How CO2 curing can turn alum sludge into construction material
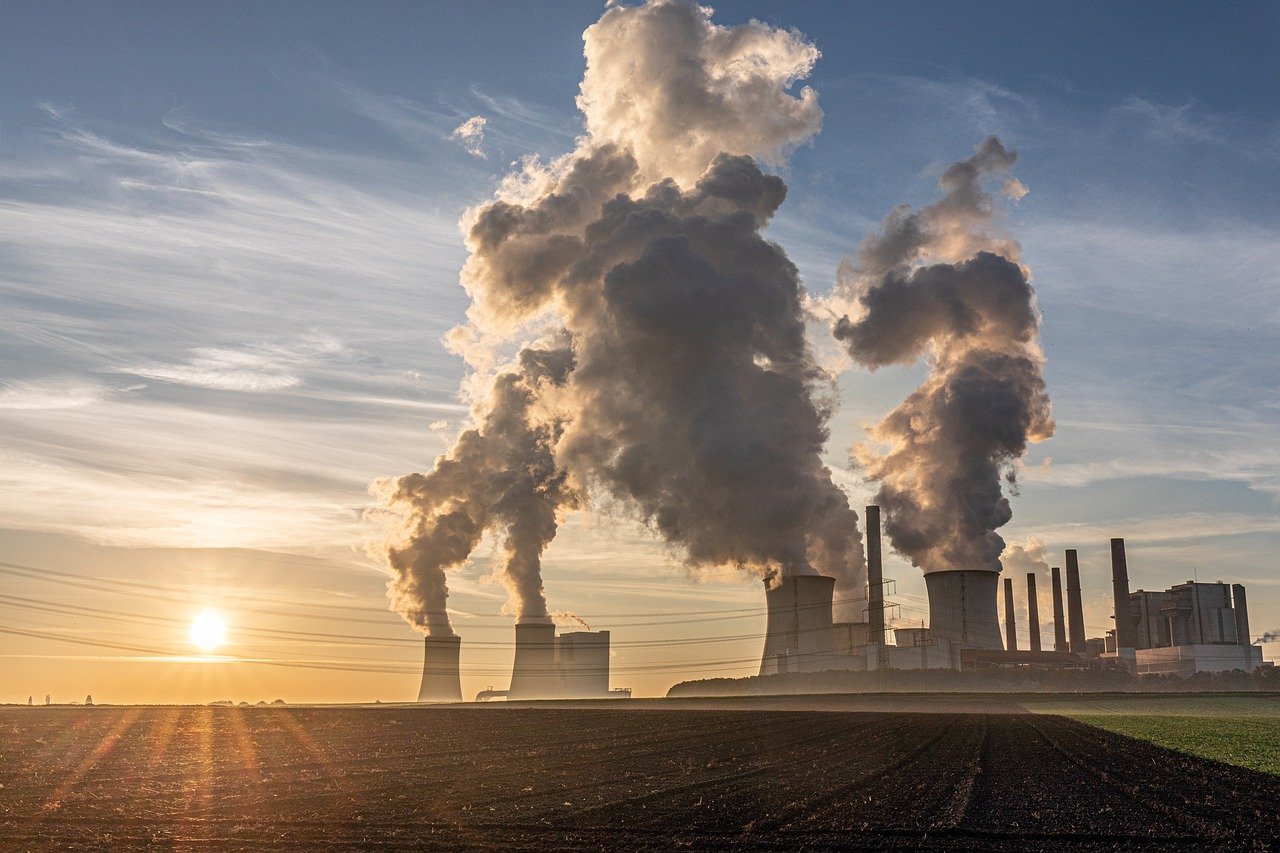
Up to 10% of cement in concrete can be replaced with a water treatment by-product
DOWNLOAD THE PAPER
ABSTRACT
Alum sludge is produced as a by-product of drinking water treatment processes when aluminium sulfate is used as a coagulant. For the last decade, sludge production has increased significantly with increasing demand for drinking water due to population growth, and a green and economic management strategy is needed for this sludge. Based on our recent studies, alum sludge is a feasible substitute to replace either sand or cement in concrete blocks, which could be an efficient way to dispose of and reuse the sludge as raw material for this concrete product. For sand replacement, oven-dried sludge may deteriorate the mechanical and durability performance of concrete blocks due to its organic content hindering the cement hydration. An advanced technology, named CO2 curing, can improve the performance of sludge-derived concrete, e.g., compressive strength and resistance to sulfate attack. Also, the CO2 curing method has benefits for recycling of the abundant CO2 in the ambient environment. For cement replacement, grinding and calcining procedures have to be applied to eliminate the organic content and activate the pozzolanic activity of sludge. The obtained results show that a maximum of 10% cement can be replaced by alum sludge ash without compromising the mechanical performance of concrete blocks. This paper gives a summary of the latest alum sludge application studied by our research team.
Keywords: Alum sludge; Value-added recycling; Concrete blocks; Early-age CO2 curing
INTRODUCTION
Global population growth has led to a significant increase in drinking water demand. The amount of water treatment sludge, which is a by-product generated during drinking water treatment processes, is consequently increased. In the United States, more than two million tons of sludge are generated from more than 16,000 drinking water treatment systems (Frías et al., 2014). The Googong Water Treatment Plant, located in New South Wales, Australia, which has a 270 ML/day water production rate, is reported to produce approximately 2000 tons of dried sludge annually (Maiden et al., 2015). In addition, the South Australian Water Corporation produces more than 40,000 tons of sludge annually. Since an aluminium-based compound is usually used as a coagulant in the coagulation process, the sludge could contain high aluminium content, therefore the name alum sludge. Alum sludge can be regarded as a non-hazardous waste, and it is disposed of either in landfills or to the sewer (Ahmad et al., 2016; Ahmad et al., 2018). However, the cost for the disposal of alum sludge can reach between $130 - $200/ton with a road transport cost of $30 - $40/ton (Maiden et al., 2015). Therefore, more economical and environmentally friendly solutions for sludge management are required by the water industry.
There are currently several sustainable reuse options for such sludge, e.g., recovery and reuse of coagulants from alum sludge, reuse of alum sludge in sewage sludge dewatering, and reuse of alum sludge in concrete products (Ahmad et al., 2016). Compared with other methods, the reuse of alum sludge in concrete could be a more sustainable approach because of the vast consumption of concrete products. Concrete is the most consumed construction materials, and the usage of concrete is fast
increasing. Natural aggregate and cement are essential components of concrete, and demand is consequently increasing. The total amount of Australian cement production in 2018-19 increased by 8.5% from 9.6 to 10.4 million tons, with 5.1 million tons GHG being released into the atmosphere (CIF, 2020). One solution to alleviate the pressure on cement demand is replacing cement with supplementary cementitious materials (SCMs), which have lower CO2 emissions. SCM is a material that normally contains a high content of silica, alumina, and ferric, which does not exhibit cementitious property in contact with water. However, it can react with calcium hydroxide generated from cement hydration, forming additional calcium silicate hydrate (C-S-H) and calcium aluminate silicate hydrate (C-A-S-H) gel. Also, to avoid excessive extraction of natural sources, alternative materials to partially replace the nature aggregates in concrete need to be explored. The main components of sludge are alum and silica; thus, it can be used in concrete as either SCM or an alternative aggregate material.
Some research work has already been done on the use of alum sludge in concrete products. For instance, Owaid et al. (2014) calcined the alum sludge at 800 ℃ for two hours to pyrolyze the organic compound and activate the pozzolanic activity of the alum sludge ash. The results showed that the mortar sample's compressive strength was improved when no more than 15% of the cement was replaced with alum sludge ash (ASA). Also, Bohórquez González et al. (2020) showed a comparable 28-day compressive strength to reference samples when 10% ASA was used to replace cement. On the other hand, Wang et al. (2018) added alum sludge as a sand replacement in a cement-based material, and the results exhibited that the sludge addition resulted in a long setting time and low compressive strength. The organic matter in sludge could significantly hinder cement hydration. Furthermore, Gomes et al. (2017) directly used wet sludge to replace sand, and the tensile strength of samples with 5% sludge decreased to 2.02 MPa, and a further decrease up to 1.79 MPa and 0.35 MPa was found for samples with 7% and 10% sludge, respectively. These results can be attributed to the degraded interface between sludge and cement matrix in comparison with that of sand.
To further investigate the feasibility of utilising alum sludge in concrete blocks (CB), the mechanical and durability properties, the leachate behavior, and the microstructure of CB with either cement or fine aggregate replaced by different proportions of the alum sludge ranging from 0% to 30% have been investigated by our research group. In addition to standard curing, an advanced CO2 curing technology was also studied.
PHYSICAL AND CHEMICAL CHARACTERISTICS OF THE ALUM SLUDGE
The alum sludge was sourced from a local water treatment plant in Adelaide, South Australia. Using the alum sludge to replace sand in CB, the raw alum sludge was crushed to pass through a 1.68 mm sieve and then oven-dried at 105℃ for at least 24 h to remove the moisture. Images and the particle size distribution of the crushed alum sludge and sand are shown in Fig.1a.
Fig.1. the particle size distribution of (a) sand and crushed alum sludge and (b) cement and ASA (Liu et al., 2020a; Liu et al., 2020d)
To replace cement in CB, further treatment of the alum sludge is required. The alum sludge was first calcined in a muffle furnace at 800℃ for two hours. After calcination, the alum sludge was then ground to pass through a 75 µm sieve. The ASA is slightly coarser than the cement clinkers, shown in Fig. 1b. The chemical composition of the raw alum sludge and ASA as analysed using x-ray fluorescence is shown in Fig.2. The primary chemical components of the raw alum sludge include alumina, silica and organic matter, occupying more than 80% of the total, followed by ferric and lime, accounting for 8% and 5%, respectively. Compared with raw sludge, ASA exhibits only a 6% loss on ignition (LOI), indicating the effective elimination of organic matter by such a heat treatment method.
Fig.2. chemical composition of (a) raw alum sludge and (b) alum sludge ash (modified from (Duan et al., 2020b))
Although the calcination of alum sludge would consume a significant amount of energy, the required temperature (800℃) is far lower than the temperature (more than 1400℃) to produce cement. Therefore, replacing a proportion of cement with ASA is feasible to reduce energy consumption and decrease CO2 emissions.
APPLICATION OF ALUM SLUDGE AS SAND REPLACEMENT IN CONCRETE BLOCKS
Compressive strength
Our research group replaced sand using alum sludge at weight percentages of 0%, 10%, 20% and 30%. Some sludge-derived CB were cured in a chamber with a controlled temperature and humidity (95 % humidity and 23 ± 2 °C), named normal curing. Some blocks were stored in a carbonation chamber with a CO2 concentration of 10% in the first 24 h and then transferred to the standard curing chamber for 27 d.
Fig. 3 shows the one-day and 28-day compressive strength of CB under CO2 or normal curing. The compressive strength of CB decreased with increasing sludge content from 0 to 30%. The detrimental effect of sludge incorporation could be attributed to high-water absorption and high organic matter content. A large amount of water is absorbed by sludge, which makes fresh mixtures lack cohesiveness. Such reduced cohesiveness could damage the homogeneity and integrity of CB during the compaction procedure, resulting in deteriorated mechanical and durability performance. Also, the organic matter significantly hinders cement hydration.
Fig. 3. 1-day and 28-day compressive strength of CB with varying alum sludge content (modified from Liu et al. (2020b)).
CO2 curing significantly improves the compressive strength of CB, especially for CB with 30% alum sludge. The compressive strength of CB-30-C increased by 373% and 172% at the age of one-day and 28-day respectively relative to CB-30-N. The increase in compressive strength could be attributed to the formation of crystalline CaCO3 and the decomposition of excessive ettringite derived from sludge addition. In Fig. 4a, the formation of small crystalline CaCO3 by carbonation reaction contributes to a denser cement matrix by filling effect. Compared with Fig. 4b, Fig. 4a indicates that the ettringite is prone to react with CO2, and it can be decomposed to CaCO3, which is beneficial to the strength development of CB (T GROUNDS et al., 1988).
The compressive strength of CB incorporating sludge meets the requirement of 7.5 MPa for non-load-bearing blocks. Furthermore, block samples subject to CO2 curing can also be used for load-bearing applications (12.5 MPa), according to BSEN771 (2011).
Fig. 4. SEM images of CO2 and normally cured block samples with 30% sludge. (a) CB-30-C, and (b) CB-30-N (Liu et al., 2020b).
Sulfate resistance
Sulfate attack in concrete products is the primary concern for long-term service life, especially for areas containing large quantities of soluble sulfates, such as Adelaide, South Australia (Neville, 2004). The chemical reaction generally produces ettringite and gypsum, causing expansion, and leading to the generation of micro-cracks. Also, physical attack, as another form of sulfate attack, is attributed to the deposition of crystalline salts in capillary pores. The generation of crystallisation pressure can cause significant spalling on the surface of the concrete (Scrivener, 2004).
In our research, chemical and physical sulfate attacks to CB were studied by introducing wet and dry cycles. The sulfate attack test was conducted for 40 cycles, and each cycle began with the immersion of the CB in a sodium sulfate solution for two hours, and finished by drying in an oven fixed at 65 ± 2°C for 20 ± 1 h. Images of samples after 40 cycles, with varying content of sludge, are shown in Fig. 5.
Fig. 5. Visual inspection of block samples after 40 cycles of sulfate attack (Liu et al., 2020e).
Fig. 5 shows that sulfate attack induced deterioration, such as spalling and cracking, becomes more severe with increasing sludge content. Also, CO2 curing significantly improves the sulfate resistance of CB. For instance, the CB-30-N exhibits a significant sign of surface spalling and loss of corner parts, but the CB-30-C remained structurally intact with a moderate degree of spalling. The other parameters to assess sulfate resistance are also discussed, e.g., mass loss, compressive strength change, and ultrasonic pulse velocity variation (Liu et al., 2020b, c). A similar trend was found with the results of visual inspections.
These results can be explained by the fact that the addition of sludge led to a porosity increase in block samples, which has been proved by analysis using x-ray computed tomography (Liu et al., 2020e). Such porosity increases make the sulfate solution penetration to the inner part of the CB easier, resulting in the acceleration of concrete deterioration. CO2 curing refined pore sizes and reduced their connectivity. The refinement effect can efficiently reduce the degree of salt crystalline in pores and delay the chemical reaction between sulfate ions and the cement matrix that produces expansive ettringite or gypsum.
Leaching behavior
The toxic characteristic leaching procedure (TCLP) test for sludge from a local water treatment plant in Adelaide shows the leaching concentration of Cu (1.8 mg L-1) may exceed the most popular “guideline value” of 1.0 mg L-1, which is accepted by many countries (James, 1998). Therefore, the leaching behavior of CB incorporating alum sludge was studied using two methods, a traditional TCLP test based on USEPA (1992), and a long-term leaching test under environmental conditions similar to that of the real scenario based on Shi and Kan (2009). The results of both tests prove that all elements are well immobilized, and the CB incorporating alum sludge are non-hazardous.
APPLICATION OF ALUM SLUDGE AS CEMENT REPLACEMENT IN CONCRETE BLOCKS
Pozzolanic reactivity of alum sludge ash
To replace cement, pozzolanic materials should react with portlandite in the presence of moisture to produce binding gels similar to those formed by cement hydration. Without calcining, alum sludge either poses no or only little pozzolanic reactivity. Therefore, alum sludge was calcined in a muffle furnace at 800°C for two hours and then ground to less than 75 µm, in which the size obtained by the alum sludge ash (ASA) exhibited a Blaine fineness value similar to cement clinkers (Liu et al., 2020d). The pozzolanic reactivity of ASA has been tested using two methods, an indirect method based on ASTM C618 (2019) and a Frattini test according to BS EN 196-5 (2011). The indirect method uses ASA to replace 20% of cement by weight in designed mortar samples. If either the 7-day or 28-day compressive strength of ASA-derived mortar can achieve 75% of the mortar without incorporating ASA (reference ones), the pozzolanic reactivity could be confirmed (ASTM C618, 2019). The results in Fig. 6a indicate that the compressive strength of mortar samples containing ASA is 84% and 114% of the reference samples at seven days and 28 days, respectively, which meet the required 75%. For the Frattini test, ASA consumes additional portlandite due to its pozzolanic reaction, resulting in the CaO concentration being underneath the saturation curve (see Fig. 6b).
Fig. 6. Evaluation of pozzolanic reactivity of ASA via (a) compressive strength and (b) Frattini test (Liu et al., 2020d)
Compressive strength
Fig. 7 shows the results of the compressive strength of ASA-derived CB. At seven days, the compressive strength of ASA-derived blocks decreases with increasing ASA content. The reduced strength could be attributed to the cement dilution effect, delayed pozzolanic reaction, and/or the incompatibility of unreacted ASA with the binder matrix. At 28 days, the compressive strength of blocks with 10% ASA exhibits a comparable strength to reference ones. In addition, the gaps in compressive strength between other ASA-derived CB (20% and 30% ASA) and the references decrease with increasing curing time. The negative effect of ASA addition, such as weak hardness and incompatibility of unreacted ASA, significantly deteriorated the mechanical performance of the blocks. However, such an effect is mitigated by the pozzolanic reaction in longer curing times. For the moderate replacement ratio, e.g., 10% cement replaced by ASA, the ASA's effects from both the positive (pozzolanic reaction and filler effect) and the negative (weak inclusion, bad compatibility, and cement dilution) seem to be balanced. Therefore, 10% is the optimum replacement ratio.
Fig. 7. Compressive strength of ASA-derived blocks relative to the blocks containing 0% ASA (modified from Liu et al. (2020d)).
Alkali-silica reaction
Alkali-silica reaction (ASR), commonly known as "concrete cancer", is the reaction that occurs between the alkaline from the pore solution in cement and the amorphous silica from the aggregate in the presence of moisture. The product of the reaction is a viscous gel, which exerts intense expansion pressure inside the cement matrix, causing cracking or even the failure of the concrete. Using reactive aggregate such as ground waste glass could lead to more severe ASR damage due to the high content of amorphous silica. The previous studies (Chappex and Scrivener, 2012; Hay and Ostertag, 2019) have demonstrated that aluminium in cement could effectively mitigate ASR. In our studies, an accelerated ASR test was undertaken, and the results exhibited that 10% to 20% replacement of cement with ASA could mitigate or even prevent ASR due to the enrichment of alum in ASA (see Fig. 8).
Fig. 8. Expansion of the mortar sample containing ASA under accelerated ASR test (modified from Duan et al. (2020a))
ECONOMIC AND ENVIRONMENTAL ANALYSIS
The economic, social and environmental impacts of using ASA to replace cement have been studied and are briefly reported here. A multiobjective mixed-integer linear programming model has been proposed to design and optimise the ASA-derived cement supply chain by maximising the social benefit, reducing greenhouse gas (GHG) emissions, and maximising net present value (NPV). Meanwhile, uncertainty and sensitivity analysis, using Monte Carlo methods, on the designed supply chain were conducted to provide a comprehensive understanding of the proposed supply chain. A case study was introduced to assess the feasibility and applicability of the model, and the corresponding data was obtained from an Australian water utility. The baseline case showed that the proposed supply chain could add 9.3 million working hours, which is equivalent to 230 full-time work opportunities per year across the future 20 years. The reduction of GHG emissions was approximately 19.8 million tonnes per year, and achieved an AU$1.93 billion NPV over a 20-year planning horizon. The uncertainty analysis and sensitivity analysis results indicated that the production rate of alum sludge is the most important factor to key model outputs.
CONCLUSIONS
After crushing, grinding and calcining, the alum sludge derived from the drinking water treatment plant was successfully incorporated into CB. With up to 30% replacement of fine aggregate with the alum sludge, the compressive strength of the block samples is still above the value specified for non-load-bearing blocks. Under CO2 curing, the compressive strength of CB can also meet the requirement for load-bearing applications. Moreover, CO2 curing can improve the sulfate resistance of concrete blocks incorporating alum sludge. The leaching test proved that the application of alum sludge into concrete blocks is safe.
For cement replacement, 10% cement replacement with the ASA could result in a comparable compressive strength relative to the reference sample at 28 days and an even higher compressive strength value at 90 days. Such reinforcement can be attributed to the pozzolanic reaction of ASA. The accelerated ASR test shows that 20% ASA content can effectively prevent the occurrence of ASR.
ACKNOWLEDGMENTS
The authors would like to acknowledge UniSA and SA Water for the research scholarship and financial support for this project. The authors would like to thank Adelaide Brighton Cement for the supply of cement.
REFERENCES
Ahmad, T., Ahmad, K., Alam, M., 2016. Sustainable management of water treatment sludge through 3‘R’ concept. Journal of Cleaner Production 124, 1-13.
Ahmad, T., Ahmad, K., Alam, M., 2018. Investigating calcined filter backwash solids as supplementary cementitious material for recycling in construction practices. Construction and Building Materials 175, 664-671.
ASTM C618, 2019. Standard Specification for Coal Fly Ash and Raw or Calcined Natural Pozzolan for Use in Concrete. American Society of Testing Materials.
Bohórquez González, K., Pacheco, E., Guzmán, A., Avila Pereira, Y., Cano Cuadro, H., Valencia, J.A.F., 2020. Use of sludge ash from drinking water treatment plant in hydraulic mortars. Materials Today Communications 23.
BS EN 196-5, 2011. Methods of testing cement Part 5: Pozzolanicity test for pozzolanic cement. BRITISH STANDARD, UK.
BSEN771, 2011. Specification for masonry units. Clay masonry units. British Standards Institution.
Chappex, T., Scrivener, K.L., 2012. The influence of aluminium on the dissolution of amorphous silica and its relation to alkali silica reaction. Cement and Concrete Research 42, 1645-1649.
CIF, 2020. Australia Cement Report. http://www.cement.org.au/Portals/0/Documents/CIF%20Publications/CIF%20Industry%20Report%202017.pdf.
Duan, W., Zhuge, Y., Pham, P.N., W. K. Chow, C., Keegan, A., Liu, Y., 2020a. Utilization of Drinking Water Treatment Sludge as Cement Replacement to Mitigate Alkali–Silica Reaction in Cement Composites. Journal of Composites Science 4.
Duan, W., Zhuge, Y., Pham, P.N., WK Chow, C., Keegan, A., Liu, Y.J.J.o.C.S., 2020b. Utilization of Drinking Water Treatment Sludge as Cement Replacement to Mitigate Alkali–Silica Reaction in Cement Composites. 4, 171.
Frías, M., Vigil de la Villa, R., de Soto, I., García, R., Baloa, T.A., 2014. Influence of activated drinking-water treatment waste on binary cement-based composite behavior: Characterization and properties. Composites Part B: Engineering 60, 14-20.
Gomes, K., Ramirez, Edna, P., Bianca, G.d.S., Mauricio, C., 2017. Potential uses of waste sludge in concrete production. Management of Environmental Quality: An International Journal 28, 821-838.
Hay, R., Ostertag, C.P., 2019. On utilization and mechanisms of waste aluminium in mitigating alkali-silica reaction (ASR) in concrete. Journal of Cleaner Production 212, 864-879.
James, F., 1998. Safety guidelines for copper in water. American Society for Clinical Nutrition 67, 1098S-1102S.
Liu, Y., Zhuge, Y., Chow, C.W.K., Keegan, A., Li, D., Pham, P.N., Huang, J., Siddique, R., 2020a. Properties and microstructure of concrete blocks incorporating drinking water treatment sludge exposed to early-age carbonation curing. Journal of Cleaner Production 261, 121257.
Liu, Y., Zhuge, Y., Chow, C.W.K., Keegan, A., Li, D., Pham, P.N., Huang, J., Siddique, R., 2020c. Utilization of drinking water treatment sludge in concrete paving blocks: Microstructural analysis, durability and leaching properties. Journal of Environmental Management 262.
- Liu, Y. Zhuge, C.W.K. Chow, A. Keegan, P.N. Pham, D. Li, J.-A. Oh, R. Siddique, The potential use of drinking water sludge ash as supplementary cementitious material in the manufacture of concrete blocks, Resources, Conservation and Recycling 168 (2021).
Liu, Y., Zhuge, Y., Chow, C.W.K., Keegan, A., Pham, P.N., Li, D., Qian, G., Wang, L., 2020e. Recycling drinking water treatment sludge into eco-concrete blocks with CO2 curing: Durability and leachability. Science of The Total Environment 746.
Maiden, Hearn, M., T,W., Boysen, R.I.C., P. , Warnecke, 2015. Alum Sludge Re-Use, Investigation (10OS-42) Prepared by GHD and Centre for Green Chemistry (Monash University) for The Smart Water Fund, Victoria, ACTEW Water & Seawater, Melbourne, Australia.
Neville, A., 2004. The confused world of sulfate attack on concrete. Cement and Concrete Research 34, 1275-1296.
Owaid, H.M., Hamid, R., Taha, M.R., 2014. Influence of thermally activated alum sludge ash on the engineering properties of multiple-blended binders concretes. Construction and Building Materials 61, 216-229.
Scrivener, K.L., 2004. Backscattered electron imaging of cementitious microstructures: understanding and quantification. Cement and Concrete Composites 26, 935-945.
Shi, H.S., Kan, L.L., 2009. Leaching behavior of heavy metals from municipal solid wastes incineration (MSWI) fly ash used in concrete. J Hazard Mater 164, 750-754.
T GROUNDS, B G MIDGLBY, NOVEL, D.V., 1988. Carbonation of ettringite by atmospheric carbon dioxide.
USEPA, 1992. Toxicity Characteristic Leaching Procedure, U.S. Environmental Protection Agency. Washington, DC, USA, 1992.
Wang, L., Zou, F., Fang, X., Tsang, D.C.W., Poon, C.S., Leng, Z., Baek, K., 2018. A novel type of controlled low strength material derived from alum sludge and green materials. Construction and Building Materials 165, 792-800.
THE AUTHORS
Yan Zhuge
Yan is a Professor at UniSA STEM, UniSA. She has a PhD in Structural Engineering from QUT. Prof Zhuge’s main research interests include green concrete materials, composite materials and structures. She has published more than 200 SCI technical papers and has been invited as a keynote speaker in conferences. She was the winner of 2018 Winnovation award.
Christopher W.K. Chow
Christopher is the Professor of Water Science and Engineering and the Director of ScaRCE, UniSA STEM, University of South Australia. Chris worked as an industry researcher for over 20 years with SA Water. He has been involved in a number of major water supply research projects.
Alexandra Keegan
Alexandra is the Manager Catchments, Wastewater and Environmental Sciences, at SA Water. Alex gained her PhD in Applied and Molecular Ecology in 2001 and worked as an industry researcher for over 20 years. Significant work includes developing methods to validate pathogen (virus and protozoa) removal and inactivation in wastewater treatment and COVID surveillance in wastewater.
Yue Liu
Yue is a PhD candidate at University of South Australia. Before starting his PhD, he worked as an aircraft designer for three years in China and obtained a master degree in mechanical engineering from The University of Adelaide. His research focuses on waste-to-energy technologies, cement-based construction materials, CO2 sequestration and utilization.
Weiwei Duan
Weiwei is a Ph.D. candidature in Civil Engineering at UniSA STEM. He has a bachelor's degree in Water Supply and Sewage Engineering and a master's degree in Civil and Environmental Engineering. His research interest includes cement materials and microbiologically induced corrosion.