall) and dynamic (water hammer) events.
The data collected from PS072 and analysed have shown that the working load and impact from the outlet riser and the water level change in pump station PS072 is minimal. This is because of the strengthening of the wall with 9 buttresses and position of the outlet riser hard against a buttress. The near-face reinforcement helps with extreme situation. Similarly, the effect of water hammer on the pipes and walls of PS001 was shown not be a cause for concern.
Despite the two pump stations monitored are of different age and different structural layout, the significant uplift by instrumenting them with distributed optical sensors, coupled with digital enablement through connected data feed, data analysis and analytics, has provided new trends and meaningful insights which give confidence in the longer-term use of the pump stations – that they are ‘fit for purpose’. The results have demonstrated the flexibility of the monitoring system in the way that it could be adapted to suit the two different layouts studied and to provide insights into the different ways which the pumping action impacts on the structure and the pipework. This should be particularly valuable in the future since no two pump stations are the same (even if their structural layout may appear, at first sight, to be similar).
This approach used was further seen as a successful way to fill the gap given that no commercially available sensors can provide (i) the ability to monitor several sensors at a long distance between each other and (ii) reliable long-term monitoring that will not only provide data on diurnal-nocturnal pumping station activity but also seasonal changes.
The approach taken provides the basis for a ‘Digital Twin’ of the two pump stations studied – and thus provides the basis for setting up a Digital Twin of future pump stations that are required to be monitored. This can be based on such drawing and records that are available on file by the asset owner (in this case Sydney Water). The aim is to give confidence in the ability to use these assets for many more years to come and to avoid the costs, reputational damage and environmental impact of pump station failure.
Given the success of this study, the next steps planned are:
- To build on the breadth of experience gained of this monitoring work on the current two pump stations under monitoring to set a ‘baseline’ for the monitoring and using traffic lights to alert of potential damaging events and
- To extend the current software and monitoring system (which currently allows monitoring of the outputs of the sensors both in Sydney and in London).
Acknowledgements
The authors would like to thank Sydney Water for the financial support for this pilot collaborative research undertaken jointly by City, University of London and Sydney Water. The support of the Royal Academy of Engineering through several schemes is also acknowledged.
The Authors
Matthias Fabian is a Postdoctoral Research Associate at City, University of London where he specializes in the development and implementation of fibre-optic sensors for a variety of industry-focused applications in the civil and structural engineering sector, as well as the railway, marine, and power electronics industries.
Richard Scott is a chartered structural engineer. After graduation he worked for ten years in industry, designing a wide range of building types. Then, at Durham University, he conducted research into the behaviour of reinforced concrete structures and now collaborates with colleagues at City, University of London, on a range of industry related projects.
Sankhyabrata Bandyopadhyay is a Postdoctoral Research Fellow at City, University of London. His research interests include the design and fabrication of optical fibre sensors for industrial applications and biomedical imaging. He is also involved in the development of machine learning-assisted automated sensing systems, quantum sensors, and nano-photonics.
Tong Sun received degrees from Harbin Institute of Technology, China, and the Ph.D. degree in applied physics from City University, London, U.K., in 1999. She was an Assistant Professor with Nanyang Technological University, Singapore, before she rejoined City as Professor, where her research focuses on developing a range of optical fibre sensors.
Kenneth Grattan received his Bachelors and Doctoral degrees in Physics from Queen’s University Belfast, and following a Research Fellowship at Imperial College London, joined City, University of London where he is Professor. His research interests include the measurement of a range of physical and chemical parameters using optical and optical fibre-based methods.
Heriberto Bustamante did his PhD at Imperial College (London). He is Principal Scientist Treatment in Sydney Water. Heri has more than 30 years of experience in industrial research. Heri pioneered the introduction of photonic sensors in Sydney Water by starting collaboration with City, University of London to improve the management sewers and pumping stations.
Michael Thurner has a degree in Civil & Structural Engineering (Technical University Vienna). After working in R&D in Water Corporation (WA), he joined Sydney Water in 2018. He is developing an effective sewerage pumping stations plan focussing on structural health monitoring by using photonic sensors so that Sydney Water can more safely “sweat” its ageing assets.
Enrico Coiro is a former Sydney Water Operations Engineering Services Lead for wastewater networks.
Raymond Llave is an experienced IT Executive with successes in the development and implementation of strategies, architectures and new technologies including Digital Water Strategy and Smart Water Architecture. A thought leader on Digital Strategies and Transformations, Smart Cities, Digital Futures and Emerging Smart Technologies.
Mason Win leads a team delivering projects and maintenance services in the instrumentation, automation and control industry for Sydney Water.
Jeremy Hearfield is a Hydrometric Team Leader who has worked at Sydney Water since 2009. With 14 years of hydrography experience, a core focus of Jeremy’s work has been on sensor installation, flow monitoring, data collection, data verification and reporting. He is currently leading Sydney Water’s large scale field rollout of Internet of Things devices.