Gas Infusion technology: An innovative way to oxygenate and treat wastewater
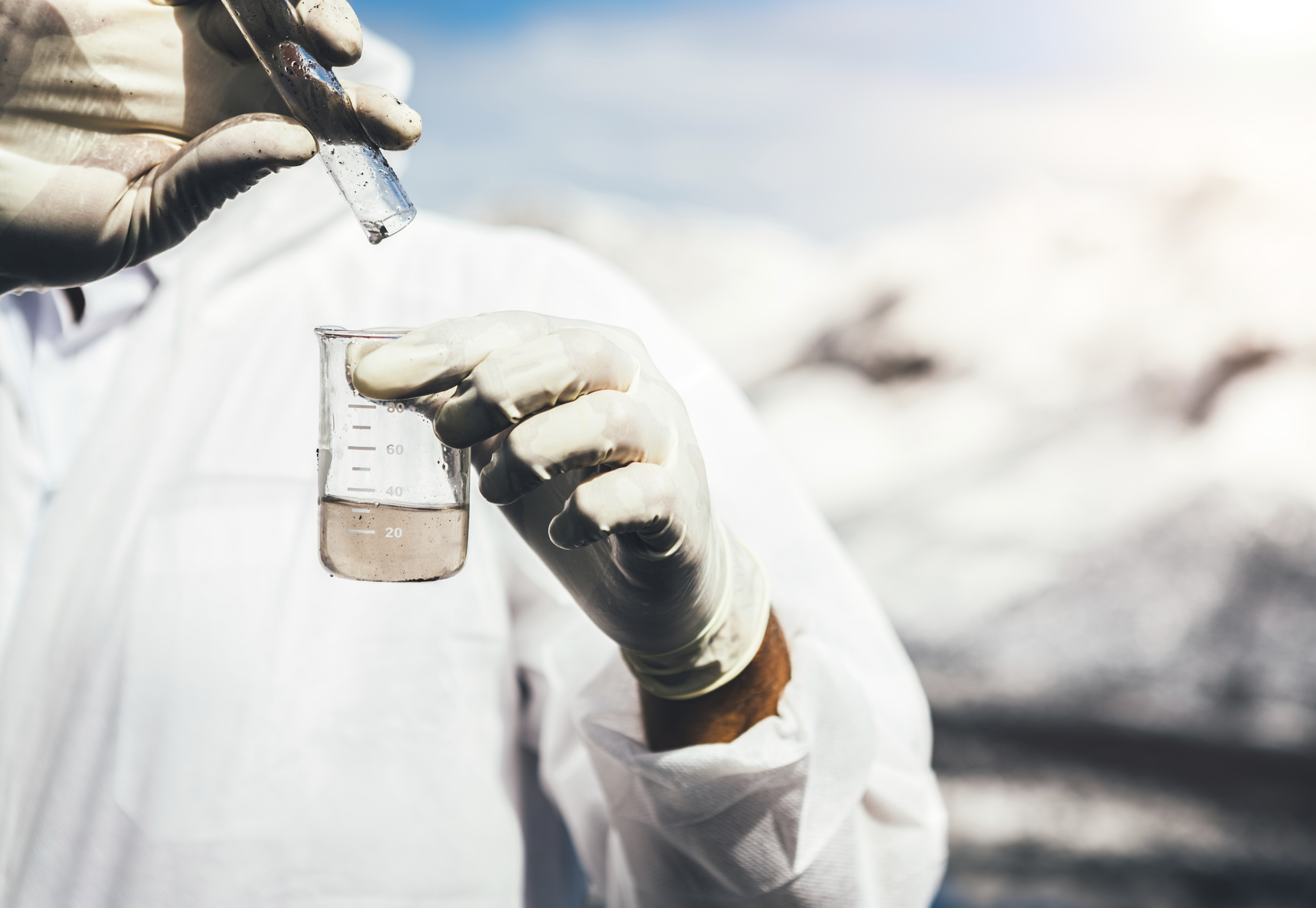
DOWNLOAD THE PAPER
Abstract
Gas Infusion is a technology which promotes a high-rate of oxygen dissolution in aqueous streams and has been used in many processes that requires oxygen, such as aquaculture, aquifer remediation, algae bloom reduction, and beverage production, amongst others.
Gas Infusion can maintain higher oxygen levels in liquids due to a proprietary gas-exchange process, allowing the introduction of pure oxygen in a bubble-less manner, creating a stable liquid stream containing enormous quantities of dissolved oxygen.
The utilisation of Prosper’s Gas Infusion technology as the primary oxygen provider for a conventional activated sludge wastewater treatment is now the hypothesis to be proved.
This paper evaluates Gas Infusion technology based on the results from full scale pilot plants developed for Canadian and Brazilian utilities.
One of the goals of the pilots was primarily prove the efficacy of the process in terms of oxygen introduction and Biochemical Oxygen Demand (BOD) removal. Another goal was to get better understanding on how a full-scale system could be configured and the implications on capital and operational expenditures (CAPEX and OPEX, respectively) of wastewater green-field plants implementation.
Introduction
Pure oxygen utilisation at wastewater treatment plants (WWTP) is not a new technique and it’s becoming more and more attractive compared to conventional aeration in general, due the development of efficient dissolution systems since its first commercial use in 1970. The main advantages of pure oxygen systems include; improved activated sludge process biokinetics, reduced power requirements and smaller biological reactors (Shammas and Wang 2008).
One type of typical oxygen introduction system at WWTPs uses a staged oxygenation at covered tanks equipped mixers and submerged propellers. The mass transfer is accomplished with the use of mixers and propellers in each stage requiring a gas/liquid mixture interface and sparging oxygen bubbles into the mix liquor.
Figure 1 shows a flow diagram for covered activated sludge with oxygen introduction.
Figure 1: Typical flow diagram of oxygen activated sludge process (Shammas and Wang 2008)
Gas Infusion technology encompasses an innovative mass transfer operation whereby sparingly soluble gases (like oxygen) are dissolved in liquids in a completely bubble-less fashion. The efficiency of this mass transfer allows the production of stable liquid streams containing enormous quantities of oxygen dissolved on scales ranging from 20 to 350 mg/l.
Gas Infusion technology uses mass transfer modules allocated into vessels, called Inline Liquid Saturators (ILS). Those modules contain hydrophobic microporous hollow fibres, providing approximately 7,000 square metres of interface area per cubic metre of fibre for mass transfer of gas into the aqueous stream.
The hydrophobic nature of the fibres allows the gas to be present within a fibre micropore at a little bit lower pressure than the liquid it is transferring to. This means that the transfer can take place without the formation of bubbles. It is also possible to raise both the liquid and gas pressures in the vessels such that the liquid is infused with higher gas concentrations previously unheard of outside of a laboratory environment.
How Gas Infusion works
Gas Infusion’s basic concept is to obtain an oxygen supersaturated stream created in the ILS vessels. The supersaturated stream is obtained in a process where water is pumped through the ILS and its fibre modules, passing over the large surface area of the gas-filled fibres. As the water passes over the fibre, due to the solubility of gases, the oxygen molecules inside the fibre are absorbed by the water flowing over the fibre following Henry's Law that defines the liquid oxygen maximum concentration depending on many variables like pressure, temperature, altitude, amongst others.
Inside the ILS, a simultaneous process occurs where other absorbed gases such as nitrogen and carbon dioxide are pushed out of the water and vented off. This “exchange” of gas process is what allows for the stable and long-term retention of oxygen within the infused water. The swapping process makes more room for oxygen, or the gas being infused into the water allowing for higher concentrations of gas to be dissolved into the aqueous stream without changing the overall gas pressure in the liquid.
Transferring of the gas to the liquid is only the first part of an entire Gas Infusion process. For oxygen especially, the downstream uses would typically occur at atmospheric pressure. The Gas Infusion portion of the process must necessarily be followed by a pressure reduction of the high gas content liquid in order for the gas (oxygen, for instance) to be utilised. Once reduced in pressure, the liquid by definition would be supersaturated. As the pressure is relieved, the liquid moves through the stages of being less than saturated, to saturated, and finally to being supersaturated. This pressure reduction should be performed correctly, otherwise gas could immediately come out of the solution in the form of bubbles. When the pressure is reduced properly and the oxygen reaches levels above 400% to 500% saturation, extremely fine bubbles of 20 microns or less may appear within the aqueous stream due to the fact that there is no more “room” in the water for more oxygen. However, these bubbles will not break the surface tension of the water and therefore are much more readily available for the biological or chemical processes they were intended for.
The Gas Infusion concept applied for a wastewater treatment process may be visualised in Figure 2.
Figure 2: Gas Inline Liquid Saturator (ILS) scheme
The wastewater mix liquor stream is pumped into the Inline Liquid Saturator (ILS) vessel which works at low pressure (4 bar, maximum) where gases are removed from the aqueous stream and replaced with dissolved oxygen. The resulting oxygenated aqueous stream is stable, allowing the target organisms to benefit from the prolonged exposure to high levels of bio-available oxygen.
Water temperature is another condition that typically restricts the ability of traditional aeration or gas transfer processes to achieve supersaturation. Due to Gas Infusion’s high oxygen transfer efficiency and the ability to achieve saturation levels above 100 mg/L or 100% saturation, the technology is still able to achieve supersaturation levels in high-temperature environments. The systems can be designed to recirculate a portion of volume of a vessel to maintain targeted supersaturation levels, thus maintaining the energy efficiency of the process. Additionally, the system can be cycled on and off to maintain oxygen levels while reducing energy usage further during off-peak times.
The Gas Infusion modules encompass hundreds of microporous hollow fibres arranged in bundles forming a single module. The modules are then arranged in arrays to increase the amount of dissolved gas a system can deliver in a twenty-four hour period. Figure 3 shows some details of Gas Infusion modules and arrays. The photomicrograph on the left shows a bundle of hollow fibres and the micropores that make up the wall of the fibres.
Figure 3: Details of micro-porous hollow fibres, Gas Infusion modules and arrays
The key hypothesis tested at the two pilot plants described below is the addition of the supersaturated flow to other streams (like raw wastewater), as Gas Infusion is able to promote the oxygenation via mono-phase mixing, (liquid to liquid) in a stable and efficient manner regarding energy consumption, while obtaining the required BOD reduction in an activated sludge process scheme.
Pilot plant trials
Two trials were conducted in Canada and Brazil in partnership with wastewater utilities to demonstrate the Gas Infusion technology capabilities regarding the treatment of domestic wastewater.
Pilot #1: Gas Infusion Technology at South East Oakville Wastewater Treatment (SEOWWTP), Canada – March, 2011 to March, 2012
The Government of Canada through the Climate Change Action Fund (CCAF) supported the Gas Infusion wastewater pilot project, and a complete report was developed (Jonasson 2012). The main objectives of this trial were to:
- Ascertain that the technology is able to effectively infuse oxygen into wastewater.
- Quantify the potential power savings with respect to a reference wastewater treatment plant.
The project has effectively completed two phases over a twelve-month period: Phase 1 - Bench Scale Testing and Phase 2 - Pilot Scale Side Stream Testing.
Both the bench scale and small-scale pilot testing was carried out as a side stream to the South East Oakville Wastewater Treatment Plant in Ontario, Canada, where all sample results were determined by the plant’s laboratory.
Phase 1 consisted of tests to determine the biological oxygen uptake rate, the oxygen transfer rate and BOD reduction over time. The Gas Infusion system was designed to mix supersaturated amounts of water into the primary effluent to reduce the BOD to the discharge levels and determine oxygen transfer rates. In each test, two oxygen transfer rates were determined: the gross oxygen transfer rate, or the rate that would occur if there were zero biological activity in the test fluid, and the net oxygen transfer rate, or the rate that is observed by the dissolved oxygen (DO) probe readings. The difference between these two rates is the minimum biological oxygen uptake rate.
Results show that oxygen was effectively transferred into the primary effluent, mixed liquor, and final effluent. The transfer rate is a controlled variable and can be set to meet the oxygen uptake demands of the primary effluent, mixed liquor and final effluent. Standard five-day carbonaceous biological oxygen demand tests (BOD) were done to determine the BOD reductions and the biological oxygen demand of primary effluent was effectively reduced.
It’s important to observe that the actual SEOWWTP process promotes the aeration of the mixed liquor using blowers and diffusers and consists in a typical treatment method for BOD reduction. For this current conventional method treatment, the SEOWWTP was achieving a rate of 0.125 mg BOD reduction per 1 mg oxygen injected through the air diffusers in a gaseous bubble form.
Nonetheless, at the bench side stream pilot using Gas Infusion, results demonstrated in many tests that up to 2.1 mg of BOD reduction per 1 mg oxygen injected was achieved in a completely dissolved bubble-less form.
This shows that the BOD reduction efficiency was significantly higher than the conventional aeration method used at that plant. Important to note that, during the bench phase, BOD reduction was achieved in primary effluent without the help of activated sludge, meaning that no return sludge was used to help effect the biological degradation of the effluent. It should be also noted that the system was only transferring approximately 70% of the oxygen introduced by Gas Infusion saturator. This was due to the inefficiency of the downstream valve used at the time of the first pilot. However, BOD levels were consistently reduced to less than 10 mg/l with primary influent BOD ranging from 80 to 90 mg/l (88% BOD reduction, as average).
Phase 2 consisted of a side stream pilot plant constructed to test the suitability of using Gas Infusion to treat primary effluent on a continuous basis, which is similar in design to the main treatment plant. A schematic of the pilot plant is shown in Figure 4.
Figure 4: Side Stream Pilot Plant Design – SE Oakville WWTP
Figures 5, 6, 7 and 8 show the side stream Gas Infusion Pilot plant details and installation pictures.
Figure 5: Gas Infusion side stream plant container
Figure 6: Gas Infusion liquid saturators (ILS)
Figure 7: Oxygenation Tank
Figure 8: Clarifier Installation
Although the pilot plant was designed for a flow rate of 16 liters per minute (primary effluent + oxygenated liquid) tests were run at different rates. Some consolidated results regarding BOD reduction and oxygen supplied are shown in Table 1. It’s important to note the pilot’s high capability to infuse oxygen: concentration average obtained was 126 mg of oxygen per liter of oxygenate flow.
Table 1: Pilot Plant BOD reduction and Gas Infusion Oxygen supply
The pilot report (Jonasson 2012) indicates that by increasing the amount of oxygen supplied to meet more of the oxygen demand, the final effluent BOD would be reduced to the required regulatory level. It’s important to emphasise that at that point, all tests were run without the addition of return activated sludge.
This statement was confirmed as more tests were run in the remaining Phase II work using then runs with the addition of return activated sludge (RAS). The addition of return activated sludge had a very significant impact on the quality of the final effluent. Total BOD averaged 17 mg/L and 22 mg/L for the periods when RAS was added, which is approximately 50% of previous BOD results without RAS. The soluble BOD obtained was well below the SEOWWTP target of 15 mg/L. TSS of the final effluent was also significantly reduced.
The theoretical plant effluent BOD calculated as a conventional activated sludge process and the actual experiment BOD were very similar suggesting that the Gas Infusion wastewater oxygenation treatment had almost 100% oxygen utilisation efficiency, meaning that almost all oxygen added is utilised and a minimum volume was lost to atmosphere.
The following Table 2 shows the hydraulic retention times (HRT) in the oxygenation tank and clarifier over a range of flow rates – showing that Gas Infusion worked consistently for a large range of HRT.
Table 2: Gas Infusion Pilot Plant detention times (Jonasson 2012)
The pilot plant data obtained during Phase II also demonstrated a potential operational power reduction by using Gas Infusion as the oxygenation method comparing with the existing conventional aeration units (with blowers/diffusers). The complete data report may be visualised at reference (Jonasson 2012). In summary, the key performance indicators of SE Oakville WWTP and Gas Infusion Pilot Plant can be compared as follows:
- South East Wastewater Treatment Plant aeration system: 330 kW per megaliter per Day treated (MLD);
- Gas Infusion Pilot Plant: 60 kW per megaliter per day treated (MLD);
Pilot # 2: Plant of Gas Infusion Technology at Flores Wastewater Treatment – Rio Claro, Brazil – under operation since October 2019
This pilot plant was developed by Prosper Technologies (Gas Infusion’s patent owner) in partnership with one of the largest private water utility companies of Brazil. The companies have designed, built, and equipped the plant, which has been operating a since 2019. This pilot plant works in parallel with a medium-sized plant - Flores WWTP with actual flows varying from 250 to 360 m3/h (or 6 MLD to 8.6 MLD, respectively).
The pilot plant consists in a typical activated sludge scheme with a biological reactor, a high lamellar rate clarifier, a recycle activated sludge unit (RAS), a waste activated sludge unit (WAS), besides the Gas Infusion oxygenation unit itself. The plant is fed with effluent from an up-flow anaerobic reactor (UASB).
The plant has the following characteristics:
- Gas Infusion Pilot Plant Influent Flow (Q): range of 30 to 60 Liters/minute or 1,8 m3/h to 3,6 m3/h, receiving from an existing UASB;
- Biological reactor volume: 26 m3 – Hydraulic detention time 7,8 to 3,9 hours (considering only influent flow);
- Recycled Activated Sludge (RAS): 0,5 to 1 times the Influent Flow (Q);
- Wasted Activated Sludge (WAS): maximum 0,5 times the Influent Flow (Q);
- Lamella Clarifier: horizontal operational rates from 26 to 54 m3/m2 per day;
- Influent BOD: 100 to 220 mg/l (domestic sewage);
The initial goals of the Gas Infusion side stream pilot carried out at the Flores WWTP were (during the period October 2019 to October 2021):
- To prove Gas Infusion capability to consistently oversaturated the influent with oxygen levels over 60 mg/l and control the oxygen plant requirements and seasonal/daily load and flow variances.
- To evaluate BOD reduction for many scenarios of oxygen introduction, influent and recirculation flows.
- To evaluate maintenance requirements for Gas Infusion units.
A simple process scheme of the pilot plant may be visualised in Figure 9. It encompasses two Gas Infusion Liquid Saturators or simply ILS:
- ILS #1: introducing oxygen direct into the raw influent;
- ILS #2: introducing oxygen into the mix liquor in a recirculation flow (RF) circuit. The mixing of the supersaturated stream in the biological reactor is made by simple perforated PVC pipe grid and nozzles.
Figure 9: Gas Infusion scheme at Flores WWTP
After 5 months of trial and many protocols tested, it was concluded that just one ILS (#2) was required to supply the oxygen requirement to maintain the dissolved oxygen ranging from 1 to 2 mg/l into the biological reactor. After process stabilisation and activated sludge growth, the recirculation flow varied from 1 to 3 times the influent flow (Q). The Gas Infusion ILS #2 was able to produce a consistent supersaturated stream with oxygen concentration over 60 mg/l – as indicated in Figure 10 that shows the collected data of the Gas Infusion SCADA system.
Figure 10: Gas Infusion SCADA screens
The results in terms of BOD reduction from 2020 to 2022 may be visualised in Table 3. It’s important to emphasise that all laboratory analysis were made by an independent third-party lab (Merieux Laboratories) using as BOD analytical method according to Standard Methods (SMWW – 23rd Edition – Method 5210).
Table 3: BOD values at Gas Infusion Pilot Plant in Brazil
Figure 11 below consolidates the data of influent and effluent BOD and the respectively percentage of removal from February 2020 to March 2021 – the period considered for process stabilisation. This period encompasses three distinct phases:
• February 2020 to June 2020: pilot commissioning/start-up and sludge creation.
• July 2020 to November 2020: recirculation flows and ILS adjustments.
• November 2020 to September 2021: normal operation.
Figure 11: BOD removal graphs from February 2020 to September 2021
It’s important to emphasise that the BOD removal efficiency variation occurred during the implementation phases are likely due to many variables as follows:
• The actual variation on influent BOD and the pre-treatment efficiency.
• The temperature variation on site – raging with averages from 18 C to 25 C.
• Some “trial and error” operational changes on the recirculation flows of the oversaturated stream.
Figure 12 shows some pictures of the pilot plant.
Figure 12: Gas Infusion Brazilian Pilot Plant – pictures of units
The pilot plant has received upgrades in March 2022 with a new positive displacement recirculation pump, a large oxygen generator and new dissolved oxygen probes. In this current phase, the pilot plant is determining what nitrification rates and ammonia conversion could be achieved and continue to develop an understanding of the way the process operates, what maintenance is required and what operator input is required.
Another point to emphasise is that from its very beginning, the demonstration plant required minimum maintenance. For instance, after 2 years of operation, a membrane module was extracted for evaluation and required a simple pressure jet washing to be put under operation again.
Discussion
Both pilots successfully proved Gas Infusion’s capability to produce over-saturated oxygen liquid streams in a stable way with average concentrations obtained ranging from 60 to 120 mg O2/L approximately.
The utilisation of the over-saturated oxygen stream as a vehicle to introduce oxygen into a biological reactor and the hydraulic mixing promoted with the influent flow of a wastewater treatment plant, also showed the ability to maintain a desirable dissolved oxygen concentration (range from 1 to 2 mg/l) in the pilot biological reactors.
Therefore, for both pilots, the expectation of having the biokinects similar or better than a conventional activated sludge process with aeration and then promote similar or better organic load reduction in terms of BOD, was also proved.
The key performance indicators extracted from the pilots seemed to be very promissing:
- The SEOWWTP pilot, even with tests with a limited capacity of oxigenation transfer (due the control valves), obtained a rate of oxygen introduced per BOD reduced always less than 1 Mg O2/ Mg BOD. With the introduction of RAS, the effluent quality improved and achieved a soluble BOD average from 17 to 22 mg/l.
- At the Flores WWTP pilot, the extensive period of tests showed a reliable capability of BOD reduction (over 85%) using Gas Infusion as the oxygenation system working in a typical activated sludge process scheme. The results of testing in that small-scale pilot have provided sufficient proof of concept and validation of the technology and may determine significant benefits over conventional aeration technology.
The Gas Infusion value proposition in terms of CAPEX is based on replacement of all types of conventional aeration (like blowers and diffusers) by a simple scheme of recirculation pump, on-site oxygen generator and zero-energy membrane modules vessels. Therefore, for an accurated economic evaluation of expected CAPEX reduction, all those items should be analised and quoted for each specific project location.
In terms of OPEX, it is likely correct to assume that Prosper’s Gas Infusion technology based on pure oxygen introduction will be more efficient than conventional aeration technology based on blowers and diffusers. In fact, many other studies have already been carried out in this direction, which indicate that the amount of oxygen that can be injected into the liquid (for a specific set of conditions) is approximately four times the amount that could be injected with an air system (Shammas and Wang 2008).
Regarding the maintenance requirements, the pilots indicated that, as Gas Infusion process membrane modules do not perform any physical filtering, no biofilm was created along ther fibres, and it did not require clean in place (CIP) or backwashing.
Therefore, it can be assumed that the expected preventative maintenance of a Gas Infusion system will be summarised as follows:
- Typical maintenance of low rotation hydraulic pumps;
- Maintenance of oxygen generators, which are generally hospital grade and have extremely low downtime;
When comparing this situation with the typical maintenance required by conventional aeration units, which require high-speed blowers, industrial valves and drives and a large number of diffusers, it becomes very likely that the Gas Infusion system implies a significant reduction in maintenance costs and overall OPEX. However, for a precise assessment, for each plant to be designed or retrofitted, it is necessary to carry out comparative studies on a case-by-case basis.
It’s important to emphasise in this discussion that pure oxygen utilisation at wastewater treatment plants is not a new technique and has been used with success in many plants around the world (Metcalf and Eddy 2003). Additionally, many issues regarding supersaturation of liquids and effluents with oxygen have also been extensively tested and many myths have been debunked (Speece 2006).
Other authors have also evaluated the direct use of dissolved oxygen in sewage treatment in comparison with conventional aeration systems. Skouteris, Rodriguez-Garcia, Reinecke and Hampel (2020) indicated some limitations of conventional aeration in typical activated sludge process treating high strength wastewaters. By replacing air with pure oxygen, they concluded that oxygen transfer can be increased, making it possible to treat higher loadings without compromising effluent quality.
Therefore a deeper understanding of this new sewage treatment technology requires a gradual and step-by-step approach. Thus, aiming at the implementation of a treatment plant, it is suggested to initially address the Gas Infusion oxygenation solution for small to medium-sized plants (1 to 5 MLD). Naturally, the executive project must include additional hydraulic and process analysis, such as Computer Fluid Dynamics (CFD) and process modeling, for determining volumes and shapes of biological reactors with different sludge ages and solids concentrations, among other variables.
Conclusion
The primary goals of the pilot plants proved the hypothesis regarding Gas Infusion capability of oxygen dissolution, its reliability, BOD removal accomplishments (over 85%) and minimal maintenance requirements.
Using Gas Infusion as primary oxygen introduction solution at wastewater treatment plants is likely to determine a significant reduction of CAPEX comparing to conventional aeration systems. Gas Infusion, as a new aeration technology, does not require expensive equipment like blowers, diffusers, stainless steel pipes, industrial air valves and actuators, mechanical aerators and mixers, that are typical components used in conventional activated sludge plants or aerated oxidation ponds.
The Gas Infusion solution built around a core technology of an industrial scale oxygen transfer system utilising a mass transfer module containing micro-porous hollow fibres (MHF) produces a stable interface for mass transfer with high transfer efficiency of oxygen in actual conditions. Gas Infusion has a unique method of dissolving gas into liquids with rapid effect as it creates over-saturated streams where the oxygen concentrations may achieve hundreds of parts per million. Gas Infusion is a technology developed by Prosper Technologies which is a vertically integrated nanotechnology company that owns an intellectual property portfolio of several other Gas Infusion patents.
As result of the pilots presented, it can be seen that Gas Infusion technology may be applied for domestic wastewater treatment, both as a “greenfield” design or for the upgrade of conventional activated sludge (CAS) plants attending increasing flows and organic loads.
Acknowledgements
We would like to acknowledge the contributions of SE Oakville WWTP utility employees in assisting us at the demonstration pilot in Canada.
The Authors
Max Mackenzie, CEO
Serial entrepreneur with over 30 years experience building and managing businesses, and particular experience in IP-rich businesses. Currently based in Miami.
Giancarlo Ronconi, VP Business Development
Experienced engineering executive with over 40 years of experience in the global Water/ Wastewater Municipal and Industrial markets. Currently based in Australia.
Andre Monutti, Director, Technology
Chemical Engineer with 11 years of experience in water and wastewater plant design, operation, start-up and commissioning, for both municipal and industrial facilities.
Wade Campbell, CTO
Inventor and technical problem solver wit 30 years of experience in designing/developing innovative solutions in environmental and manufacturing industries. Based in Canada.
References
Jonasson, K 2012, ‘Development & demonstration of Gas Infusion Technology for Wastewater treatment’, Technical Report, Public Works & Government Services Canada
Metcalf and Eddy Inc., Tchobanoglous, G, Burton, F L, Stensel, H. D. 2003, ‘Wastewater Engineering Treatment and Reuse – 4th edition’, pages 448, 747, McGraw-Hill, Boston, MA
Shammas NK, Wang LK 2008, ‘Handbook of Environmental Engineering Volume 8: Biological Treatment Process’, Chapter 7,The Humana Press, Totowa, NJ
Skouteris G, Rodriguez-Garcia G, Reinecke SF, Hampel, U 2020, ‘The use of pure oxygen for aeration in aerobic wastewater treatment: a review of its potential and limitations’, Technical Paper, Bioresource Technology
Speece, R E 2006, ‘Super-oxygenation: Facts and Myths’, Technical Paper, Vanderbilt University, Nashville, TN