Are PFAS an Issue for Permeation of Plastic Water Pipes?
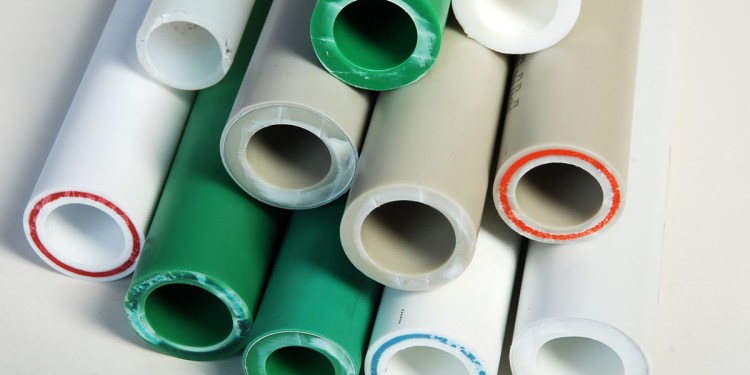
An investigation into potential drinking water contamination.
DOWNLOAD THE PAPER
Abstract
Plastic pipes have been used increasingly for conveying drinking water in distribution systems. Factors favouring the use of plastic pipes include their ease of installation and handling, durability and good resistance to the chemicals used in water treatment, such as chlorine. However, organic contaminants in soil may permeate/penetrate through plastic pipes and adversely affect the quality of drinking water in a reticulation system. These contaminants include volatile hydrocarbons and chlorinated organic solvents.
With attention being given to PFAS (Per- and Poly-Fluorinated Alkyl Substances) as an emerging contaminant, the possibility of drinking water contamination has increasingly become a concern. In this regard there has tended to be a focus around potential source water contamination, rather than possible contamination through localised permeation of reticulation pipe networks.
This paper describes an investigation of the latter scenario from two aspects. The first being a review of the mechanism of permeation, the chemical nature of plastic pipes and their organic permeants, as well as a consideration of chemical properties of PFAS molecules and their likelihood to be permeants of plastic pipes. The second aspect describes a six-month laboratory-based trial, jointly commissioned in 2018 by City West Water (CWW), South East Water (SEW) and Yarra Valley Water (YVW), into possible permeation of HDPE pipe by 29 (of the greater than 6,000) PFAS compounds.
Based on the findings from the two aspects considered (theoretical and practical) it would seem that PFAS compounds are unlikely to be a water contamination issue in terms of permeating undamaged HDPE (and PVC) plastic pipe.
Introduction
Plastic pipes have been used increasingly for conveying drinking water in distribution systems, for which they are often the preferred materials. A significant factor for the increased use of plastic pipes is their ease of installation and handling. In addition, plastic pipes are highly durable and offer good resistance to the chemicals used in water treatment, such as chlorine.
In urban areas, plastic pipes can come into contact with contaminated soils as a result of chemical spills and improper disposal of used chemicals. When organic contaminants (e.g. solvents, petroleum compounds) are present, they may permeate/penetrate through plastic pipes and adversely affect the quality of drinking water in a reticulation system (USEPA 2002). When this type of contamination occurs, it is often detectable by consumers, as many of the compounds produce strong odours at low concentrations (WHO 2014).
Although volatile hydrocarbons and chlorinated solvents are non-aqueous phase liquids, their limited solubilities in water can be sufficient to compromise compliance with drinking water standards/guidelines. The plastic pipe materials involved include polybutylene, polyethylene (PE) and polyvinyl chloride (PVC). Contaminants of interest include volatile hydrocarbons (e.g. as found in petroleum, such as benzene) and chlorinated organic solvents (e.g. degreasing agents, such as trichloroethane).
In recent decades there have been increasing concerns over the globally widespread presence of PFAS (hydrocarbon molecules with fluorine in place of most or all of the hydrogen atoms) in the global environment, including aquatic ecosystems, as well as human and wildlife tissues. This, together with suspected adverse health implications, has led to concerns over potential presence of PFAS in drinking water and the development of precautionary maximum guideline levels (WaterRA 2017).
In view of the known permeability of plastic pipes by hydrocarbons, this paper examines the potential for PFAS compounds to penetrate plastic pipe. This is done from two aspects. The first being a desktop review of the mechanism of permeation, the chemical nature of plastic pipes and their organic permeants, as well as a consideration of chemical properties of PFAS molecules and their likelihood to be permeants of plastic pipes. The second aspect describes a six-month laboratory-based trial, jointly commissioned in 2018 by City West Water (CWW), South East Water (SEW) and Yarra Valley Water (YVW), into possible permeation of HDPE pipe by 29 (of the greater than 6,000) PFAS compounds.
Permeation (penetration)
Permeation of piping material is defined as the passage of contaminants external to the pipe, through porous, non-metallic materials, into the drinking water.
Typically, the permeation of contaminants through plastic pipe involves three processes (Mao 2008; Mao et al 2015):
- partition of the contaminant between the outer surface of pipe and the medium containing the contaminant (sorption);
- diffusion of the contaminant through the amorphous areas of polymer pipe material; and
- partition between the inner surface of pipe and the water in the pipe (desorption).
Depending on soil contaminant concentrations, permeation of PE and PVC pipes can occur within a matter of days/weeks (Mao 2008).
Permeation is specifically influenced by (i) the structural characteristics of the polymer material (density, crystallinity, thickness, degree of crosslinking, chain rigidity); (ii) the chemical activity (concentration) and molecular characteristics (weight, size, shape) of the organic contaminant and its chemical similarity to the polymer; and (iii) soil characteristics. Other environmental factors, such as temperature, hydraulic gradient, and ageing of pipe materials may also impact permeation. (Mao et al 2015).
USEPA (2002) reports on incidents of drinking water hydrocarbon contamination resulting from permeation of subsurface mains and fittings. The occurrence of permeation incidents was equally split between high-risk locations such as industrial areas, former sites of fuel stations and storage tanks; and low-risk locations such as residential areas. The sources of contamination for low-risk areas included disposal and accidental leaking of petrol, oil and paint thinners. Plastic pipes were involved in almost all cases. High rates of permeation included diesel and petroleum products, volatile chlorinated solvents, simple chlorinated aromatics, chlorinated and unchlorinated straight-chain aliphatic hydrocarbons and phenolics.
Chemical structure of polyethylene (PE) and polyvinyl chloride (PVC) water pipes
PE is a polymer of the ethylene monomer:
The non-polar chains are attracted to each other by relatively weak dispersion forces but, because of the length of the chains, these intermolecular forces become significant.
PVC is a polymer of the vinyl chloride (chloroethene) monomer (CH2CHCl):
The polar molecule chains are attracted to each other by dipole-dipole interactions due to electrostatic attractions of a chlorine atom in one molecular chain to a hydrogen atom in another chain.
Due to fundamental differences in the polymer structures, PE and PVC exhibit different permeation behaviour. Permeation by a contaminant is expected to decrease with increasing density, chain rigidity, and degree of cross-linking. New PVC pipes exhibit lower permeation rates than new PE pipes, primarily due to differences in the material matrices (USEPA 2002). For example, PVC is an amorphous glassy polymer with very limited flexibility of the polymer chains, while PE is a partially crystalline rubber-polymer having amorphous areas with high chain mobility.
Small organic molecules permeate PVC through the small free volumes between the relatively immobile polymer chains, whereas permeation of PE occurs through the amorphous areas having relatively more mobile polymer chains. This structural difference accounts for the different performance between PE and PVC to resist permeation by organic chemicals. Penetration through high density PE is less than for low density PE due to the greater crystallinity of high-density PE. At high concentrations of pollutants, such as in a gross spillage situation, swelling of PVC by solvents may cause rapid penetration through the PVC pipe wall.
For practical purposes, there is no level of contamination at which PE pipe is resistant to permeation by gasoline, chlorinated solvents or hydrocarbons or aqueous solutions of gasoline, chlorinated solvents or hydrocarbons. Corrective action should be undertaken whenever there is a known spill of gasoline or organic solvents, hydrocarbons in the vicinity of a PE service line (Ong et al 2007). Petroleum products are complex mixtures of hundreds of hydrocarbon compounds, ranging from light (low molecular weight), volatile, short-chained organic compounds to heavy, long-chained, branched compounds. The exact composition varies depending on the source of crude oil and refining processes. Consistent components of petroleum hydrocarbons are the BTEX group – benzene, toluene, ethylbenzene and xylene.
Permeation through PVC pipes has generally been assumed to be negligible for low concentrations of hydrocarbons such as BTEX and chlorinated solvents such as trichloroethane in soil (DWI0772 1997). Ong et al (2007) considers PVC pipe to be impervious to “gasoline” and gasoline saturated solutions, due to the low level of BTEX present. However, this can change if conditions of stagnation and contact with neat free hydrocarbon and chlorinated solvent product occur (Ong et al 2007). In the presence of high levels of organics which are good solvents for PVC (e.g. chlorinated hydrocarbons, BTEX), the polymer can become swollen. Diffusion rates increase markedly through the swollen material and the pipe can be rapidly permeated within months, weeks or days. This is most likely to happen where gross spillage of solvents has occurred (DWI0772 1997).
Chemistry of plastic pipe permeants (penetrants)
Hydrocarbons are molecules/compounds consisting of only hydrogen and carbon and are commonly found in petroleum, natural gas and bitumen. There are two classes: aliphatic hydrocarbons are non-cyclic, with a linear structure that may have branches; and aromatic hydrocarbons which contain a stable ring of atoms, such as benzene. Hydrocarbons are non-polar, even when branched.
Chlorinated solvents are usually composed of one or two carbon atoms with up to six chlorine atoms covalently bonded. The chlorinated solvents are commonly used for dry cleaning operations, solvents for fats, engine cleaning, degreasing agent, paint removers, etc. They are generally considered as non-polar.
Besides the structural characteristics of plastic polymer, the chemical activity (concentration) and molecular characteristics of organic contaminants influence the permeation of organic compounds through polymeric materials. It has been shown that in most polymer-penetrant systems, both diffusion and permeation coefficients exhibit a general increase when there are similarities in molecular structures between the penetrant molecules and the polymer materials.
For instance, strongly polar molecules have very low transport rates through PE, which is non-polar. Polar molecules such as alcohols and acids exhibit lower permeation affinity for PE, compared with (non-polar) aromatic hydrocarbons and halogenated hydrocarbons (Mao 2008). Therefore, contaminants most likely to permeate plastic are non-polar (and lipophilic), however, limitations due to other factors such as molecular weight, size (molecular volume), cross sectional area and chain length of the penetrant play a role (USEPA 2002).
As a molecule, water is considered to be strongly polar. PVC is a polar polymer; however, its waterproof nature is explained by a lack of OH groups that could form hydrogen bonds with water molecules.
Mao (2008) summarises physical characteristics of permeants and their bearing on permeation. For example:
- Permeation decreases with increasing molecular weight and size (molecular volume); and that the magnitude of the decrease is higher for chlorinated rather than methyl substituted chemicals due to the bulky chlorine atom.
- Penetrants having linear, flexible and symmetrical molecules have higher mobility than rigid molecules. For example, permeation by n-alkane (CnH2n+2) and other elongated or flattened molecules is much higher than for spherical (e.g. tetrahedral) molecules with similar molecular weight.
- Permeation rates decrease with increased “n” (number of carbon atoms on the alkane chain).
- Permeation rates increase with concentration of penetrant. This is because the greater presence of penetrant molecules weakens the interactions between adjacent plastic polymer chains, leading to plasticisation (softening).
The nature of soil surrounding the pipe can affect permeation. For example, plastic pipes buried in soil of high organic carbon content are permeated more slowly than those in soil of low organic carbon content (Mao 2008).
The majority of recorded permeation incidents occur with PE and polybutylene rather than PVC pipes (USEPA 2002). DWI0772 (1997) reviews the extent of organic chemical permeation problems in plastic pipes used for drinking water, finding that PB, PE and PVC pipes were involved in 43%, 39% and 15% of cases, respectively.
Typical organics found in the drinking water amongst these cases were:
- acetone
- benzene
- carbon tetrachloride
- chlorobenzene
- ethylbenzene
- tetrachloroethene
- toluene
- trichloroethene
- xylene
Some characteristics of the above-mentioned penetrants are summarised in Table 1.
Table 1: Characteristics of permeants
* Miller’s Home (https://sites.google.com/site/miller00828/in/solvent-polarity-table)
In the context of organic chemistry, the compounds shown in Table 1 are regarded as small molecules, for example, as compared with proteins and nucleic acids, which have molecular weights ranging in the hundreds to thousands.
In summary, the combined characteristics of PE and its hydrocarbon penetrants that cause PE to be permeated are as follows:
- PE, as a polymer of hydrocarbon molecules, allows for free interaction with hydrocarbon penetrant molecules.
- PE is non-polar, as are the relatively non-polar penetrant hydrocarbons.
- PE’s relatively mobile polymer chains with amorphous areas allow the small, non-polar hydrocarbons to penetrate.
PVC has lower permeability (than PE) due to:
- PVC’s chlorinated molecules forming a glassy (brittle) amorphous polymer with very limited flexibility of the polymer chains. Small organic molecules can permeate PVC through the small free volumes between the relatively immobile polymer chains, but to a much lesser extent than with PE.
- PVC consisting of polar molecules that tend not to interact with the non-polar hydrocarbons.
Chemical considerations of PFAS molecules
PFAS (per- and polyfluoroalkyl substances) are a family of man-made chemicals (>6,000) that contain carbon, fluorine and other elements. All PFAS contain a chain of carbon atoms (typically 2 to 16 carbon atoms, sometimes branched) bonded to fluorine atoms. Some also have a functional group at the end of the chain. These structures are the basis for different chemical properties and different chemical names. In perfluoroalkyl substances all carbons (except those associated with functional groups) are attached to fluorines; the last carbon attaches to a functional group. In polyfluoroalkyl substances at least one (but not all) carbon is attached to fluorines (Concawe 2016; Buck et al 2011).
The covalent carbon-fluorene bond is one of the strongest bonds in organic chemistry due to the effective overlap of the molecular orbitals involved in the bond. The dense packing of fluorene electrons also acts as a “shield”, protecting PFAS from degradation, thus causing the high thermal, chemical photolytic (UV-radiation) and biological stability of these materials (Concawe 2016).
PFAS are chemically very stable with surface tension/levelling properties. Uses include inks, varnishes, waxes, water and oil repellents, fire-fighting foams, and lubricants. PFAS have the ability to repel both oil and water, leading to their use in stain guard products. The ability of PFAS to form an aqueous film that will wet and flow across the surface of liquid hydrocarbon has led to their application in high performance fire-fighting foams at facilities handling large volumes of flammable liquid hydrocarbons (Concawe 2016, USEPA 2017).
In general, the better known PFAS consist of a hydrophobic poly- or perfluorinated carbon chain and a hydrophilic functional group consisting of, for example, sulphonate or carboxylate or other salts. This amphiphilic (both hydrophobic and hydrophilic) characteristic of PFAS makes them ideal for use as surfactants. However, in contrast to conventional surfactants, the perfluorinated backbone is also lipophobic, which renders many PFAS coatings resistant not only to water but also to oil, grease, other nonpolar compounds and dirt particles (Buck 2011).
PFOA and PFOS have been the most extensively produced and studied of the PFAS chemicals. Both chemicals are very persistent in the environment and in the human body. Besides consisting of carbon and fluorine atoms, some PFAS also include oxygen, hydrogen, sulphur and/or nitrogen atoms (USEPA undated).
PFOS and PFOA are distributed across all biota trophic levels and found in soil, air, surface and ground water across the world (USEPA 2017). Most perfluoroalkyl acids (e.g. PFOS, PFOA) are present in environmental and human matrices in their anionic form and are reasonably soluble (g/l range) due to the hydrophilic carboxylate and sulphonate groups. The variability in alkyl chain length and functional group charge means that the behaviour of PFAS compounds is not readily generalised (USEPA 2018).
A brief comparative summary of physical/chemical characteristics of PFAS (PFOA, PFOS) and two typical plastic penetrant hydrocarbons is shown in Table 2.
Table 2: Physical/chemical properties of PFOA, PFOS (USEPA 2017), trichloroethene and benzene
Based upon the above and preceding discussed physical/chemical characteristics of PE, PVC, plastic permeants and PFAS, an assessment is made in Table 3 of likely permeation of PE and PVC by PFAS.
Table 3: Summary of PFAS characteristics and bearing on permeability of PE and PVC
* Generally speaking, although PFAS are environmentally highly mobile and found globally (due largely to their water solubility), they are unlikely to be found in high concentrations throughout urban areas. They are, however, associated with primary and secondary manufacturing facilities, wastewater treatment sites, landfill, firefighting training sites, leaks from fire suppression systems (e.g. at airports) (USEPA 2017). On the other hand, hydrocarbons (including BTEX) can be (and are) found in high concentrations at localised sites throughout urban environments, let alone at industrial facilities. This is because permeant hydrocarbons are available to (and used by) the general population, for example, petroleum, paint products, paving sealants and bitumen. Localised application, discard or spillage, followed by plastic pipe permeation throughout suburbia is more likely to be an issue with hydrocarbons than for PFAS.
Based on this comparative assessment it seems unlikely that PFOA and PFOS would be an issue for penetration of PE and PVC plastic pipes. However, due to the varied chemical characteristics of the >6,000 PFAS chemicals, possible permeation by some PFAS cannot be excluded.
Trial of possible permeation of HDPE pipe by PFAS
Up until now, this paper has considered plastic (water) pipe permeation in terms of plastic pipe, organic permeant and PFAS chemistry, with the aim of making a desktop assessment of whether PFAS are likely to also be a permeant of concern in urban water supply networks.
In an attempt to gain a practical insight into the permeation possibility, in 2018 CWW, SEW and YVW jointly commissioned ALS Lifesciences (Environmental) to undertake a laboratory-based trial to investigate if high density (HD) PE pipe could be penetrated by PFAS. PE pipe was selected for the trial (rather than PVC) as it is more subject to permeation. The actual pipe material used consisted of sections of new HDPE (PE100 polyethylene pipe for drinking water; DN25PE; as per WSAA product specification WSPS215 property service, which refers to AS/NZS 4130:2019) that is used by the three Victorian retail water corporations as service connections between reticulation water mains and customer meters. The PFAS-containing material in which pipe sections were immersed was a 3% (by weight) solution of Aqueous Film Forming Foam (AFFF) concentrate supplied by 3M Company (product identifier: 3M(TM) Fire Barrier Rated Foam FIP 1-Step KIT).
The trial commenced in May 2018 and involved a six-month exposure period, with internal pipe sections’ water contents analysed at time zero, one month, three months and six months. In summary, the trial comprised four sets of test scenarios (see also Table 4):
a.) Duplicate, sealed pipe sections containing reagent water, immersed in trays containing 3% AFFF – total of six pipes.
b.) Duplicate, sealed pipe sections containing reagent water, adjacent to the 3% AFFF-containing tray (to monitor potential for vapour transfer of PFAS through the sealed ends of the pipes) – total of six pipes.
c.) Duplicate, sealed pipe sections containing reagent water, in an empty tray, but remote from the 3% AFFF-containing tray (to monitor possible background PFAS in the pipe sections and sealing caps) – total of six pipes.
d.) Reagent water blank controls.
Table 4: Summary of HDPE PPFAS immersion trial
The pipe sections were approximately 50 cm in length and retained the “natural” curvature of the HDPE roll from which they were cut. The curvature allowed for the middle section of the pipes to be immersed with each sealed end sitting out of solution. Figure 1 shows the configuration of the immersed and adjacent pipe sections. Figure 2 shows the remotely placed pipe sections.
Figure 1: One of two sets of three HDPE pipes immersed in 3% AFFF (top) and three adjacent control pipes (bottom)
Figure 2: Remotely located control pipe sections
Four classes of PFAS were analysed (total of 29 PFAS compounds) as shown in Table 5.
Table 5: Classes of PFAS analysed during the permeation trial
Trial results
May 2018 (time zero)
The trial apparatus set up was completed on 1 May 2018 when first testing was undertaken. First tests were of the reagent water used to fill the pipe sections. Results showed PFAS concentrations below detection levels (0.002µg/L or 0.005µg/L, depending on the individual PFAS compound). Quality control analyses were undertaken for PFAS-spiked reagent water to check for recovery of the PFAS analytes in order to confirm that the testing was indeed capable of detecting PFAS. Recovery levels were deemed satisfactory. Spiking with AFFF itself was not specifically undertaken as part of this trial. However, ALS Lifesciences (Environmental) had quality control records (using the same testing methodology and equipment used in this trial) showing detection of the PFAS compounds in question from the same batch of AFFF.
June 2018 (1 month exposure)
On 1 June reagent water samples were obtained from within the pipes of test scenarios (a), (b) and (c), as well as the reagent water stock (d) used to top up the pipe contents, and tested for PFAS. All test results showed PFAS concentrations below detection levels (0.002µg/L or 0.005µg/L, depending on the individual PFAS compound). Quality control recovery of PFAS-spiked reagent water was deemed satisfactory.
August 2018 (3 months exposure)
On 1 August reagent water samples were obtained from within the pipes of test scenarios (a), (b) and (c), as well as the reagent water stock (d) used to top up the pipe contents, and tested for PFAS. All test results showed PFAS concentrations below detection levels (0.002µg/L or 0.005µg/L, depending on the individual PFAS compound). Quality control recovery of PFAS-spiked reagent water was deemed satisfactory.
November 2018 (6 months exposure)
On 1 November reagent water samples were obtained from within the pipes of test scenarios (a), (b) and (c), as well as the reagent water (d) used to top up the pipe contents, and tested for PFAS. With two exceptions, all other test results showed PFAS concentrations below detection levels (0.002µg/L or 0.005µg/L, depending on the individual PFAS compound). Quality control recovery of PFAS-spiked reagent water was deemed satisfactory.
The two exceptions where PFAS was detected (specifically, perfluorohexane sulphonic acid) related to one of the duplicate immersed pipes of scenario (a) and, one of the duplicate adjacent non-immersed pipes of scenario (b). Permeation and/or airborne transfer through the sealed pipe ends were considered unlikely due to absence of detections in respective duplicates. Furthermore, had permeation occurred, it might be expected that smaller PFAS molecules would also have been detected. For example, perfluorobutane sulphonic acid has a molecular weight of 300, compared with 400 for perfluorohexane sulphonic acid. It is therefore considered more likely that an analytical issue was responsible for the detections.
Conclusion
Based on the desktop analysis of chemical properties of plastic pipes, permeants and PFAS, it would seem that permeation of undamaged PE and PVC pipe by PFAS is unlikely (e.g. due to larger molecular size as compared with the volatile hydrocarbons). This tends to be supported by the six-month laboratory exposure trial of HDPE to potential permeation by 29 PFAS compounds. Despite minor, seemingly anomalous test results at six months, it is believed that permeation was not observed. It is tentatively proposed that PFAS are also unlikely to permeate PVC pipe, however, without conducting the same tests using PVC this remains an assumption. It must be remembered that the trial did not consider permeation by PFAS of chain length shorter than C4 that are consequently smaller molecules (for example, trifluoroacetic acid has a molecular weight of 114 g/mol, well in the range of the known organic permeants).
Acknowledgements
The authors thank City West Water, South East Water and Yarra Valley Water for providing the resources to undertake this study. In addition, we thank Steven McGrath of ALS Lifesciences (Environmental) for managing the laboratory trial.
About the authors
Georges Ruta (Lead Author) | Water Quality Scientist, City West Water Corporation. Over 40 years’ experience in water quality testing, research, operations, planning and management.
Anthea McManemin | Water Quality Manager, South East Water Corporation. Over 15 years’ experience in water quality management, planning and operations.
Asoka Jayaratne | Water Quality Specialist, Yarra Valley Water Corporation. Over 20 years’ experience in distribution system water quality management, planning and operations
References
behaviour) (Accessed 14 June 2019)