IoT as a Digital Enabler of a Hyper-Connected Water Utility
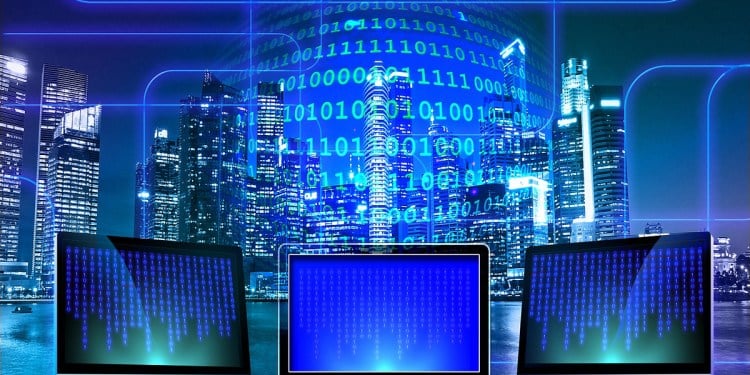
DOWNLOAD THE PAPER
Abstract
Internet of Things (IoT) provides near-real-time asset monitoring and analytics capabilities which lead to better customer outcomes, higher operational efficiency and improved asset performance. Our pilot project explored potential applications of IoT, tested a range of technologies and investigated how IoT can provide value for customers. The ability to detect a service fault before our customers do was our primary focus for this initiative, enabling proactive resolution by Sydney Water’s Customer Hub and leading to improved customer experience. This paper reports on achievements of the Customer Hub in the past year, outlines the IoT pilot project, and summarises evaluation results for different use cases, key learnings and next steps.
Introduction
After its successful initiation, Sydney Water’s Customer Hub[1] now services the entire customer base of five million people and is co-located with the System Operations Centre (SOC). The first year of Customer Hub’s operation saw a big reduction in customer impact in relation to water interruptions and a significant shift to a customer-centric mindset of the maintenance staff. To further improve customer experience, the organisation is looking for innovative approaches and technologies to support the Customer Hub in achieving the vision of being proactive in customer communications and predictive in asset management.
Internet of Things (IoT) is a promising technology which has the potential to assist Sydney Water in reducing impact on customers and the environment, delivering significant operational efficiencies and reducing WH&S risks. It is just one of a range of technologies that together with the use of machine learning and artificial intelligence can form part of the wider strategy for digital transformation within Sydney Water.
To explore IoT’s opportunities and test its maturity Sydney Water conducted an IoT trial project. Hereby, relatively inexpensive battery-powered devices monitor assets and report back readings through dedicated communication networks and software services which raise an alarm in case of variations. Furthermore, the data can teach machine learning algorithms which will predict faults, provide maintenance planning support to prevent faults from happening at all and support optimised system planning.
The project recently won the Committee for Sydney’s 2018 SMART city award for ‘Best NSW Government Initiative’. The experience and expertise acquired throughout the project will be contributed to partnerships with eight Western Sydney Councils (“Western Sydney Parklands City Group”) and as a lead technology partner with the Aerotropolis (Western Sydney Airport).
Customer Hub update
Customer Hub is a key initiative of Sydney Water’s transformation to a customer-centric organisation. The pilot commenced operation in September 2017 covering the western operational area with approximately one million people. Customer Hub was established to move from a traditional asset-centric philosophy of ‘fix the asset, fix the customer problem’, to a process that considers and minimises customer impact, provides proactive communications and case management for customers, and seeks and acts on customer feedback in real time.
The pilot delivered impressive results. In its first 12 months of operation:
- Over 100,000 properties had water interruptions avoided or mitigated, which equates to around a 30% reduction in customer impact
- Over 50,000 customers informed of water interruptions in advance
- Over 21,000 customers kept informed of progress on faults reported
- Over 80% of customers satisfied or extremely satisfied they were kept informed
- Customer experience scores recognised by the industry as excellent (currently Net Promoter Score of 56)
Following the success of the pilot, it was decided to extend Customer Hub to the full area of operation and include the Systems Operations Centre (SOC).
Incorporating the SOC improves Customer Hub’s ability in reacting to faults efficiently and in improving its capability to predict issues:
- Using the knowledge and experience of and the real-time information available to the SOC team in reacting to issues
- Leveraging the large quantity of operational data to improve predictive capability to foresee and prevent issues
To make best use of the inclusion of the SOC, all teams were co-located at a newly fitted out location in Parramatta Head Office. This move and the significant impact it had on staff and the IT environment was fully managed and delivered in-house, by Networks staff, the internal Change Management team and Digital Business.
Besides the ongoing continuous improvement activities, the following key outcomes were delivered in the last year:
People/structure
A permanent Customer Hub team was established in December 2018. Further to the SOC team the newly created EPA Liaison team, which provides the EPA with timely information and a single point of contact regarding incidents, was added to the Customer Hub.
Accompanied with the expansion of the Customer Hub to the entire Sydney Water customer base, Planners, Dispatchers and Field Resource Coordinators for North and South were moved into the Hub. These roles were combined and co-located under a single point of leadership and strategic direction.
Customer Duty Managers (CDMs) who provide oversight of the day of operations within the Hub team and for field-based staff now work closely with the SOC to identify issues that are likely to affect customers and minimise customer impact.
Processes
With the creation of a centralised planning and dispatch team in the Customer Hub, which is complemented by dedicated Planners in each of the satellite area teams, a new operating model and respective planning processes were developed, trained and introduced. Furthermore, to gain benefits from including the SOC in the Customer Hub structure, business processes were developed to improve reactive and enable proactive faults management.
An over-arching cross business Customer Journey Council has been established to identify and prioritise projects for further improvement.
Technology
2019 sees the implementation of a new Customer Relation Management and Billing System for Sydney Water. To minimise the risk of this implementation, core technology in use by Customer Hub has remained unchanged since early 2018. Therefore, the focus of our in-house Digital Business team lay in extending the existing technical capability to the whole area of Sydney Water’s operation and the relocation of Customer Hub.
Nevertheless, some smaller enhancements could be delivered:
- A newly introduced banner on Sydney Water’s “Water supply & service updates” webpage informs customers about widespread impacts that our crews are still on route to. This enhancement has already led to a noticeable reduction in “no water” calls.
- The customer notification process for completed maintenance work was streamlined
- The implementation of a new Voice of Customer measurement dashboard reduces reporting effort and allows for individual staff member dashboards that show staff member specific customer feedback.
Preliminary results of this extension are promising. The Advocacy score has further increased to 57 (on the Net Promoter Score scale).
A big portion of faults managed by the Customer Hub are detected and reported by customers via phone, email or webforms. These reporters are already directly or indirectly negatively impacted by the issue before the fault management process can be kicked off. Therefore, Customer Hub’s ultimate aim is to get ‘ahead of the issue’ and rectify any issues and potential problems before any customer even knows about it. One of the requirements to achieve this is to be able to monitor the full distribution and collection network and process the collected data accordingly.
Sydney Water’s trunk water and wastewater network is already monitored and controlled through the SCADA system (IICATS). However, most of the customer and environment impacting water leaks and sewer blockages occur in the reticulation networks of which there is limited visibility. Therefore, the traditional approach has been to rely on customers being the sensor for outages, leakages, overflows, burst mains, etc. This results in delays, poor customer experience, costs, loss of productivity, environmental impacts and compliance issues.
To achieve the next step change in reducing customer impact and increasing customer experience a better monitoring and alert system of the reticulation network is necessary. Internet of Things (IoT) is a technology which provides the capability of monitoring a vast amount of distributed assets by using small, low-cost and battery-powered devices which read and transmit data to a backend system.
This functionality in combination with advanced data analytics provided by machine learning and artificial intelligence can detect and predict service faults, support maintenance planning and recommend rectifying activities. By this means, IoT supports reducing the impact of service faults or even prevents them from happening at all.
IoT proof of value (PoV)
IoT connects objects such as sensors, meters, phones and wearables to the internet, turning them into ‘smart’ assets that can communicate with people, applications and amongst each other. This technology has the potential to transform the water industry through better visibility of the physical environment, enabling better-informed, faster decisions; automated processes and providing the data needed to predict future events.
Opportunities for Sydney Water
In alignment with Customer Hub, IoT provides significant opportunities for Sydney Water across all aspects of our business, such as:
- Digital/Smart Meters – leak alerts and online usage information for customers, more flexible billing, non-revenue water management, deferring capital investment and driving a reduction in customer water usage
- Smart Sensors, which are low power and wireless and can be deployed into reticulation areas for improved water quality and sewer operations
- Condition-Based Maintenance
- Personnel Safety (wearables), vehicle and asset
- Near real-time reporting to our key stakeholders (EPA, Health, etc.)
- Atmospheric monitoring for a range of parameters including odour, H2S, compliance, etc.
- Soil monitoring to feed into predictive models for pipe burst, etc.
- River/Stream monitoring – proactive monitoring for compliance, quality, etc.
- Use of drones to reduce WHS challenges during inspections and incidents
- Structural Health of Assets e.g. buildings, fire hydrant monitoring, etc.
Scope and goals of the PoV
The IoT PoV was set up as an opportunity to test a range of technologies on different use cases to demonstrate if Sydney Water will get value for our customers using this technology. The PoV is comprised of a technical component, which commenced in September 2017 and concluded at the end of 2018, and a data analytics component which will commence in 2019. This paper reports on the outcomes of the technical phase of the PoV.
One goal of the PoV was to demonstrate that the end-to-end process from a device in the field to an application in the office works as defined. The other aim was to provide insights and to inform a future decision on which instruments, transmitters and communication networks to continue with into production.
The following five use cases were explored:
- Detect sewer blockages in reticulation assets
- Detect and predict sewer overflows in reticulation assets
- Identify water pressure issues in reticulation assets
- Monitor and display valve positions
- Support digital metering with IoT
The trial for the water and wastewater related use cases was conducted in the Liverpool catchment/supply zone. This zone was selected because there was already one of the proposed IoT communication networks in place and the area is known for water and wastewater network related problems. A further criterion was that the Customer Hub, which is a major business user of this technology, was located in Liverpool at this time.
PoV solution architecture
One requirement of running a cost and resource efficient trial was the ability to use the same IT solution for all selected use cases. The project tested not only different sensors, transmitters and communication networks but aimed at getting insights into using an IoT platform, data store and analytic tools as well.
The solution which is based on a reference IoT architecture was designed and implemented mainly in-house by Digital Business. As this is a temporary solution which will eventually be replaced by a strategic IoT environment, the project didn’t conduct an in-depth evaluation and selection of the IoT platform components but used services which were readily available.
The IoT architecture developed for this project comprises of the following components (Figure 1):
- IoT devices (sensors, meters)
- Communication network
- Data broker & data ingestion
- Data storage & processing
- Data visualisation and analysis applications
- Configuration database
Figure 1: IoT PoV High-level Architecture
IoT devices, such as sensors and digital meters, transmit signals through low-power wide-area network (LPWAN) to a cloud-based IoT platform. Multiple LPWANs were utilised for the trial to better understand the capabilities, strengths and weaknesses of the various technologies:
- LoRa
- Sigfox
- Taggle
- Telstra NB-IOT
- 3G/4G with SCADA (IICATS)
Business users access the collected data via Power BI dashboards and an extension of the Sydney Water-developed geospatial application Spatial Hub.
The tested devices and networks were evaluated using a weighted decision criteria framework comprising of Capability, Cost, Reliability, Value (-add) and Security.
Use case: Detect sewer blockages and detect sewer overflows
The goal of these use cases is to identify sewer blockages and rising sewer levels before they become sewer overflows and affect customers or the environment negatively. An alarm raised by the system needs to leave enough time to dispatch a crew which can resolve the issue safely. The data collected should be suitable to feed a machine learning algorithm which predicts issues.
This use case comes with multiple challenges for devices and communication networks, such as:
- Potential flooding of devices (water ingress)
- Aggressive gases
- Vermin and rodents
- Reception problems, due to underground location and iron access chamber covers
Three types of sewer sensors were deployed which provide different levels of information:
- Level switches – submit a digital reading which states if a predefined sewer level is reached or not (see Figure 2)
- Ultrasonic level sensors – submit an analogue value of the sewer height in metres
- Sewer flow sensors – submit an analogue value of the sewer flow
In total, 15 different models of sensors and transmitters were tested for these use cases. The project used both off-the-shelf products and devices developed and prototypically assembled in-house by engineers from Sydney Water’s Operational Technology Services (OTS) team.
Figure 2: Sydney Water-developed and assembled IoT Sewer Level Transmitter with Float Sensor
The project installed around 330 sensors in the Liverpool area. There is no generally accepted rule of how many access chambers need to be monitored and what sensor technology to use to get full monitoring coverage of a sewer and being able to predict issues. Following a rule of thumb, initially, every 3rd access chamber was equipped with a level switch, every 30th access chamber with an analogue level sensor and every 200th access chamber with a sewer flow sensor. Additional business rules fine-tuned this selection.
This rule leads to a vast amount of monitored access chambers, probably much more than needed. However, this roll-out strategy in combination with event information delivers enough data sets to train machine learning algorithms. One of the use cases of the upcoming machine learning trial is to determine the optimal mix of monitoring devices to reliably detect blockages and predict overflows.
As Sydney Water has around 500,000 access chambers, this is an important input for a feasible business case.
The system has been operational since mid-2018 and while the period since has been mainly dry, Sydney Water has already realised some benefits:
- 21 sewer blockages were detected and cleared before customers and the environment were impacted
- One high impact overflow was averted with 4,700 properties upstream
Figure 3: IoT Sensors deployed in Liverpool
Figure 4: Anonymised Evaluation of Sewer Level Float Switches
By equipping critical sewers with monitoring devices this technology was deemed to be suitable as an alternative to preventive maintenance and can also be used to monitor breakdown maintenance effectiveness.
All sensor and transmitter models used were evaluated based on a weighted decision criteria framework comprising for this use case of Cost (40%), Reliability (25%), Capability (15%), Value (-add) (15%) and Security (5%). For future assessments, the security rating will be adapted per use case as required. Figure 4 shows the anonymised result of this evaluation; cost is on the y-axis and technical compliance, which includes all other criteria, on the x-axis. Devices placed in the upper right quadrant are qualified for the next phase of the trial.
Use case: Identify water pressure issues
This use case tests the technical feasibility of pressure monitoring at water hydrants. Monitoring pressure of reticulation pipes, combined with advanced analytics and visualisation will support Sydney Water in:
- identifying vulnerable locations, predicting breaks and locating leaks
- proactively notifying about water outages
- planning maintenance work schedules based on real-world asset condition rather than time
- determining rebates for no-water and low-pressure
Figure 5: Hydrant adapter, pressure gauge, transmitter and external antenna
A recent machine learning project conducted by Sydney Water in conjunction with external specialists concluded that more granular pressure data in a zone is needed to enable early leak detection and prediction at specific pipe locations. Battery powered, fast deployable and low priced IoT pressure sensors can provide the required sampling coverage.
The IoT pressure monitoring device is comprised of a hydrant adapter, connector to a pressure gauge and an IoT transmitter (Figure 5). Fifty-three devices of three different transmitter types were deployed. Intensive discussions with the Fire Brigade were undertaken before roll-out, including training and the provision of a tool to remove the adapter from the hydrant quickly.
Conclusion:
- The solution achieved the required accuracy at a competitive price
- The sensors are quickly installed, can be deployed temporarily and are reusable
- As the gauges are just IP67, water ingress, which led to many device failures, is a major issue, especially when installed in hydrant pits
- Installation is potentially detrimental to firefighting activities
Even though the solution delivered the data as required, an alternative to installation in hydrants needs to be considered.
Benefits realised so far:
- Water pressure sensors detected pressure fluctuation caused by water tanker extracting water from the system
Use case: Digital water meter
The majority of Sydney Water’s customers have mechanical meters which are manually read four times a year by contractors. This initiative intends to provide a digital meter at customer premises. As a basic level, the meter should be able to provide a meter reading for monthly and quarterly billing periods, daily water usage and an indication of water leakage.
The trial was mainly about testing technical reliability, connectivity and handling of different types of digital metering solutions. The upcoming extended trial aims to deliver robust insights into how digital metering can support the following goals:
- General water consumption reduction of residential properties, by changing behaviour and by detecting household leaks
- Asset investment deferral, by reducing general water usage and by better understanding and influencing usage pattern of big consumers
- Reduction in network leakage by conducting real-time water balance calculations and identifying and localising leaks
- Reduction of system losses by identifying theft, unapproved tanker fillings, etc.
The digital metering use case was commenced towards the end of the PoV period due to the unavailability of suitable digital meters. So far, the project has installed 80 digital meters comprising of a mixture of retrofits, integrated digital pulse meters and smart meters. Beside the field test, the project set up a test rig on a Sydney Water site to test reliability and functionality of selected digital meters in-house.
A portion of the tested smart meters is equipped with integrated pressure and temperature sensors. This was to determine if pressure readings at the point of connection could replace pressure sensors installed directly on mains or hydrants to deliver data required for leak prediction, detection and asset planning.
Use case: Valve position monitoring
The intent of this initiative is to determine the status of valves in the water distribution network without the need for manual communication of the information.
The open/closed status of valves in the reticulation network is not automatically recorded and updated in any system at this point. The current process relies on field crews to manually record valve position changes in the Geospatial Information System (GIS).
Sydney Water engineers developed a prototype of a monitoring device which can be attached to valve keys and actuators. It contains a magnetic compass to determine the direction and the number of valve rotations and GPS to gather the location. The prototype device uses Bluetooth to send the readings through a mobile phone. A device which communicates through LoRa directly is currently in development.
Key outcomes of the trial are:
- The device works well, submitting all the required data
- The magnetic compass is inaccurate when the device is mounted on a magnetised steel valve key
- GPS location is not accurate enough to distinguish between valves in close proximity
There is further research and development necessary before this solution can be considered.
Outcomes and conclusion
The project gathered a lot of experience, know-how and market insights, some of the key learnings are discussed below.
Key learnings
- IoT is an immature marketplace – especially regarding suitable devices for sewers. Many of the sourced devices failed. Sydney Water’s self-developed and prototypically-produced devices showed good reliability.
- Cost of (un)reliability is critical to the desired outcome.
Re-visiting a device for replacement or calibration results in high life-cycle costs and makes the business case unfeasible. - Logistics and coordination of IoT device deployment is very complex in distribution networks. Contrary to work around the trunk system, deploying monitoring devices in the reticulation system frequently involves discussions with customers, information and negotiation with councils and agencies and the need for traffic control.
- Interoperability does not yet exist at any layer of the IoT ecosystem. For example, there is no transmitter device which can be used for all tested use cases.
- Technology is only really at the emergent stage at all layers of the IoT ecosystem.
- Device Management is a key consideration. Currently, a new device needs to be commissioned and registered individually at every level of the IoT ecosystem.
- Most vendors are not really considering security adequately – there is an assumption and requirement that this will change in the near future. Currently, data security requirements need to be assessed on a use case by use case basis before operationalising IoT. Nevertheless, the current state of IoT security features led to the decision that IoT will be used for non-mission critical monitoring activities only and not included in control tasks at this point.
Figure 6: Anonymised Comparison of IoT Transmitters for Sewer Level Sensors
Technology evaluation result
Sensor, transmitters and communication networks were evaluated using the weighted decision criteria framework comprising of Cost, Reliability, Capability, Value (-add) and Security. This evaluation enabled the project putting forward a recommendation for a technology mix for an extended trial. Each device and communication network supplier involved in the trial was provided with anonymised evaluation results which show the suppliers’ position in relation to the competition (Figure 6).
Conclusion
This trial has proven that the IoT technology can provide cost-effective and proactive customer outcomes. However, it should be noted that this is an immature and fast emerging technology and careful analysis needs to be undertaken in developing standards, technology choices and decision criteria at all levels of the IoT ecosystem.
Therefore, Sydney Water will extend this trial and deploy up to 10,000 additional sensors and digital meters to be able to robustly evaluate technologies and support an informed decision on the implementation of IoT across the whole area of operation. This thorough assessment will also inform future revisions of asset standards to ensure that all newly built environments incorporate appropriate technology choices to allow us to drive improved customer outcomes and contribute to the truly smart cities of the future.
Sydney Water will take on collaboration opportunities with local councils, universities and agencies and plans to implement a customer portal to provide access to a subset of the data to customers and collaboration partners.
The ability to capture more and higher frequency of data will drive predictive analytics and machine learning capability with the ultimate goal of delivering artificial intelligence to support operations decision-making and enabling cognitive automation.
IoT is just one of a range of technologies that are being deployed by Sydney Water to realise their vision of being a truly digitally hyper-connected utility. This, along with data from drone technologies, Building Information Modelling (BIM), asset performance data and hydraulic models will be utilised to deliver Digital Twins of assets, systems and cities that will transform the way that planners and operators of the future work in a modern utility.
Acknowledgment
The authors would like to acknowledge the hard work, dedication, curiosity and out-of-the-box thinking of all members of the IoT project team which led to this highly anticipated result and numerous innovative solutions. We thank all stakeholders and the Sydney Water Executive for their support and motivation.
About the authors
Christoph Prackwieser | Christoph Prackwieser is the project manager of Sydney Water’s Internet of Things (IoT) initiative. Having joined Sydney Water in 2013, he has managed the delivery of several high-profile business improvement projects, implemented a 5-year planning process for treatment assets and led the process design for the Customer Hub implementation.
Darren Cash | Darren Cash is the manager of Sydney Water’s Customer Hub, a team that focuses on minimising the customer impact of daily operations and provides an excellent experience for any affected customers. Darren is an engineer with 28 years’ experience in the water industry and a passion for delivering exceptional customer service.
Michael Wassell | Mike Wassell is the Head of Operational Technology Services (OTS) at Sydney Water. Sydney Water supplies water and sewerage services to over four and a half million people. Mike has responsibility for all SCADA and automation within the organisation as well as the Internet of Things (IoT) portfolio.