Membrane Loader for the Reverse Osmosis (RO) Membrane Replacement at Seqwater’s Gold Coast Desalination Plant
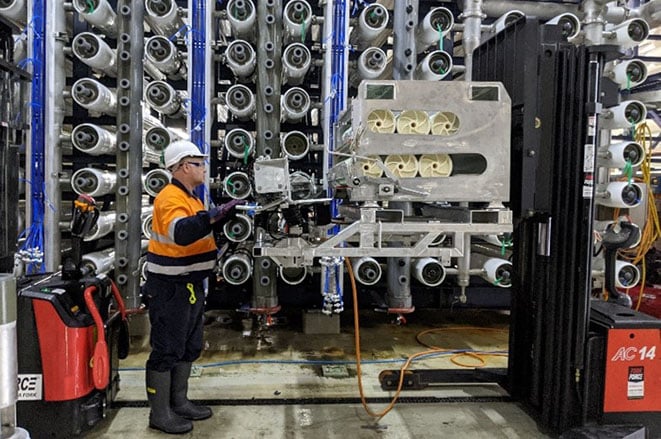
DOWNLOAD THE PAPER
Abstract
Although the Reverse Osmosis (RO) membranes at Gold Coast Desalination Plant (GCDP) aged considerably well since plant commissioning and were still suitable to produce drinking water, deterioration of the performance had been observed, particularly Salt Passage. The global RO market also had supply outstripped by demand which consequently extended delivery times. Based on the volatile market condition and the revised operational forecast due to drought response operations and baseline network requirements at the time, GCD Alliance expedited the replacement program and initiated a full replacement of the RO membranes at GCDP.
In 2021, Seqwater’s Gold Coast Desalination Plant replaced all 16,848 of its aged First Pass RO membranes (SWRO) and Second Pass RO membranes (BWRO) in the space of 12 weeks. The delivery of this project presented several challenges specific to the site which were overcome by the teams through collaboration and innovation that could shift the industry’s ways of working.
Key Points
- Unlike a routine maintenance/task, a full site replacement required careful planning and consideration to guarantee a successful outcome.
- The membrane loader resulted in 85% manual handling risk in a process that has occurred on a global scale for decades.
- The project was completed with no injuries, on time, HACCP requirements met and on budget.
- The robust workflow is key, arguably more important than the membrane loader. In reality, the workflow and processes around the membrane loader dictated the overall loading efficiency.
- The teams involved, with the right attitude, were able to turn challenges into opportunities and successfully completed the project with an innovation piece.
- There should be no compromise of quality and with proper planning and scheduling, the method and equipment should be considered for future jobs.
Introduction
Background
RO membranes are traditionally loaded manually and at 15-17 kg each (dry weight) and eight membranes per vessel, a membrane change out of this magnitude comes with safety risks, mainly manual handling strains from repetition. A previous manual handling injury saw Seqwater prompt Veolia to address the issues with manual loading which saw the project team focus heavily on safety. Timeliness is also key as the plant was operating as a part of the Seqwater’s drought response so would need to work strictly under the allocated shutdown schedule. Veolia was driven to look for solutions to overcome said challenges to keep people safe and to get the job on time and on budget.
Method
Research and Site Investigation
Veolia conducted the initial research and began the concept ideation for a device to help with the loading/pushing of the RO membranes. The goal of the loading device is to reduce manual handling whilst being safe to operate and minimise rework (quality). The membrane loader must also have a failsafe to avoid damage to equipment e.g. pressure vessels, the RO membranes and their components.
In the earlier stages, Veolia kicked off the site investigation in 2020 to acquire data e.g. force tests showing force required and alignment tolerances on a First Pass SWRO train.
The force test results are shown on Table 1 below.
Table 1: Raw Data
Collaboration for Prototype Build
During the tender for installation work the following year, Safety and Timeliness weighed heavily for contract award.
Neumann Contractors presented a concept idea as part of the tender submission which was inspired by a recent work at another Seqwater water treatment plant. 1,500 RO membranes were installed manually and the findings by the team include:
- High level of manual handling on a large number of RO membranes, presenting injury risks through strain and repetition;
- Change out process involves tedious steps and is inefficient; and
- Unloading of RO membranes creates a wet working environment.
The two parties quickly identified the opportunity to bring an idea to life through this project. Veolia had done a concept design and acquired data based on site investigations, and Neumann Contractors had similar interest with the capacity to design and fabricate. This contributed to the award of the contract, and with a slightly extended scope, began the collaboration between Veolia and Neumann Contractors for the RO membrane replacement at GCDP. At this point, the plan was to fabricate and trial the device in the first phase of the project (replacement of the BWRO membranes), whilst having a contingency plan should the device not work.
Veolia acted as a consultant providing data and design inputs, whilst Neumann Contractors designed and manufactured the prototypes. The membrane loader adopts a pneumatic system with a cartridge able to hold eight RO membranes at a time. After one membrane is pushed, an operator can allow the next membrane to roll out of the cartridge and onto the membrane loader, ready to be pushed into the vessel.
Prototype testing took place at Neumann Contractor’s workshop with GCDP pressure vessels and RO membranes provided by Veolia for design and testing purposes (refer to Figure 1). These trials proved critical as the attendance of and feedback from Veolia’s subject matter experts (30+ years of experience) were adopted to the final design.
Figure 1: RO Membrane Loader demonstration at Neumann Contractor’s workshop
Challenges
The team had two main challenges – Designing and manufacturing a membrane loader that is safe-to-operate and suitable for the project prior to the planned installation start date, and to develop a workflow along with the required equipment and accessories to meet project schedule.
During the design process, the challenges include but are not limited to:
- Sourcing a pneumatic ram suitable for the required pushing force and pushing length;
- Designing a clamping system that is fixed onto the pressure vessel and not the structural steel frame to help distribute the pushing load to the neck of the pressure vessel and avoid displacing the pressure vessels and avoid causing damage;
- Incorporating alignment capabilities to avoid damage to RO membranes and interconnectors;
- Efficient and delicate handling of RO membranes from preparation to loading into pressure vessels; and
- Time and resource constraints to deliver a working prototype and confirm feasibility.
Combining Neumann Contractors’ equipment design experience and capability and Veolia’s subject matter experts, the team was able to cooperate and overcome the challenges.
The final design of the membrane loader system, shown in Figure 2, features the following:
- Sourcing the correct pneumatic linear actuator;
- A clamping system that distributes the push force on neck of the vessel and not on the structural steel frame;
- A self-aligning mechanism for alignment of the RO membranes prior to and during loading into the pressure vessel; and
- RO membrane cartridge that holds eight RO membranes (one pressure vessel worth), mountable on the RO membrane loader to feed the RO membranes into the pushing unit.
Figure 2: Diagram of the RO Membrane Loader and the RO Membrane Cartridge
Along with other equipment and accessories, Neumann Contractors also manufactured a purpose-built table to unpack the RO membranes, scan serial numbers, lubricate the brine seals and fit the interconnectors before loading into the membrane cartridges. This is part of the developed workflow which also considered efficiency and safety for the process steps prior to loading.
Workflow Summary
Preparation and Cleaning
Once all the permeate pipework and end caps have been removed the used RO membranes are ready to be removed, and the new ones installed. The clamps are fitted on pressure vessels on the loading side and RO membrane preparation activities can commence. The end caps are cleaned before reinstallation.
The RO membrane boxes on pallets are raised and placed next to the purpose-built Sorting/Packing table. Eight RO membranes are slid onto the table in series and the serial number barcodes on the boxes are scanned and recorded. With safety slitters, the tape on the boxes are cut on the long side and the RO membranes are rolled out to be removed from the vacuum bags. The cardboard boxes are saved for recycling and cut-out plastic bags removed for recycling.
The RO membranes are fitted with the interconnectors (seven of the eight) and the brine seals are then lubricated with Glycerine and then rolled into the membrane cartridge. A purpose-built ‘cleaning pig’ is soaked in water and Glycerine and placed into the membrane cartridge, ready to be transported to the RO membrane loader for loading.
Loading
The membrane loader is attached to the clamp system fitted on the pressure vessel with industrial carabiners and aligned. The prepared RO membrane cartridge is mounted on the membrane loader, ready for loading.
The operator first places the cleaning pig against the first used RO membrane visible from the loading side. This pig is pushed in to clean (water) and lubricate (glycerine) the pressure vessel along the way. The first new membrane is then fed into the unit and pushed into the pressure vessel, pushing out one used element on the other side of the vessel. The process is repeated, ensuring that the used RO membranes are captured in a purpose designed catching cartridge to avoid damages, until the cleaning pig is retrieved on the receiving end, indicating that all used RO membranes have been unloaded.
The end cap on the receiving end is refitted and when confirmed and communicated, the membrane loader operator can drive the last RO membrane into the pressure vessel and with the help of a ‘push pig’, drive the RO membrane home, against the end cap on the other side. The push pig is retrieved and the end cap on the loading end is refitted, completing the loading process.
The used RO membranes can be received and handled manually with operators on a scissor lift if the elements need to be preserved. Waste bins and a forklift can also be used to catch the used membranes which can then be lowered and transported and dumped onto a larger bin for disposal.
Finalisation
Once all the RO membranes have been replaced on the RO train and all end caps have been refitted, the permeate pipework connections which connect the pressure vessels to the main permeate headers are reinstalled. The hoses connecting the permeate pipes to the taps on ground level for pressure vessel profiling purposes are also reconnected as per the labels.
Results
The collaboration between both parties resulted in a successful implementation of detailed workflow systems and a specially designed equipment suitable for the project – completed with no injuries, on time and on budget.
The first prototype was completed and was used for the replacement of the Second Pass BWRO Membranes in April to May 2021 and then later in October to November 2021 for the First Pass SWRO Membranes after implementing design adjustments from the lessons learnt from the first phase of the replacement program.
Second Pass BWRO Membrane Replacement
Second Pass BWRO Membrane Replacement was an opportunity to test out the membrane loader and the workflow developed to enable the use of the device and the team was met with challenges. The design was heavily based on the force test results which presented challenges, particularly for the Second Pass SWRO Membranes. There were numerous RO membranes with enlarged brine seals in the pressure vessel which saw the force required to push to be much higher than expected. The membrane loader was unable to push the membranes with enlarged brine seals out and the team had significant setbacks due to these.
The first Second Pass BWRO train was the slowest run as the team was getting to understand the workflow around loading (preparation) and learning the loading device itself. The team progressively got a higher average daily load rate and hit a record of 54 pressure vessels in a day, which is much higher than the conservative target of 30 vessels per day. Despite this, the team had to make a few variations but was still able to complete the replacement of the Second Pass BWRO membranes on time. All this was done with no rework or leaks associated with the membrane loader (e.g. rolled interconnector o-rings). Refer to Figure 3 below for the RO membrane loader in use during this replacement period.
Figure 3: Second Pass BWRO membrane replacement with the semi-automated membrane loader
927 used RO membranes (approximately 15 tonnes) were preserved during the Second Pass BWRO membrane replacement, sent for direct re-use instead of being disposed to landfill. These RO membrane elements were handled delicately when removed from the pressure vessel until they were repacked and placed in the container. The rest of the RO membranes that did not need to be preserved were caught by bins on forklifts. In this case, there was no need to delicately handle these RO membranes so this naturally made the loading process quicker in comparison. The workflow and equipment made available considered and accommodated the two options as required.
First Pass BWRO Membrane Replacement
The enlarged brine seal issue was unique to Second Pass SWRO Membranes and this is believed to be due to quality issues of the RO membrane parts delivered dating back to plant commissioning. The loading of the First Pass SWRO Membranes went smoothly with a record of 58 vessels loaded in one shift. There were more minor rework/leaks observed but they were associated with the end caps and the permeate pipework fitment, not with the membrane loader itself i.e. no damaged or crack interconnectors. No major reworks were required prior to commissioning of the train.
Conclusion
A collaboration between Veolia and Neumann Contractors saw the development of an RO membrane loader which was utilised during the full RO membrane replacement at GCDP. Buy-in from all parties was able to be obtained due to the novelty, significant reduction in manual handling risks (as observed) and minimal rework which has been proven historically by other sites to be very costly.
The use of the membrane loader at GCDP saw an overall loading efficiency that is comparable to manual loading, which resulted in a timely completion of the project with minimal rework – none that was associated with the loading itself – but most importantly with zero injuries.
The robust process is as important as the membrane loader and as critical to carry out the work. In reality, the process that was developed enabled the use of the membrane loader allows work to be adopted by any team and at any site; not just at GCDP.
The replacement of the RO membranes using the semi-automated membrane loader is arguably the first step in the right direction. The team was able to trial the membrane loader during the Second Pass BWRO Membranes, and refine the workflow and equipment for the replacement of the First Pass SWRO Membranes. The next step is to improve, develop further and share to industry to consider using the tool to mitigate risks from manual handling, as appropriate. There should be no compromise in quality and with proper planning and scheduling, the method and equipment should be considered for future jobs.
Acknowledgement
We thank Tina Feenstra (Veolia) for initiating and for obtaining buy-in and approvals from stakeholders to launch this project. We also thank Scott Murphy (Veolia) and Vinay Muppala (Veolia) for sponsoring the initiative and for providing design considerations. We thank Daryl Harding (Veolia), who as Project Manager of the RO Membrane Replacement at GCDP endorsed the development of the RO Membrane Loader and managed project delivery risks associated with its use. We are immensely grateful to Filippo Vico (Veolia), Gilles Beurton (Veolia) and Mark Thompson (Emerald Process Engineering) for providing technical support and design inputs which were key to the RO membrane loader. We thank Ryan Green, Wayne Buckleton, Hans van der Zouwen and the extended Neumann Contractors team for taking on all challenges head on and for engineering solutions in all shapes and forms – from smart equipment to robust systems – to deliver at a high standard.
Author Biographies
Jonathan Jo | Jonathan Jo is the Process Engineer at the Gold Coast Desalination Plant. He has worked in various professional roles across Veolia’s desalination and recycled water assets. He is an
integral member of the Veolia team and industry advocate, demonstrating technical excellence, integrity, and a passion for sustainability and innovation.
Hans van der Zouwen | Hans van der Zouwen is the subject matter expert for the
membrane replacement project. Hans is the go to Project Manager to facilitate, manage and bring together mutual project ideas to transfer them into prototype design inception, replacement procedure development, managing manufacture of equipment and successful execution of the membrane replacement works.